Understanding the intricacies of welding rod types is essential for any professional welder, and the 7018 electrode stands out as a staple across various industries. Known for its versatility and strength, the 7018 welding rod is highly esteemed for its unique properties and wide-ranging applications.
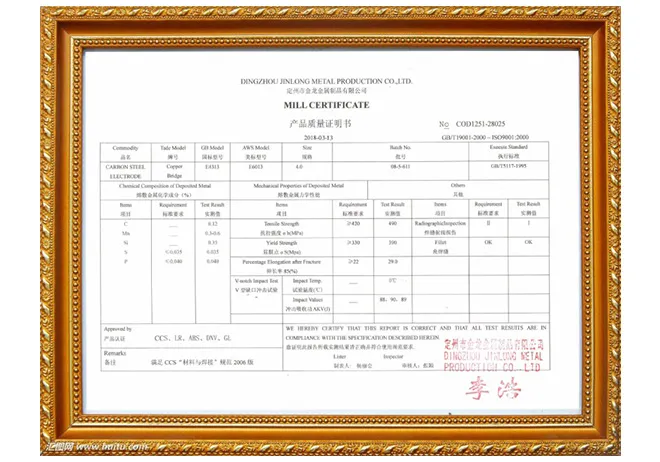
The 7018 rod is categorized under the group of low-hydrogen, iron powder electrodes. One of its primary benefits is its low moisture absorption characteristic, which makes it resistant to hydrogen-induced cracking, a prevalent issue in welding. This feature renders it particularly advantageous for welds requiring high tensile strength and ductility. Consequently, the 7018 electrode is frequently utilized in structural steel welding, pressure vessels, and pipelines where integrity and strength are paramount.
Employing the 7018 welding rod necessitates a profound understanding of its technicalities. Unlike other electrodes, the 7018 requires a more controlled welding environment, often necessitating an AC or DC+ (direct current electrode positive) power source to maintain stability and produce optimal results. Moreover, proper storage is crucial; the electrodes should be kept in a moisture-controlled environment to prevent the absorption that can lead to hydrogen embrittlement.
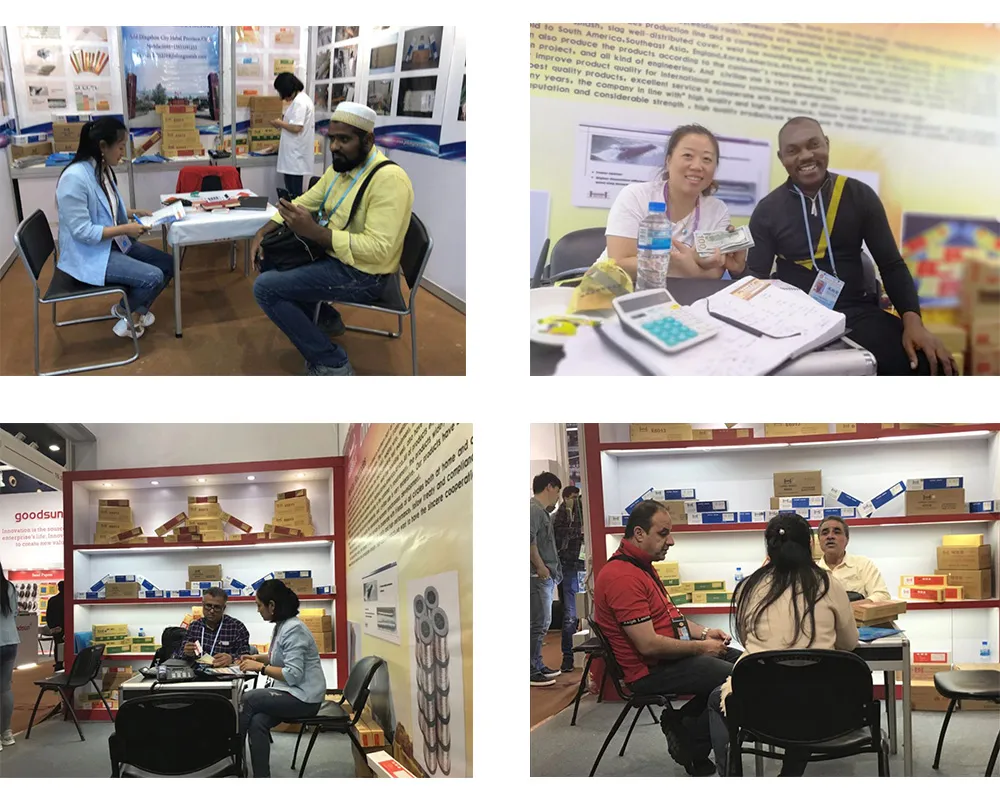
My personal experience using the 7018 rod highlights the importance of patience and precision. During a project involving a structural steel beam, the 7018 was chosen for its ability to produce a clean, strong weld. However, I learned that preheating the material was necessary to eliminate moisture, further ensuring a strong bond and reducing the risk of cracking. This preparatory step was critical, illustrating how crucial preparatory processes are when working with specific welding materials.
welding rod types 7018
Furthermore, it is crucial to hone one’s skills with vertical and overhead welding when using the 7018 rod. Its thicker slag layer and fast-freeze properties can pose a challenge, making it imperative for welders to practice proper technique and positioning to achieve ideal penetration and bead appearance. Mastery of these techniques underscores the welder’s expertise and enhances the quality of the weld.
Trustworthiness in welding performance also translates to the quality of the input materials. Opting for well-known brands that adhere to industry standards, such as AWS, guarantees the consistency and reliability of the electrodes. Professional-grade 7018 rods from reputed manufacturers undergo rigorous testing, providing assurance of their mechanical properties and performance capabilities.
Ultimately, the 7018 welding rod’s authoritative standing in the welding domain underscores its efficacy in delivering robust and reliable joints. With its impeccable performance in combating cracking and its adaptability across myriad applications, the 7018 remains a preferred choice for many welding professionals. Through diligent practice and an informed approach, welders can unlock the full potential of the 7018, ensuring superior outcomes in their projects. Understanding its nuances and optimizing its application not only stands testament to a welder’s expertise but also fortifies their reputation for delivering exceptional welding results.