Understanding the meaning behind the numbers and letters on a welding rod can significantly enhance the quality of your welding projects. For budding welders or those looking to refine their skills,
the cryptic 7018 stamped on a welding rod may appear perplexing at first glance. However, unraveling the meaning of these digits can unlock a deeper comprehension of your materials and optimize your work.
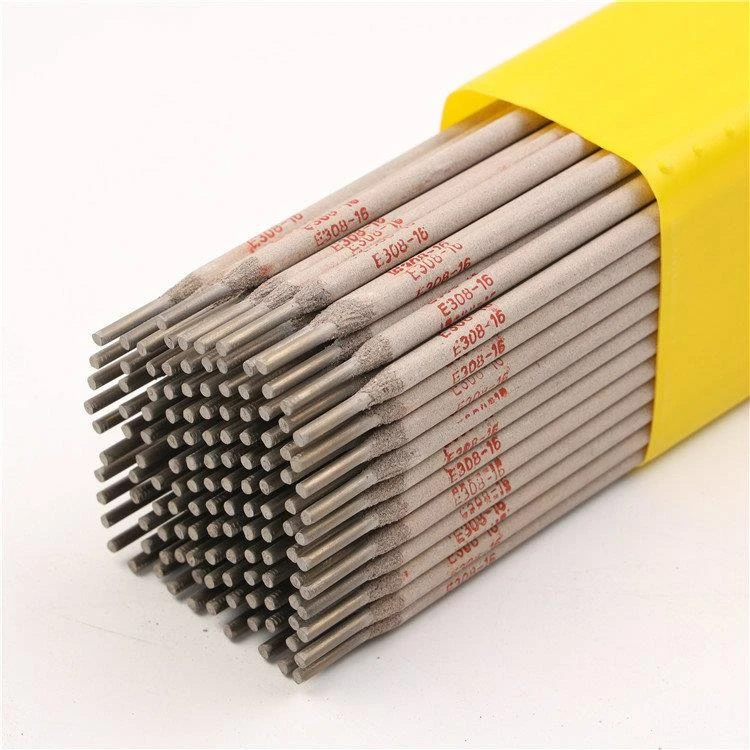
The 7018 designation follows a standard classification system developed by the American Welding Society (AWS) to categorize electrodes. Each digit provides specific information about the characteristics and intended use of the electrode. Starting with the 70, this figure represents the tensile strength of the weld deposit. Measured in thousands of pounds per square inch (PSI), a 70 signifies that the weld can withstand a tensile stress of 70,000 PSI. Understanding this strength capacity is crucial in ensuring that the welded materials will not fail under expected loads or pressures, making it indispensable for high-stress applications such as construction, shipbuilding, or pipeline installation.
The third digit, 1, indicates the position in which the electrode can be used. A designation of 1 suggests that the 7018 electrode is versatile and can be employed in all positions—flat, horizontal, vertical, and overhead. This versatility makes the 7018 electrode a favorite among welders who require adaptability across various job site conditions.
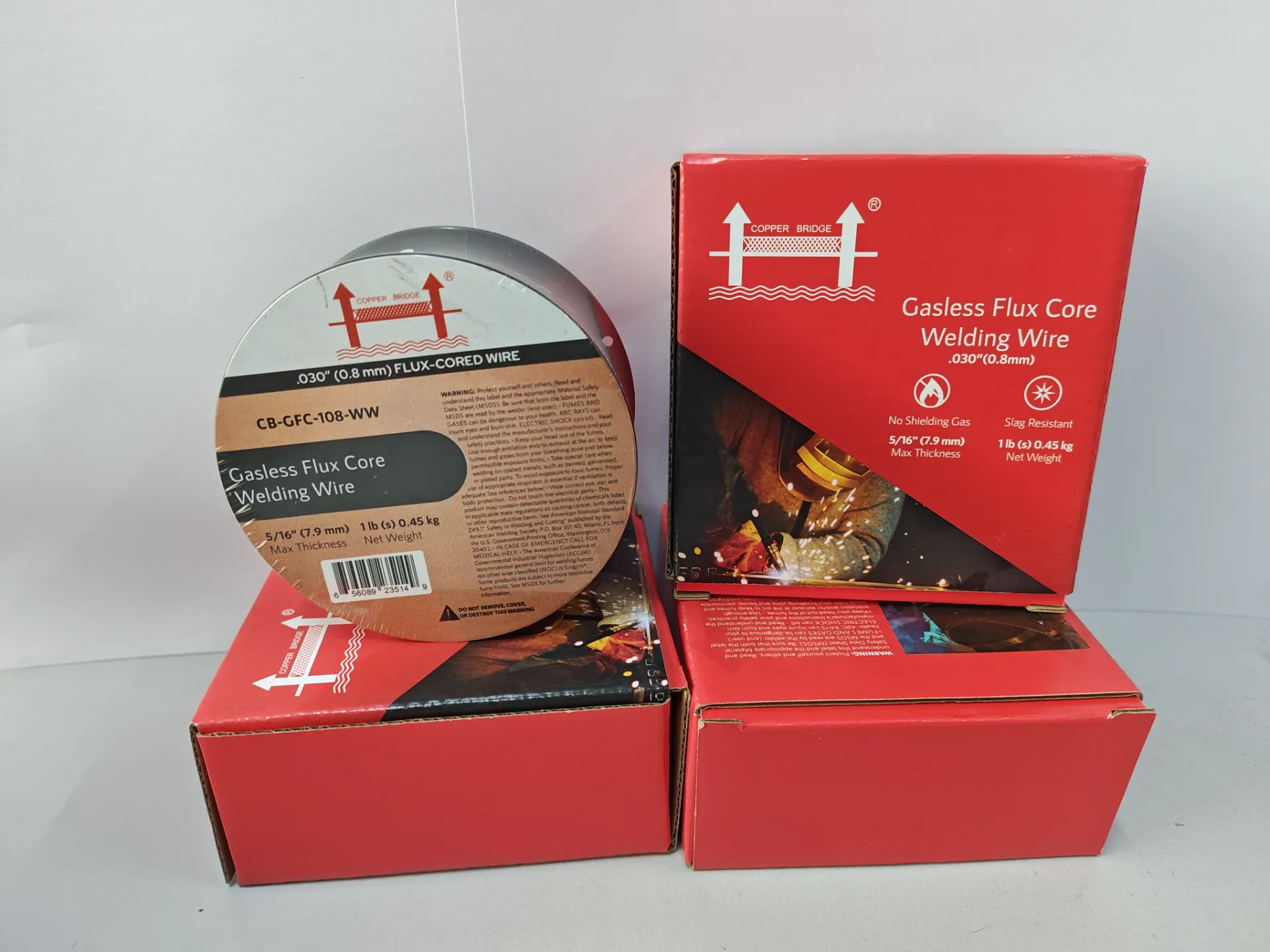
The final digit, in this case, 8, provides insight into the type of flux coating and current that can be used with the electrode. The 8 signifies a low hydrogen, iron powder coating that reduces the risk of hydrogen-induced cracking—a common challenge in welding operations. This coating facilitates smoother operation by minimizing spatter and allows for a more stable arc, which is crucial for achieving consistent bead quality. The use of iron powder also increases deposition rates, making the 7018 electrode highly efficient for larger projects.
