Selecting the right electrode for welding stainless steel is crucial not only for the integrity of the weld but also for the longevity and performance of the welded structures. As the engineering and manufacturing sectors continue to evolve, understanding the nuances of stainless steel welding becomes imperative for professionals involved in the process.
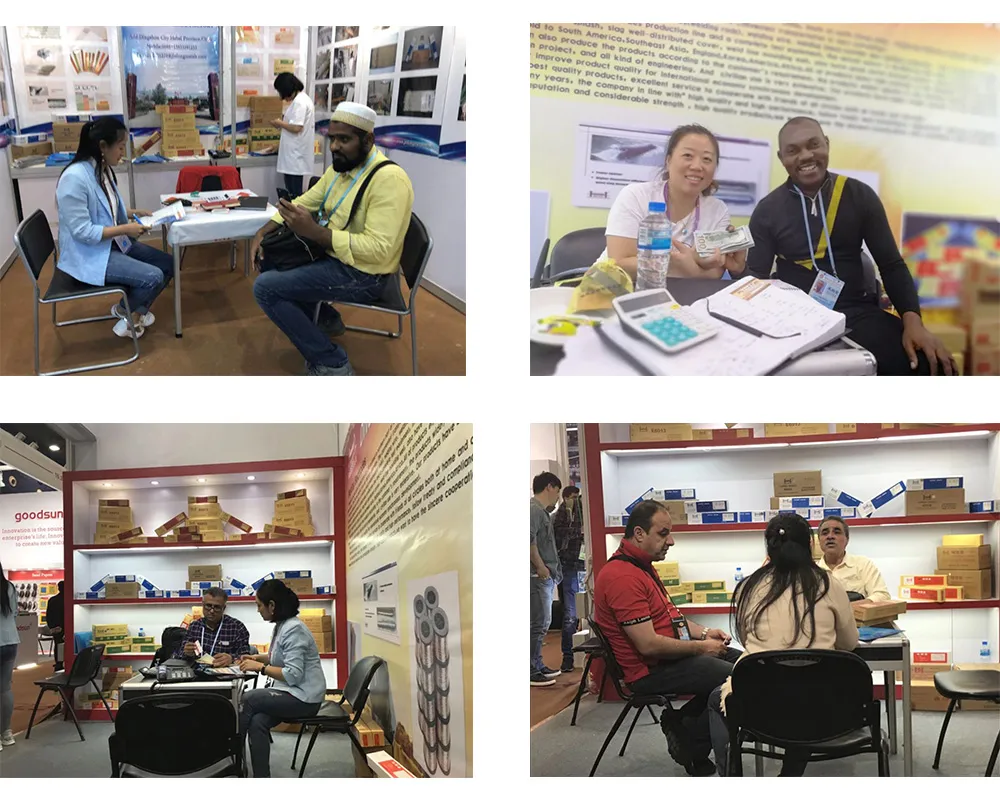
When it comes to welding stainless steel, it's essential to comprehend the types and requirements of electrodes that work with this versatile material. Stainless steel is renowned for its corrosion resistance, aesthetic appeal, and durability, making it a preferred choice in industries such as automotive, aerospace, food and beverage, and chemical processing.
Experience Tackling the Challenges
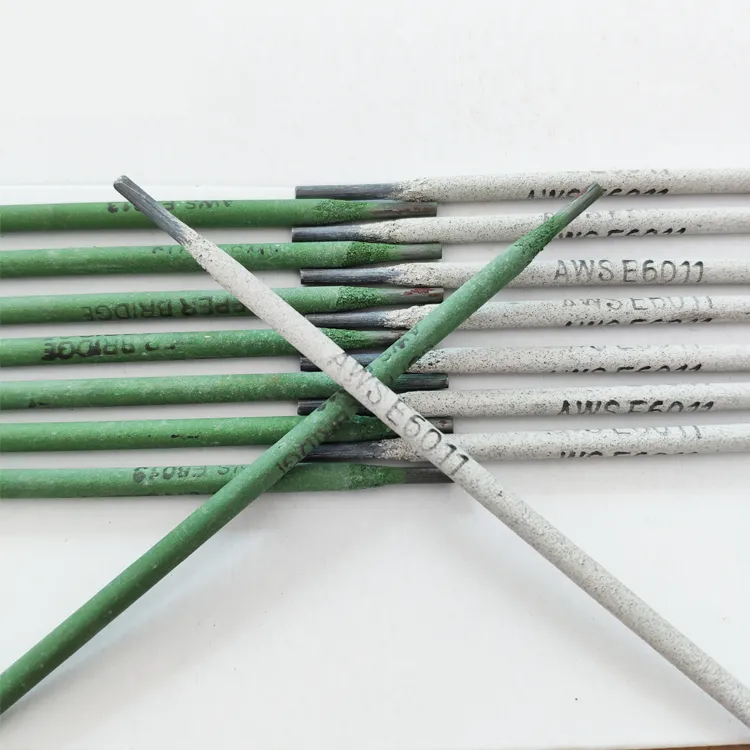
From years of industry experience, experts have noted that choosing the correct electrode affects not just the visual appearance of the weld but also its mechanical properties. For instance, stainless steel contains chromium, which provides its corrosion resistance. During welding, maintaining the chromium content in the weld metal is paramount, as depletion can lead to rust formation.
A commonly used electrode for stainless steel is the E308L-16. This electrode is ideal for welding 304 stainless steel, among other similar grades, due to its low carbon content that minimizes carbide precipitation during the welding process, thus preserving the metal's corrosion resistance characteristics.
Expertise Choosing the Right Electrode
For those possessing expertise in stainless steel welding, E309 electrodes are preferred when welding dissimilar metals such as the joining of stainless steel to mild or carbon steel. The higher alloy content in E309 provides a safety cushion against cracking and promotes a stable arc during the welding process.
When welding high-strength stainless steel, professionals might choose the E316L electrode. This electrode is particularly noted for its molybdenum content, which enhances resistance to pitting corrosion and increases performance in environments exposed to chlorides and other harsh chemicals. This makes it a go-to choice for the marine and coastal construction industries.
what electrode is used for stainless steel
Authoritativeness Trust the Process
Depending on the application, authoritative sources recommend pre-weld preparations wherever applicable. This may include cleaning the metal surfaces to remove any grease, oil, or dust that could compromise the weld or using specific welding techniques such as TIG welding for thinner stainless sections that require precision and a clean finish.
Stainless steel can be sensitive to thermal expansion. Therefore, understanding the thermal properties of the stainless steel in question and using controlled heat input during welding is essential to prevent warping and maintain structural integrity.
Trustworthiness Safety and Quality Control
Safety and quality in stainless steel welding cannot be overstated. It is crucial to use protective gear to prevent exposure to harmful fumes and ultraviolet light. Additionally, post-weld inspections including non-destructive testing methodologies like ultrasonic testing can detect potential faults or weaknesses in the weld, thereby ensuring that the welding process adheres to stringent quality standards.
Moreover, ensuring that the workshop maintains consistent environmental controls such as humidity and temperature can help in producing a reliable and defect-free welded product. High humidity levels, for example, can lead to moisture pick-up, influencing the performance of certain electrodes.
In conclusion, the selection of electrodes for stainless steel welding is not a decision to be taken lightly. It requires an understanding of material composition, application-specific requirements, and an awareness of how different factors can impact the quality of the weld. Through informed decisions based on experience, expertise, authority, and trustworthiness, fabricators and engineers are better equipped to deliver superior welding results tailored to their specific project needs.