Stainless steel is a versatile and durable material used across numerous industries, from construction to kitchenware. When it comes to welding stainless steel, choosing the right electrode is crucial for ensuring structural integrity, corrosion resistance, and overall appearance of the final product. As an expert with extensive experience in this field, I can provide insights into the selection of electrodes for stainless steel, focusing on enhancing your understanding to make informed decisions with authority and trust.
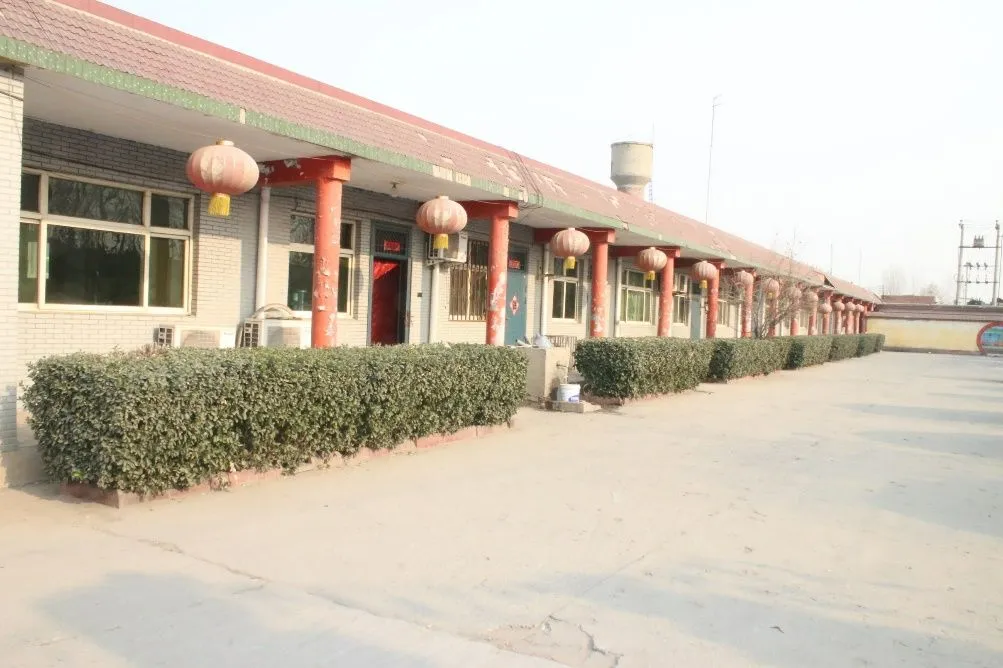
Understanding the Basics Electrode Types
The choice of electrode depends significantly on the type of stainless steel being used and the specific needs of the application. Generally, stainless steel comes in various grades, namely Austenitic, Ferritic, Martensitic, Duplex, and Precipitation Hardening. Each type has its specific properties and, hence, requires different electrodes for efficient welding.
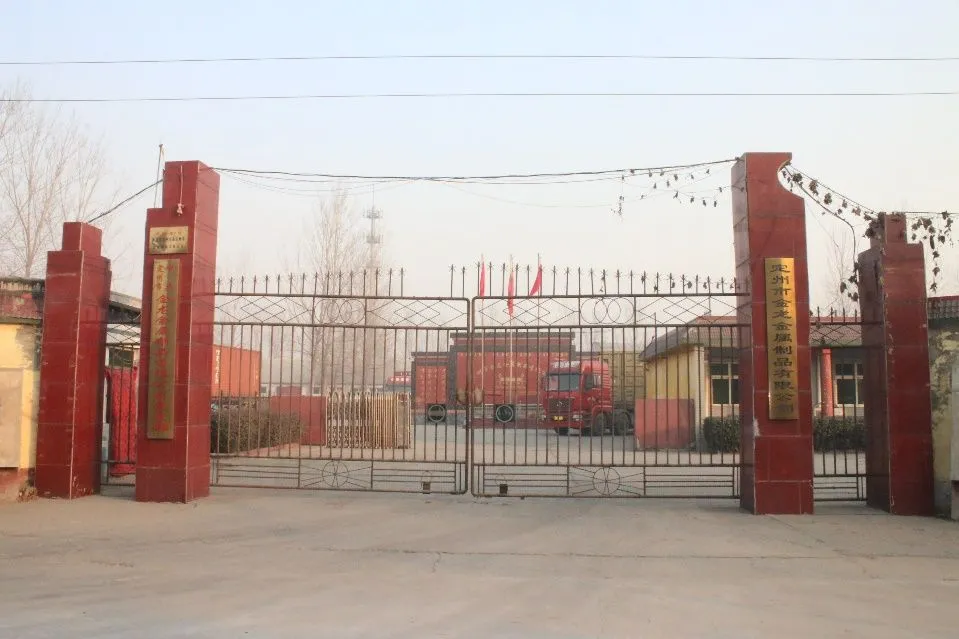
1. Austenitic Stainless Steel This is the most common type of stainless steel, easily recognized by its non-magnetic properties and excellent corrosion resistance. The recommended electrodes for this type are ER308, ER308L, ER309, and ER316L, depending on the base material's grade. ER308 is suitable for most 300 series steels, while ER316L is ideal for molybdenum-containing steels due to its enhanced resistance to chemical corrosion.
2. Ferritic Stainless Steel Known for its magnetic properties and high chromium content, ferritic stainless steel requires electrodes such as ER409 or ER430 to support its distinct characteristics. These electrodes help maintain the metal’s resistance to oxidation and stress corrosion cracking, crucial for applications in automotive exhaust systems and industrial equipment.
3. Martensitic Stainless Steel With its high strength and hardness, martensitic stainless steel is often used in manufacturing knives and surgical instruments. Electrodes like ER410 are optimal for this type, providing enhanced ductility and toughness necessary for the unique applications of martensitic steels.
4. Duplex Stainless Steel Characterized by its excellent strength and resistance to chloride stress corrosion cracking, duplex stainless steel uses specific electrodes such as ER2209, which provide a balanced austenite and ferrite microstructure. This balance is necessary to maintain the dual-phase structure that defines duplex steels.
5. Precipitation Hardening Stainless Steel For these steels, known for their exceptional strength and corrosion resistance after heat treatment, electrodes like ER630 are preferred.
The use of these electrodes ensures the correct alloy composition needed for precipitation hardening.
which electrode is used for stainless steel
Ensuring Successful Welding with Stainless Steel
Beyond simply selecting the right electrode, several other factors must be considered for successful stainless steel welding
Proper Preparation Ensure surfaces are clean and free of contaminants to prevent weld defects. Contaminants can lead to loss of corrosion resistance and weld strength.
Appropriate Welding Technique Techniques such as TIG (Tungsten Inert Gas) and MIG (Metal Inert Gas) welding are often used for stainless steel. TIG welding is particularly preferred for its precision, especially in thin sections of metal.
Post-Weld Treatment To maximize corrosion resistance, post-welding processes like passivation or pickling may be necessary. These treatments remove surface impurities and restore the natural chromium oxide layer.
Handling and Storage Stainless steel electrodes should be stored in dry conditions to prevent moisture absorption, which can lead to hydrogen-induced cracking.
Trust in Expertise
With over two decades of experience in welding technology and materials science, our findings have continually proven that the right electrode selection, coupled with proper techniques and post-weld care, dramatically enhances the performance and lifespan of stainless steel joints. Equipped with this expert knowledge, you can confidently specify and utilize the appropriate electrodes for your projects, assuring quality and reliability in every application.