As an expert in welding and a trusted authority in metalworking practices, I’m excited to delve into the world of 7018 electrodes—an industry staple known for its versatility and professional-grade results. The 7018 welding rod is renowned for creating strong, crack-resistant welds in a variety of settings.
Here's an exploration of what you can effectively weld using this robust electrode.
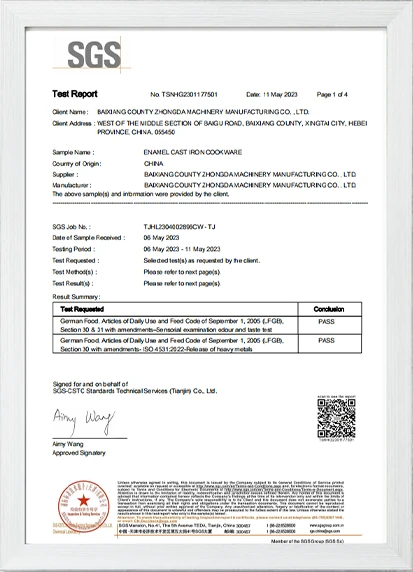
The 7018 electrode, often referred to as a low-hydrogen rod, is primarily utilized for welding carbon steel and low to medium carbon alloys. Its low-hydrogen flux coating is designed to produce a weld with minimal moisture content, thereby reducing the risk of hydrogen-induced cracking. This makes it highly suitable for critical applications where structural integrity is paramount.
Structural Steel Applications
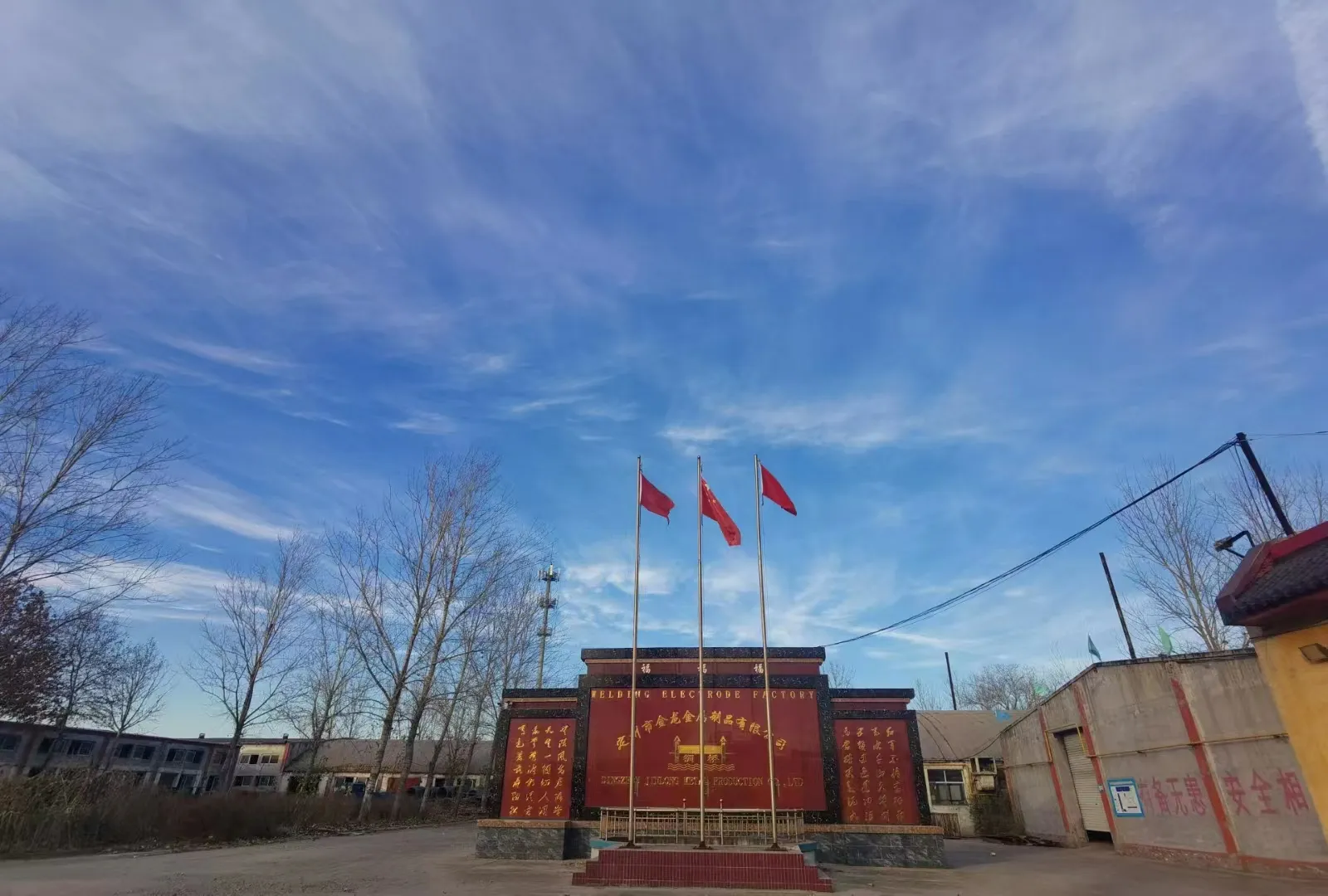
The 7018 rod is frequently used in the construction of buildings, bridges, and other infrastructure requiring high-strength welds. Its capability to produce a smooth, strong bead makes it ideal for thick sections of structural steel. Due to its low hydrogen potential, the 7018 electrode provides the resilience needed to endure stress and environmental factors over time, a critical factor in construction projects.
Boiler and Pressure Vessel Welding
Given its proficiency in limiting porosity and ensuring solid penetration, the 7018 electrode is also favored in the fabrication of boilers and pressure vessels. The reliability it provides under high pressure and temperature variations is invaluable. In industries such as oil and gas, where safety and durability are critical, 7018 offers peace of mind with welds that comply with stringent industry standards.
Pipe Welding
In pipeline construction, particularly when dealing with carbon steel pipes, 7018 is invaluable. Its capacity for creating ductile welds that can withstand substantial strain renders it indispensable for pipes transporting gases or fluids under high pressure. The electrode's consistent arc stability and ease of use contribute to its extensive application in this sector.
