Choosing the right welding rod for joining stainless steel to carbon steel is pivotal for ensuring structural integrity and achieving optimal weld quality. This task, although seemingly straightforward, involves understanding material properties, compatibility, and application requirements. Here, we delve into the process of selecting appropriate welding rods, touching on key factors such as material compatibility, mechanical properties, and operational conditions.
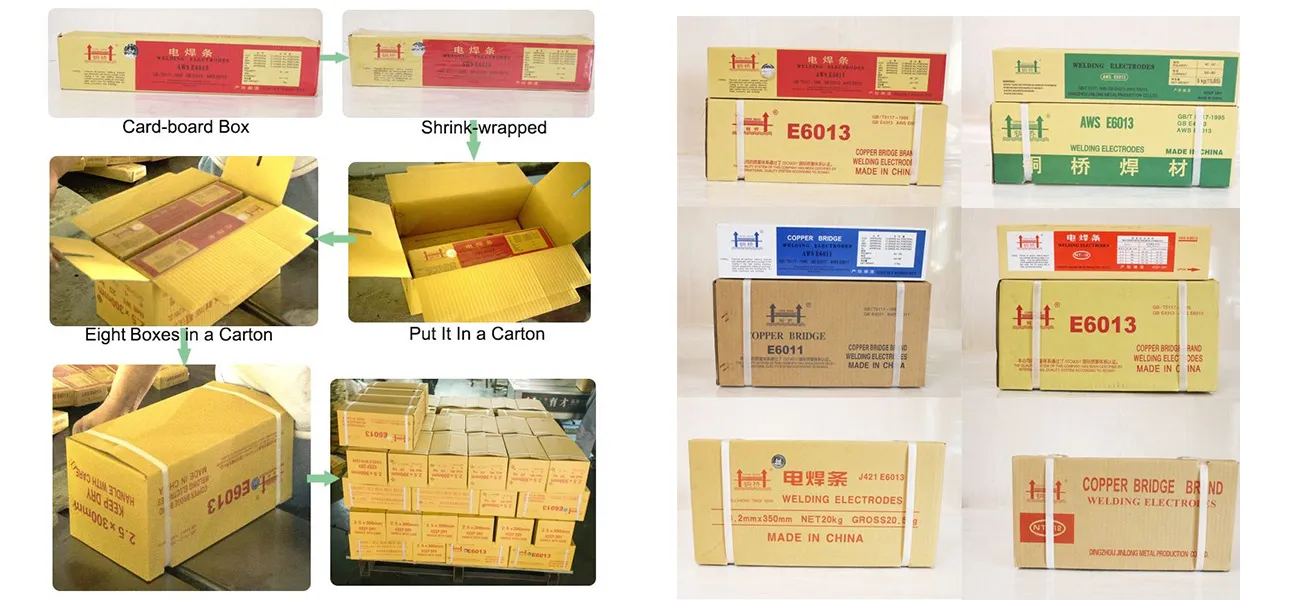
One of the primary considerations is the chemical composition of the materials being bonded. Stainless steel is known for its corrosion resistance, which is due to chromium content, generally above 10.5%. Carbon steel, on the other hand, contains a higher level of carbon, making it stronger but less ductile and more susceptible to corrosion. Therefore, when selecting a welding rod, the goal is to obtain a filler metal that can bridge these differences.
A commonly recommended welding rod for this purpose is ER309L, an austenitic stainless steel filler rod that provides a good balance between strength and corrosion resistance. This specific rod contains a higher level of chromium and nickel, making it ideal for dissimilar metal welding. The presence of nickel in the rod is crucial as it stabilizes the austenitic microstructure, ensuring a ductile weld that can withstand thermal expansion and contraction.
