When selecting the appropriate welding electrode for a project,
it is crucial to understand the differences between types like E6013 and E7018. Both rods are popular in the welding industry, yet their applications, characteristics, and performance differ significantly.
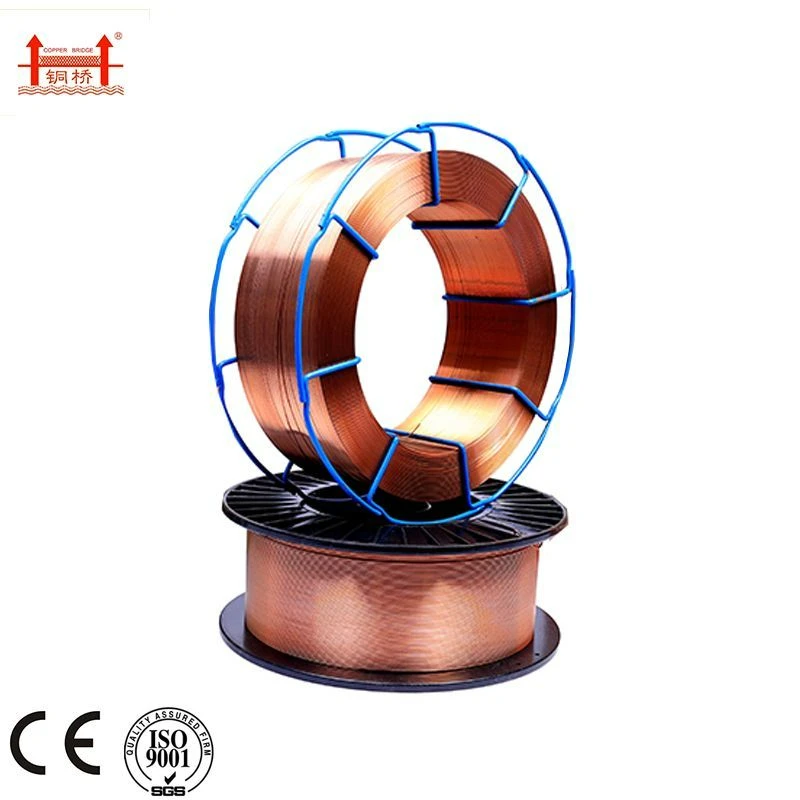
E6013 electrodes are often favored for their versatility and ease of use. They produce a smooth, stable arc and are known for excellent bead appearance, which is aesthetically pleasing. These electrodes are particularly suitable for sheet metal work, general fabrication, and maintenance tasks. Their ability to work well on both AC and DC currents and in all positions makes them a practical choice for a wide range of applications. The flux composition of E6013 results in a rapid freezing slag, allowing for fast travel speeds which translates to increased productivity in certain scenarios. However, it's important to note that E6013 rods are not ideal for structural work that demands high-strength welds due to their moderate tensile strength of around 60,000 psi.
In contrast, E7018 electrodes are renowned for their high deposition rate and the superior strength of the welds they produce, making them a staple in the construction industry, especially for structural welding. With a tensile strength of 70,000 psi, E7018 rods are designed for tougher, more demanding jobs where weld integrity is critical. They are primarily used with DCEP (DC Electrode Positive) and require a stable power source to maintain a consistent arc. The low-hydrogen characteristics of E7018 electrodes mean they have less susceptibility to cracking and porosity, offering greater resistance to atmospheric moisture. However, these rods require careful storage in a dry environment to prevent moisture absorption, which could lead to hydrogen-induced cracking.
