In the world of welding, the significance of choosing the right electrode cannot be overstated. One such electrode, the 7018 rod, stands out due to its unique characteristics and versatile applications. Understanding what the 7018 rod means involves delving into its composition, usability, and the implications it holds for welding projects across various industries.
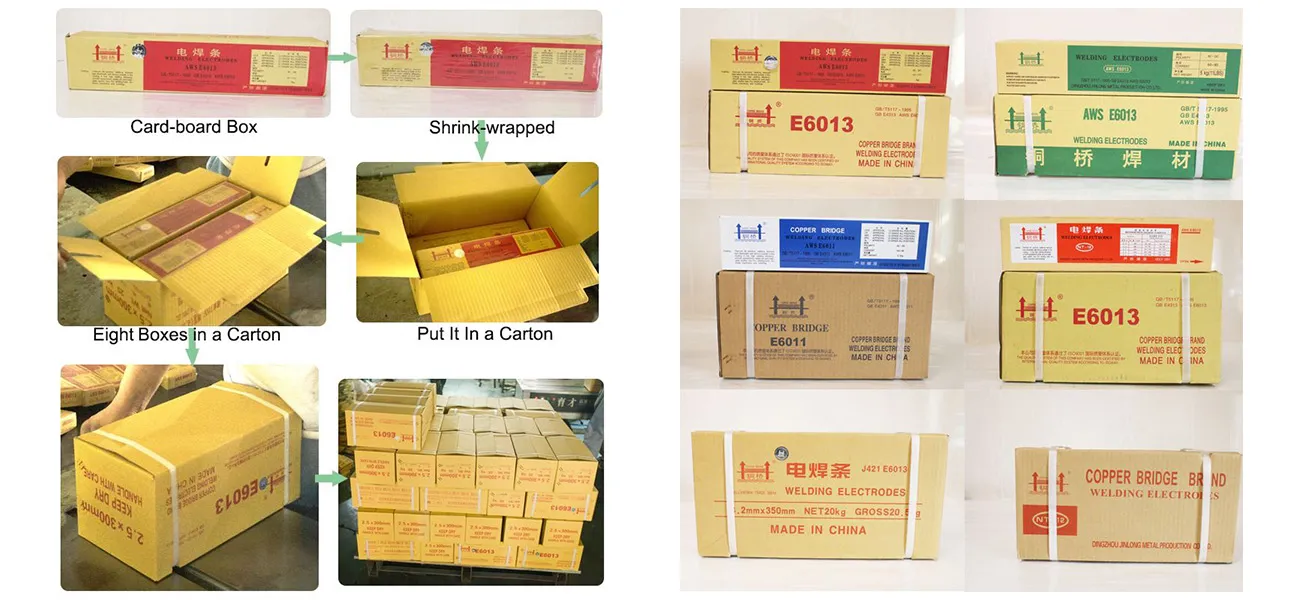
The 7018 rod is a low-hydrogen, potassium-bearing, iron powder-coated electrode widely used in structural welding. The numerical designation '7018' provides a clear insight into its capabilities. The '70' in 7018 signifies the tensile strength of the weld deposit, which is 70,000 psi. This feature is crucial for applications where strong joints are required to withstand high stress. The '1' denotes the position in which the rod can be used. It is suitable for all positions, whether flat, horizontal, vertical, or overhead. This versatility ensures that welders can tackle complex projects with varying joint configurations without switching to different rods. The '8' indicates the coating type and the current the electrode can handle. In this case, it can operate with either AC or DC current, adding to its usability.
The low-hydrogen nature of the 7018 rod is particularly significant because it reduces the risk of hydrogen-induced cracking, a common issue in welding that can jeopardize the integrity of a joint. This makes the 7018 rod an ideal choice for welding high-strength steels and critical structural components. Its iron powder coating enhances deposition efficiency and weld bead appearance, contributing to a cleaner and more aesthetically pleasing weld.
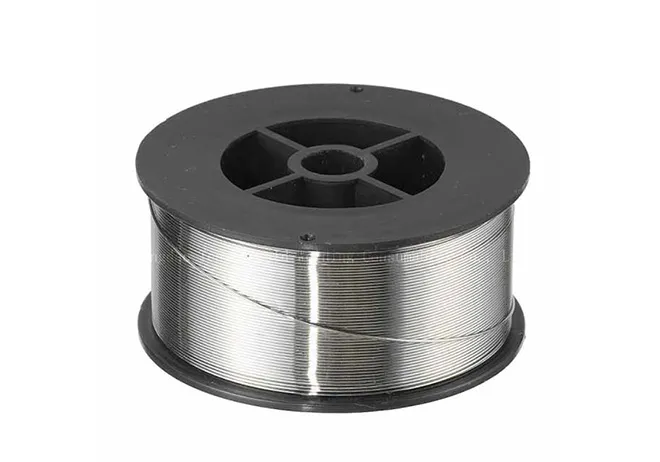
Professionals in the field appreciate the 7018 rod for its reliability and consistent performance. Its ability to produce smooth weld beads with minimal spatter reduces the need for extensive post-weld cleanup, thereby enhancing productivity. This attribute is crucial for large-scale projects where time and resources are of the essence. With the 7018 rod, welders can achieve high-quality welds with excellent mechanical properties, ensuring the durability and safety of structures such as bridges, buildings, and heavy machinery.
what does 7018 rod mean
For optimal results,
the 7018 rod must be stored and handled properly. Since it is susceptible to moisture absorption, storing it in a dry area or using an oven to maintain its temperature is recommended. This precaution prevents moisture-related defects that could compromise the weld. Furthermore, preheating the base material can enhance the rod's performance, particularly in thicker materials or alloys prone to cracking.
Leading manufacturers of welding equipment and supplies, such as Lincoln Electric and ESAB, advocate the use of 7018 rods in various applications, from shipbuilding to the construction of pressure vessels and industrial boilers. Their endorsement underscores the rod's authority in the welding community, cementing its status as an indispensable tool for achieving superior weld quality.
The trustworthiness of the 7018 rod is supported by its widespread adoption across industries with stringent standards for strength and safety. Whether used in demanding conditions or routine fabrication environments, welders consistently rely on its predictable performance. This trust is further reinforced by professional certifications, with many welders trained specifically in techniques to maximize the benefits of using this electrode.
In conclusion, the 7018 rod's reputation as a dependable welding electrode stems from its impressive tensile strength, all-position usability, low-hydrogen benefits, and compatibility with various current types. For welders seeking a rod that combines expertise, authority, and trust with practical experience, the 7018 is a go-to choice. Its role in high-stakes projects across numerous fields attests to its unparalleled efficacy and enduring value in the world of welding.