The 3/32 7018 welding rods represent a cornerstone in the field of welding, renowned for their versatility and efficiency in a myriad of applications. These electrodes, known scientifically for their low-hydrogen iron powder coating, offer exceptional usability across different sectors, making them a preferred choice among professionals. This article aims to provide in-depth insights into the features, applications, and best practices associated with the 3/32 7018 welding rods, enhancing understanding for professionals seeking authoritative and trustworthy information.
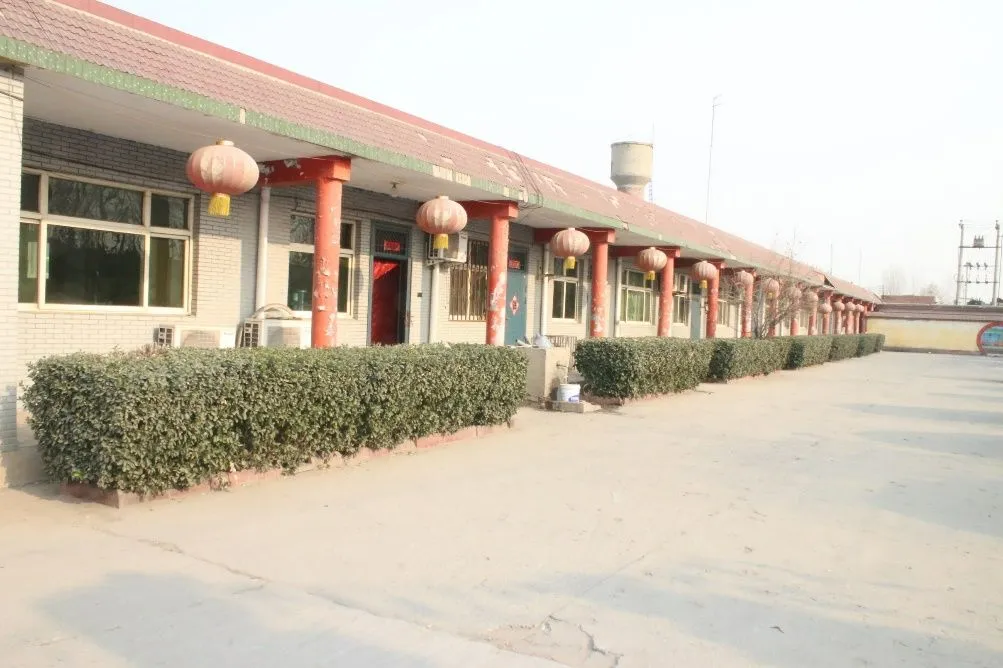
Firstly, the 3/32 7018 welding rods are particularly celebrated for their robustness and ability to produce high-quality welds with excellent mechanical properties. These rods are engineered to perform particularly well on carbon steel and low-alloy steel, enabling strong, ductile, and crack-resistant welds. Their low-hydrogen content significantly minimizes the risk of hydrogen-induced cracking, a critical factor when working on structural projects or pressure vessels. This quality underlines the rod’s reliability and positions it as an industry staple for construction and manufacturing professionals.
Moreover, the 7018 electrodes offer a smooth arc that is easy to control, even for less experienced welders. Their compatibility with both alternating current (AC) and direct current (DC) makes them highly adaptable to various power sources.
The 3/32 size is particularly suited for medium-thickness materials, providing the precise balance needed to avoid excessive penetration or lack of fusion. For welding professionals, this adaptability not only enhances their craftsmanship but also optimizes operational efficiency by reducing the need for multiple types of rods.
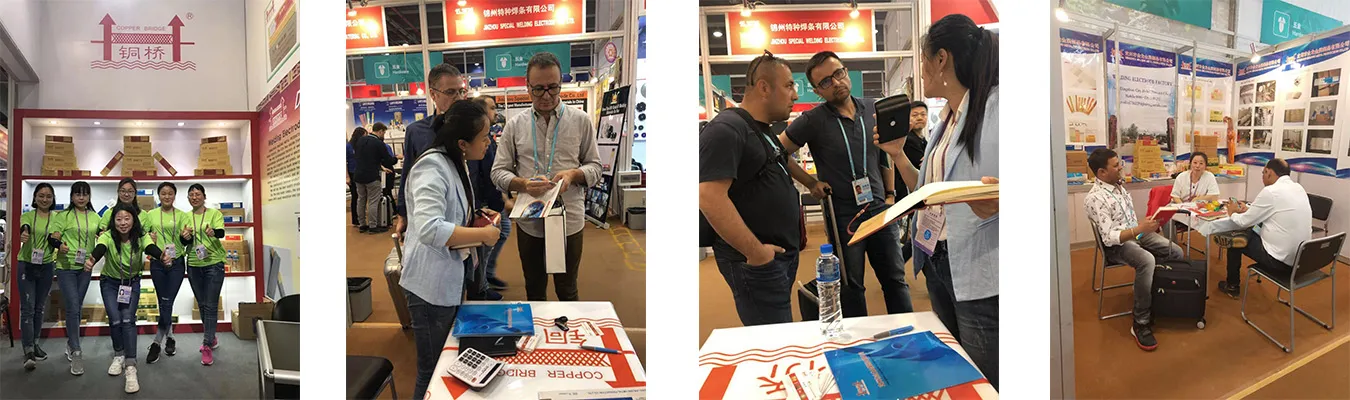
Expertise in utilizing 3/32 7018 welding rods involves understanding their optimal storage and handling to maintain their effectiveness. These rods must be kept dry to preserve their low-hydrogen characteristics; exposure to moisture can lead to porosity in the weld, undermining structural integrity. Professionals often use rod ovens or sealed packaging to ensure that the electrodes remain moisture-free until they are used. These practices highlight the importance of expertise in achieving superior weld quality and maintaining the rod's designed performance standards.
3/32 7018 welding rods
The effective use of 3/32 7018 welding rods also extends to pre-weld and post-weld procedures that ensure the weld's durability and resilience. Preheating thicker materials or those prone to cracking is a recommended practice to minimize thermal stress. Furthermore, post-weld heat treatment can be necessary to relieve residual stresses and reduce hardness in the heat-affected zones. Such meticulous attention to detail showcases the professional expertise required to maximize the benefits of these electrodes in demanding applications.
Authoritative knowledge about the 7018 rods also involves an appreciation of their safety standards and regulatory compliance. Professionals who frequently use these rods are well-versed in adhering to guidelines set by bodies such as the American Welding Society (AWS), which standardizes their classification and usage criteria. This adherence not only ensures the safety and effectiveness of welding projects but also builds trust with clients, affirming their commitment to using high-quality materials and maintaining industry standards.
In conclusion, the 3/32 7018 welding rods are indispensable to the welding industry due to their exceptional mechanical properties and versatility. Their ability to produce quality welds with low hydrogen content is essential for projects requiring high durability and resistance to cracking. The expertise required to effectively use these rods encompasses a deep understanding of their characteristics, optimal handling practices, and compliance with safety standards. Professionals who excel in these areas garner trust and respect in their field, positioning themselves as authoritative figures proficient in delivering high-quality, reliable welding solutions.