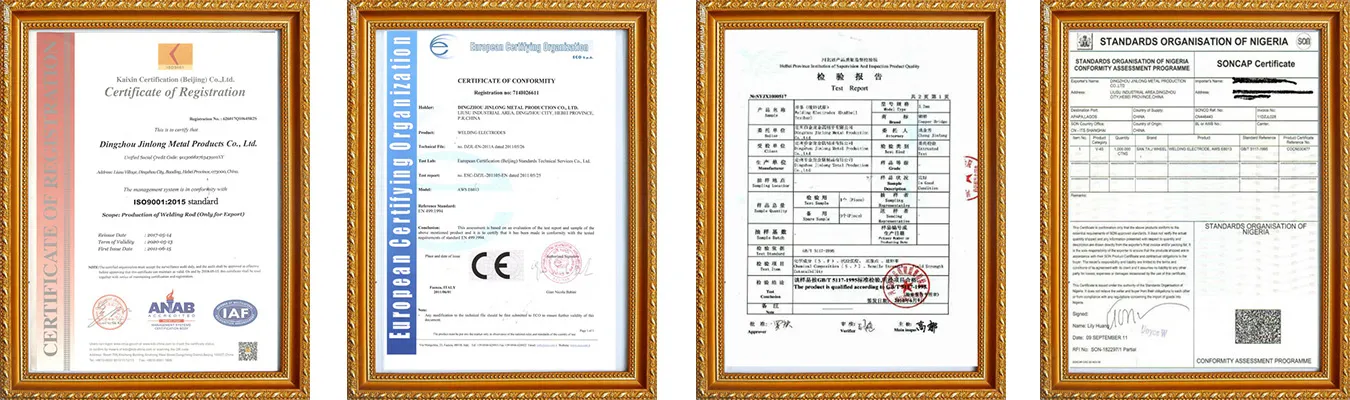
In scenarios where the structural integrity and elevated temperature service are of utmost importance, ER312 rods are often preferred. ER312 contains a higher percentage of chromium and is particularly useful in harsh industrial environments where both strength and corrosion resistance are mandatory. The use of ER312 also minimizes the risk of hot cracking, a common challenge when welding these differing steel types.
Having made a choice of rod, pre-weld procedures should not be overlooked. A thorough cleaning of both base metals is essential to eliminate contaminants that could compromise the weld. Preheating might be necessary to prevent thermal shock, particularly when dealing with a high carbon steel base that can be prone to cracking.
Maintaining precise control over the interpass temperature is also crucial.
During the welding process, a technique that mitigates dilution is key. Excessive dilution from the base metals can lead to a weld pool that reflects their unfavorable properties such as brittleness or reduced corrosion resistance. Thus, controlling the arc length and travel speed is vital to ensure that the properties of the filler metal predominate in the weld.
what welding rod to use for stainless to carbon
Post-weld treatments like heat treatment can further enhance the mechanical properties of the weld joint. It is often recommended to follow the welding procedure with stress-relieving processes to reduce residual stresses that could otherwise lead to cracking.
What about the environments and applications where these welds are used? The joining of stainless steel to carbon steel is prevalent in industries such as petrochemical, food processing, and construction. These applications often involve aggressive media exposure or need for reliable high-temperature performance. Therefore, the selection of a welding rod goes beyond just technical specifications; it also involves understanding operational demands and environmental conditions.
Quality control is paramount throughout this entire process. Employ radiographic or ultrasonic testing to ensure weld integrity, particularly in critical applications. Document the welding procedure specifications (WPS) to maintain consistency and reproduce success in future projects.
Lastly, keeping abreast with advancements in filler metal technology can provide new rod options that may offer improved performance for specific scenarios. Engaging with manufacturers and suppliers who have technical expertise can also guide you to select the best welding rod fit for particular tasks and conditions.
Making an informed choice of welding rod for stainless to carbon steel not only assures a robust weld but also enhances the longevity and reliability of the final product. Each step, from rod selection and pre-weld preparation to post-weld treatment, is integral in creating a weld that meets industrial standards and withstands the test of time.