In the world of welding, the term 7018 refers to a specific type of electrode that is widely recognized and utilized within the industry for its reliability and versatility. This electrode is a choice material for professionals who seek precision and durability in their welding projects. Understanding what 7018 means can significantly enhance the quality and efficiency of welding work, and can guide experts in best practices for material fusion.
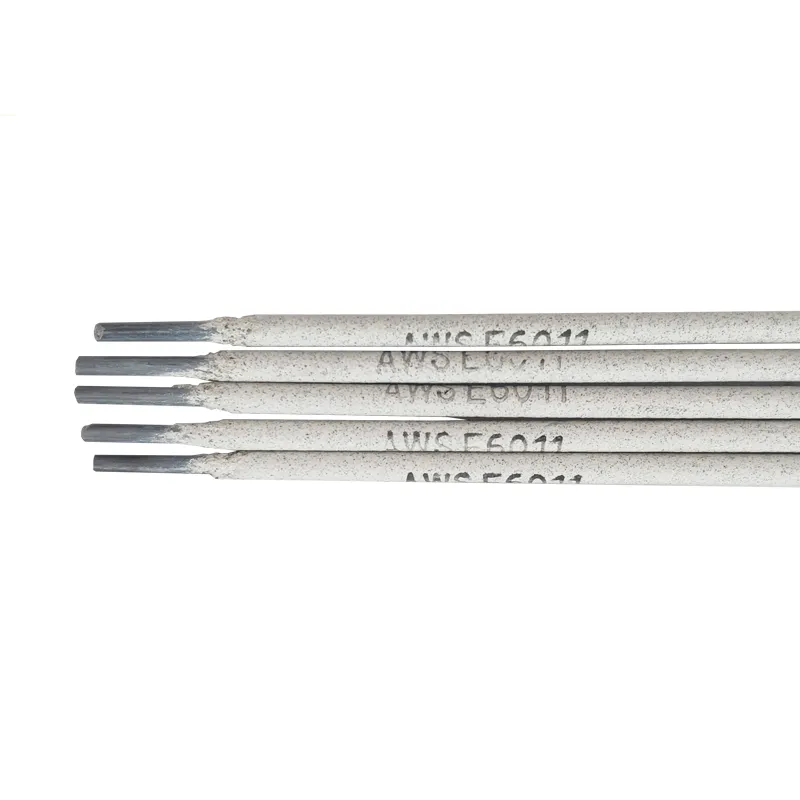
7018 is an alphanumeric code used in the American Welding Society (AWS) classification system that provides critical information about the electrode's properties. The first two digits, 70, indicate the minimum tensile strength of the weld deposit, which is 70,000 psi (pounds per square inch). This high tensile strength is ideal for structural steel projects, ensuring a robust and sturdy bond once the materials are welded together.
The third digit, 1, signifies the electrode's suitability for all-position welding, meaning it can be used vertically, horizontally, overhead, and flat. This flexibility affords welders the convenience of executing complex welds on-site without the need to reposition the workpiece. This becomes invaluable in projects involving intricate steel frameworks or large construction structures where repositioning materials is not feasible.
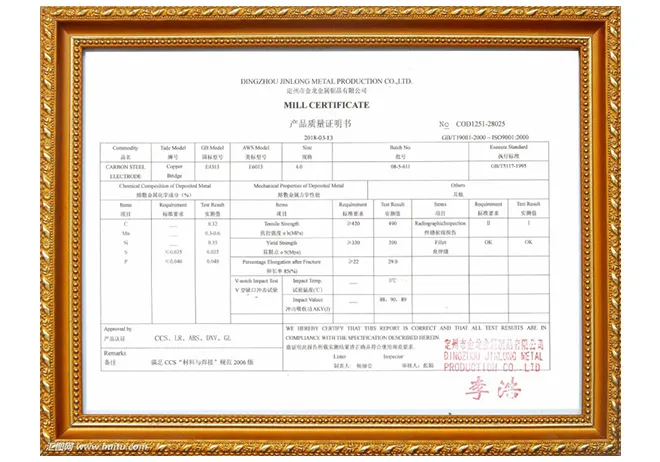
The last digit 8 in the 7018 classification corresponds to the characteristics of the coating, penetration depth, and current type. Specifically, the 8 indicates a low-hydrogen potassium, iron powder coating, which is conducive to direct current electrode positive (DCEP), also known as reverse polarity. This low-hydrogen aspect is a major benefit because it minimizes the risk of hydrogen-induced cracking, a common issue in welding that can weaken the structural integrity of the weld over time.
what does 7018 mean in welding
Another vital attribute of the 7018 electrode is its capability to produce a weld with a smooth, aesthetically pleasing finish. The flux coating substantially reduces spatter, a common by-product of the welding process, leading to a cleaner weld bead and reducing the need for post-weld cleanup. This not only saves time but also improves the overall appearance of the weld, which can be crucial for projects where visual appeal is as important as strength.
Professional welders often appreciate 7018 electrodes for their consistency and ability to handle heavy-duty applications. These electrodes are commonly found in industrial contexts such as shipbuilding, bridge construction, and heavy machinery manufacturing. Their compatibility with various steel alloys further widens their application scope, making 7018 a staple in a welder's toolkit.
However, to harness the full potential of 7018 electrodes, it's essential to maintain optimal storage conditions to preserve their low-hydrogen properties. Unused electrodes should be stored in a moisture-controlled environment, ideally in a heated cabinet or similar storage solutions designed to keep the coating intact. Exposure to moisture can compromise the electrode's integrity and lead to defective welds, undermining the strength and safety of the final weld.
In summary, understanding the significance of 7018 in welding can greatly influence the success and quality of a project. By selecting the appropriate electrode type, welders can ensure they achieve the desired tensile strength, weld position flexibility, and finish quality. This knowledge not only enhances the technical expertise of professionals but also affirms their capability to execute projects with a high standard of craftsmanship and reliability.