Selecting the appropriate welding rod is crucial for ensuring the strength, durability, and overall quality of a welded joint.
As an experienced welder, you understand that not all welding rods are created equal. Each project demands careful consideration of material type, electrode coating, position of the weld, and expected environmental conditions. This comprehensive guide delves into the nuances of choosing the right welding rod for your specific needs, drawing from both established expertise and real-world experiences.

First and foremost, the material of the workpiece is the primary determinant in choosing a welding rod. For mild steel, the E6010 or E6011 rods are often recommended due to their all-position welding capability and penetration power. Meanwhile, if you're working with stainless steel, the E308, E309, or E316 rods provide excellent resistance to corrosion, coupled with the mechanical strength necessary for high-stress applications. For aluminum projects, an E4043 or E5356 rod is preferable, especially in overcoming aluminum's natural oxide layer which can complicate the welding process.
The choice of electrode coating plays a critical role in weld characteristics. Cellulose-based coatings, common in E6010 and E6011 rods, offer deep penetration, making them suitable for piping work or when dealing with rusty or dirty surfaces. On the other hand, low-hydrogen coatings found in rods like E7018 are prized for their ability to produce clean welds with minimal spatter and are indispensable when working under radiographic inspection standards. These low-hydrogen rods also significantly reduce the risk of hydrogen-induced cracking—a vital consideration in high-strength steel welding.
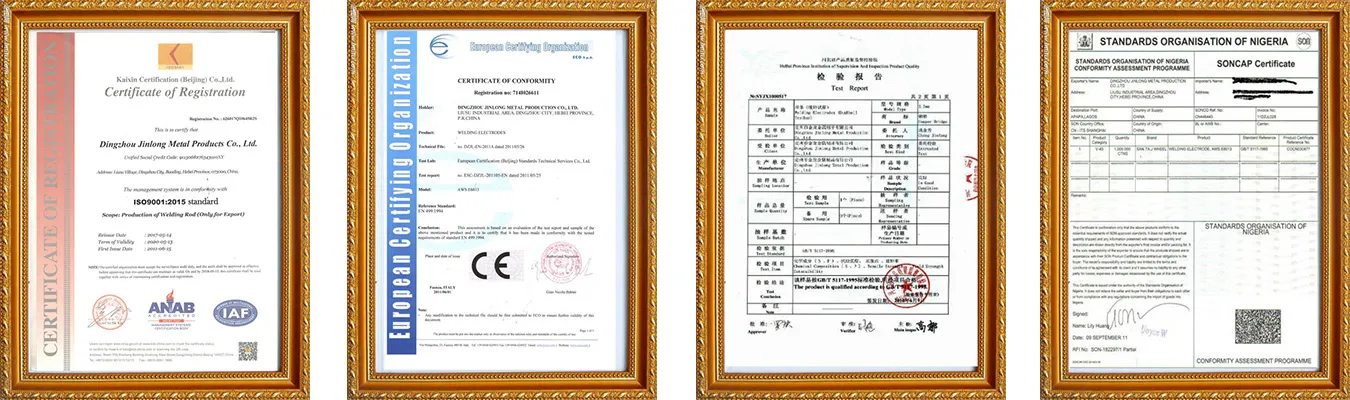
Considering the position of the weld is another pivotal factor. Certain rods perform better in particular positions. E6010 is versatile for all positions, including vertical and overhead, which can be challenging with less adaptable rods. For flat and horizontal welds where aesthetic appeal is critical, the E7014 rod can provide a smooth, beautifully contoured finish.
selecting welding rods
Real-world conditions also heavily influence rod selection. High-moisture environments necessitate using low-hydrogen rods stored at controlled humidity to prevent moisture absorption, which can lead to weld defects. Furthermore, outdoor work requiring AC generators may benefit from rods designed to maintain stable arcs despite power fluctuations, such as the dual-purpose E6011.
Many welders encounter the challenge of dissimilar metal welding, where selecting a rod like an E309 can bridge stainless steel to mild steel effectively due to its high chromium and nickel content, ensuring structural integrity across different materials.
Insight from personal experience emphasizes the benefits of maintaining an organized storage system for rods, separated by type and coating, to swiftly adapt to project specifications without compromising quality.
Ultimately, the evidence of one's expertise manifests not only in successful projects but also in the methods employed to navigate complex challenges. The authoritative selection of welding rods—grounded in knowledge and tested by experience—fortifies your reputation as a competent, reliable professional in the welding domain. As you continue refining your skill set, this adeptness in matching welding rods to the task at hand will serve as an invaluable asset, bolstering both your craftsmanship and credibility.