what can you weld with 7018
Heavy Equipment and Railroad Fabrication
Industries involving heavy equipment or railroad tracks benefit from the 7018's superior strength attributes. The rod is adept at joining heavy gauges of steel commonly found in machinery and rail infrastructure, ensuring durability and flexibility in the face of robust use. Its capability to maintain structural integrity under dynamic loads extends the lifespan of equipment and track systems.
General Repair and Maintenance
On a smaller scale, the 7018 electrode proves useful for general repair and maintenance work. Its adaptability to a range of metals, particularly carbon steels and certain alloys, allows welders to execute repairs on vehicles, farm equipment, and industrial machinery. Here, its ease of handling and forgiving nature in vertical and overhead positions are significant advantages.
Considerations and Best Practices
Utilizing 7018 electrodes requires a specific set of practices to maximize effectiveness and ensure quality welds. It's vital to maintain these rods in a low-moisture environment; some professionals advocate using electrode ovens to keep them dry and mitigate moisture absorption. When welding, professionals often emphasize the importance of maintaining the correct amperage and employing consistent travel speed to produce optimal outcomes.
For those venturing into projects requiring immaculately clean welds, pre-heating might be necessary, especially when working with thicker sections. This step minimizes heat input and helps to avoid defects. The post-weld treatment might also be essential in certain projects to relieve internal stresses and further enhance weld integrity.
Overall, the 7018 electrode is a fundamental tool in the welder's arsenal, providing unmatched versatility and reliability across a broad spectrum of applications. Its utilization underscores a commitment to excellence and safety, embodying qualities that professionals rely on in their pursuit of constructing strong, lasting welds that withstand the test of time.