Understanding the intricate choices involved in stainless steel welding is paramount for both professionals and hobbyists. Stainless steel, known for its resistance to corrosion, strength, and aesthetic appeal, is a staple in industries ranging from construction to automotive and even culinary equipment. However, to effectively work with stainless steel, one must choose the correct electrode, which can be the linchpin between a successful project and a failed one. This guidance delves into the essentials of selecting the right electrode for stainless steel, drawing from expert knowledge and real-world experiences to enhance your understanding.
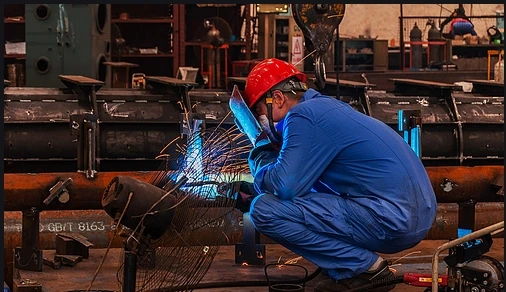
Stainless steel welding demands precision and the correct tools, with the electrode serving as a critical component. It acts as a conduit, transferring the welding current from the welding machine to the metal surfaces being joined. The choice of electrode is influenced by several factors including the type of stainless steel being welded, the welding technique employed, and the desired properties of the welded joint.
There are three principal types of stainless steel electrodes coated electrodes, bare electrodes, and flux-cored electrodes. Coated electrodes are typically used in shielded metal arc welding (SMAW) and offer protection against oxidation, aiding in the production of a clean, strong weld. Bare electrodes, often used in gas tungsten arc welding (GTAW) or tungsten inert gas welding (TIG), provide higher precision and control, making them suitable for thinner materials. Flux-cored electrodes, used in flux-cored arc welding (FCAW), offer versatility and can save time due to their high deposition rate.
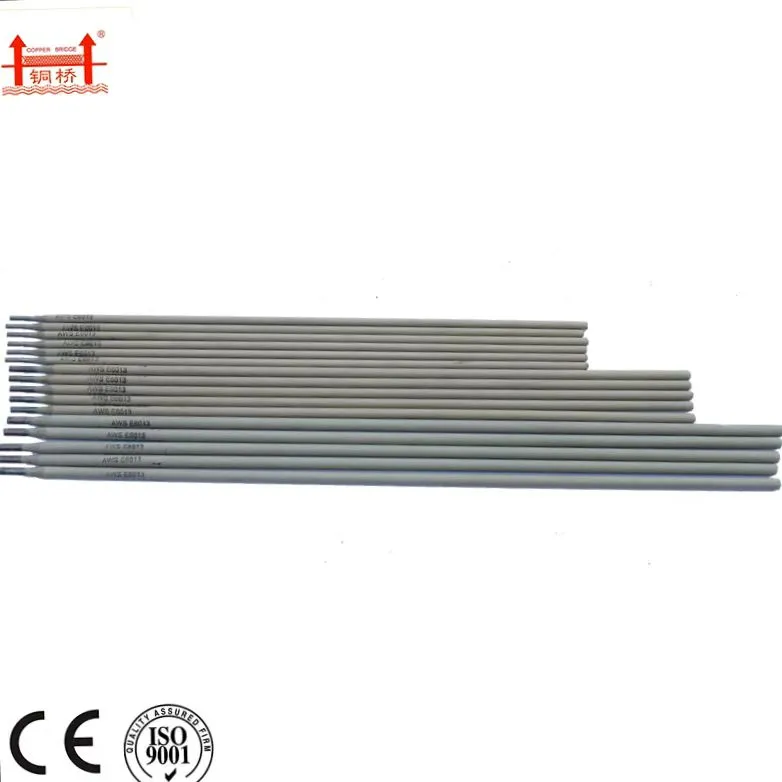
When choosing an electrode,
it is crucial to consider the type of stainless steel. The three main families include austenitic, ferritic, and martensitic. Each type has specific electrodes that are compatible with their chemical composition, ensuring integrity and performance of the weld. For instance, austenitic steels, which are the most common due to their excellent mechanical properties and corrosion resistance, often utilize 308, 309, or 316 electrodes. The choice among these is dictated by the base material and the environmental conditions the welded part will endure.
The welding position, whether flat, horizontal, vertical or overhead, also influences electrode selection. Some electrodes, like those used in SMAW, are versatile and can be used in all positions, while others may be limited to a few. This adaptability makes them invaluable for repair work or applications requiring complex joint configurations.
what electrode to use for stainless steel
One common pitfall is not accounting for the potential for carbide precipitation and resulting corrosion when welding stainless steels, especially with austenitic grades. Low carbon variants, denoted by an L such as 308L or 316L, are recommended to minimize this risk. These low carbon electrodes are particularly beneficial when the weldment will be exposed to high temperatures or corrosive environments over time.
Safety and reliability are underpinning concerns when working with stainless steel. Electrodes' performance can significantly influence the strength and durability of a weld. Therefore, ensuring the electrode's compatibility with both the base material and the welding process is essential. It is also vital to align with industry standards and manufacturer recommendations to uphold safety and quality.
Real-life welding challenges often reveal the expertise needed to choose the right electrode. For instance, welding in automotive contexts requires electrodes that not only provide robust and corrosion-resistant joints but also retain aesthetic beauty. Similarly, in the food and beverage industry, the highest hygiene standards must be met, requiring electrodes that support sanitary welding techniques.
In practice, the understanding of how electrode types interact with different stainless steels is often honed through years of experience and trial. Professionals recommend starting with small-scale tests, welding sample pieces to assess outcomes before proceeding with larger projects. This hands-on experience supports informed electrode selection and process adjustment, ensuring project success and efficiency.
Navigating electrode options for stainless steel welding involves a balance of scientific understanding and practical expertise. It requires clear insight into materials, processes, and expected outcomes. Armed with this knowledge, you can make informed decisions, resulting in high-quality welds that meet both functional and aesthetic needs, reinforcing your reputation for excellence in stainless steel welding projects.