The transition from carbon steel to stainless steel when selecting a welding rod is a crucial consideration for industries demanding robust, reliable joints that withstand environmental and mechanical stressors. The compatibility of welding materials directly influences the integrity and durability of the joint, necessitating an informed choice rooted in professional expertise.
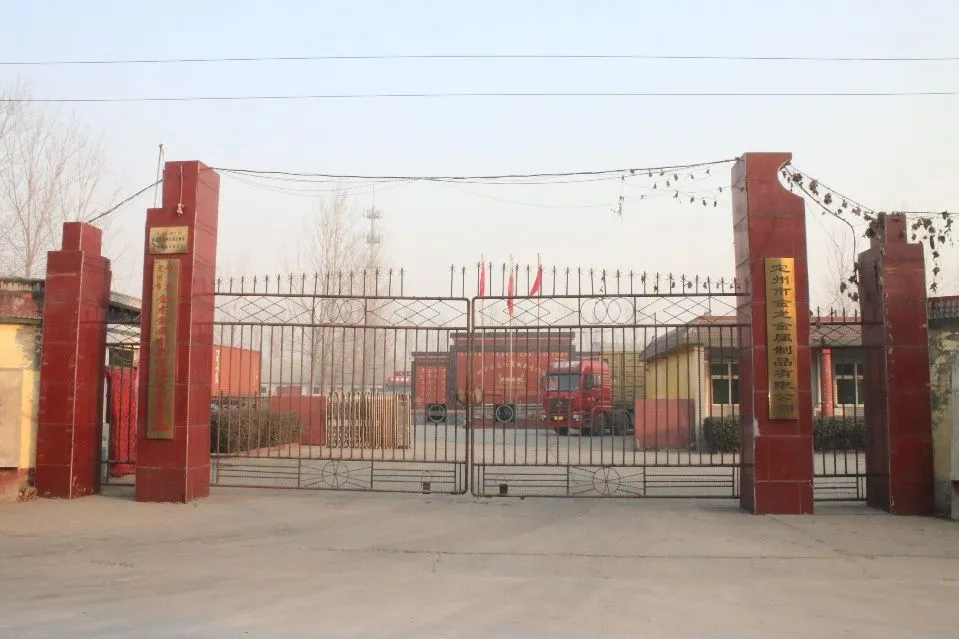
Carbon steel and stainless steel inherently exhibit distinct metallurgical properties. Carbon steel, favored for its high strength and affordability, lacks the corrosion resistance of stainless steel. Conversely, stainless steel offers excellent corrosion resistance, making it indispensable in high-demand applications such as chemical processing, food production, and architecture. The challenge lies in merging these materials without compromising their inherent benefits.
Selecting the appropriate welding rod is instrumental in achieving a seamless bond between carbon steel and stainless steel. The use of a dissimilar metal welding rod, such as 309 or 312 stainless steel electrodes, is often recommended. These electrodes bridge the metallurgical gap, ensuring a stable fusion zone that minimizes risks associated with thermal expansion differences and corrosion potential.
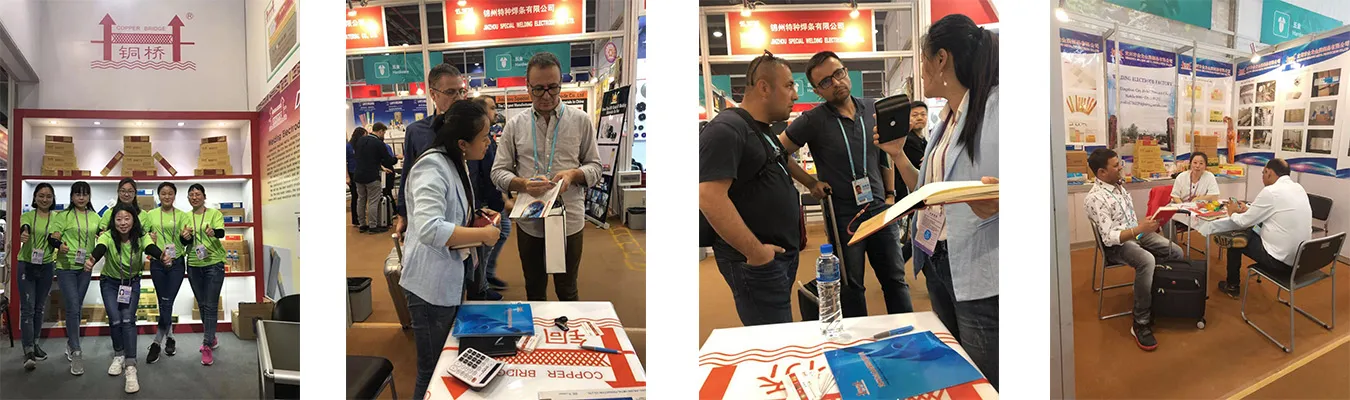
The 309 welding rod, renowned for its versatility, is a popular choice for welding carbon steel to stainless steel. Its composition includes chromium and nickel, which facilitates a stable arc and minimizes cracking during the welding process. This composition not only accomplishes successful fusion but also provides a robust weld with a balanced combination of strength and corrosion resistance. Meanwhile, the 312 welding rod is particularly effective in extreme environments due to its higher alloy content, offering exceptional resistance to cracking.
carbon steel to stainless steel welding rod
Application technique also crucially affects the outcome. Employing controlled heat input and inter-pass temperatures can mitigate the potential for thermal distortion and excessive dilution, particularly given the differing thermal conductivities and expansion coefficients of carbon and stainless steels. Achieving this typically requires advanced knowledge of welding procedures, which professionals acquire through experience and technical training.
Pre-welding preparation is another pivotal factor. Both metal surfaces must be carefully cleaned and free of contaminants that could compromise the weld integrity. This includes removing oxides, oil, and other surface impurities through grinding or chemical cleaning processes, thus ensuring optimal adhesion and penetration of the weld.
For welding practitioners, safety cannot be overemphasized. Utilizing appropriate protective gear, such as helmets with filter lenses, gloves, and protective clothing, is essential to safeguard against radiation and molten metal spatter. Additionally, proper ventilation systems must be in place to mitigate the risks posed by harmful fumes emitted during welding.
In conclusion, the process of welding carbon steel to stainless steel is an intricate task requiring specialized materials and methodologies to overcome the inherent differences in metallurgical properties. The choice of a suitable welding rod, such as 309 or 312, along with proper technique and preparation, ensures a joint that is both reliable and durable. By adhering to these practices, professionals in the field can achieve superior results, satisfying both structural and environmental demands. This expertise-driven approach not only enhances the quality of the final product but also reinforces the reputation of craftsmen and industries relying on these advanced welding solutions.