Welders often appreciate the low hydrogen composition of the 7018 electrode, as it prevents moisture absorption that could lead to hydrogen embrittlement. Proper storage and handling of 7018 electrodes are crucial in maintaining their low hydrogen characteristics. This involves keeping the rods in a dry, temperature-controlled environment, often requiring the use of an electrode oven to prevent moisture pickup.
what does the 7018 on a welding rod mean
Practically, the 7018 electrode is lauded for its ease of use and the superior finish it provides. Its ability to produce strong, durable welds with a fine aesthetic quality makes it ideal for critical joints where the appearance of the weld plays as important a role as its strength. Welders engaged in structural projects frequently choose 7018 for its seamless finish and dependable performance.
Experienced welders underscore the importance of maintaining proper technique when using 7018 rods. Keeping a consistent angle, speed, and travel distance is paramount to control the heat input and avoid weld defects such as porosity or slag inclusions. As many experts suggest, practicing on scrap materials before progressing to the actual project can prevent costly errors and build confidence in using these electrodes.
Authoritative bodies such as the AWS emphasize adherence to safety protocols when working with 7018 electrodes. This includes wearing appropriate personal protective equipment (PPE), using adequate ventilation to avoid exposure to harmful fumes, and ensuring that electrical connections are secure to prevent accidents.
In conclusion, the 7018 welding rod is an embodiment of reliability and performance in the welding industry. Its detailed classification provides essential information that empowers welders to make informed decisions tailored to their project's specific demands. By embracing the strengths of the 7018 electrode, welding professionals can achieve high-quality results characterized by exceptional strength, aesthetic finish, and versatility across a range of applications.