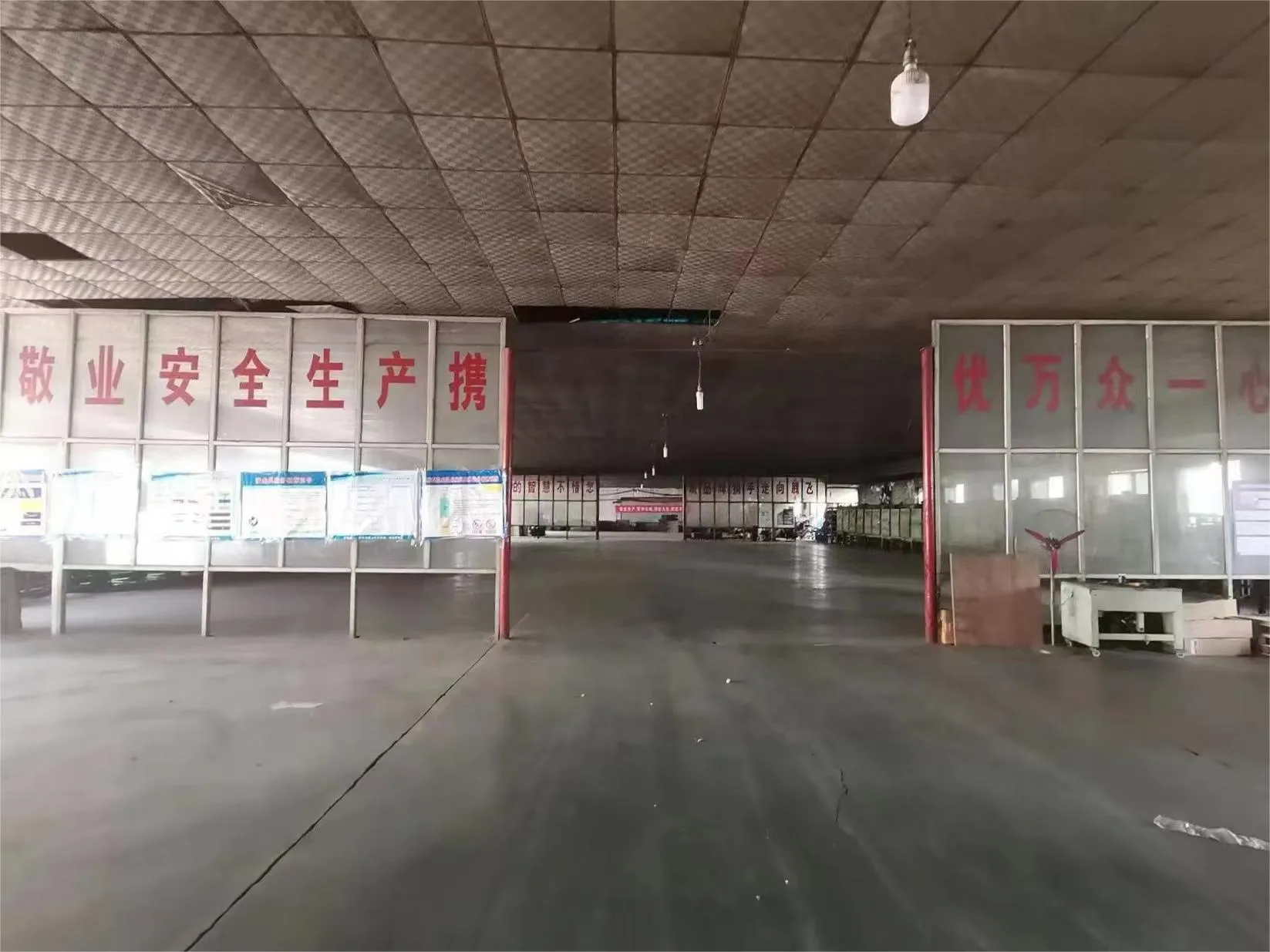
what is the difference between e6013 and e7018
From a practical perspective, a welder working with E6013 rods will appreciate the ease with which slag can be removed and the electrode's forgiving nature that adapts well to variations in operator technique. The E6013 electrode is often a preferred choice for home hobbyists and light-duty fabrication because it does not demand specialized welding equipment and skills.
Meanwhile, an experienced welder using E7018 rods might emphasize the electrode's robust performance in creating durable, high-quality welds suitable for critical infrastructure projects like bridges, buildings, and pipelines. These rods require a higher level of skill and sometimes preheating of the workpiece, but the trade-off is a strong, reliable weld.
In conclusion, choosing between E6013 and E7018 electrodes depends chiefly on the specific requirements and conditions of the welding task at hand. For projects focusing on ease of use, aesthetic finish, or involving thinner materials, E6013 is often the electrode of choice. On the other hand, E7018 is indispensable for projects where the strength and reliability of the weld are non-negotiable. Understanding these nuances ensures welders select the right tool for their job, enhancing both the quality and efficiency of their work. Trusting in the proven performance of these electrodes, backed by professional experience and industry standards, welders can achieve excellent results tailored to their specific project needs.