Selecting the right welding rod for stainless steel is crucial for ensuring strong and durable welds, especially in professional applications where quality and precision are of utmost importance. Stainless steel is widely used across industries due to its corrosion resistance, durability, and aesthetic appeal. However, welding this metal presents unique challenges that require careful consideration and expertise.
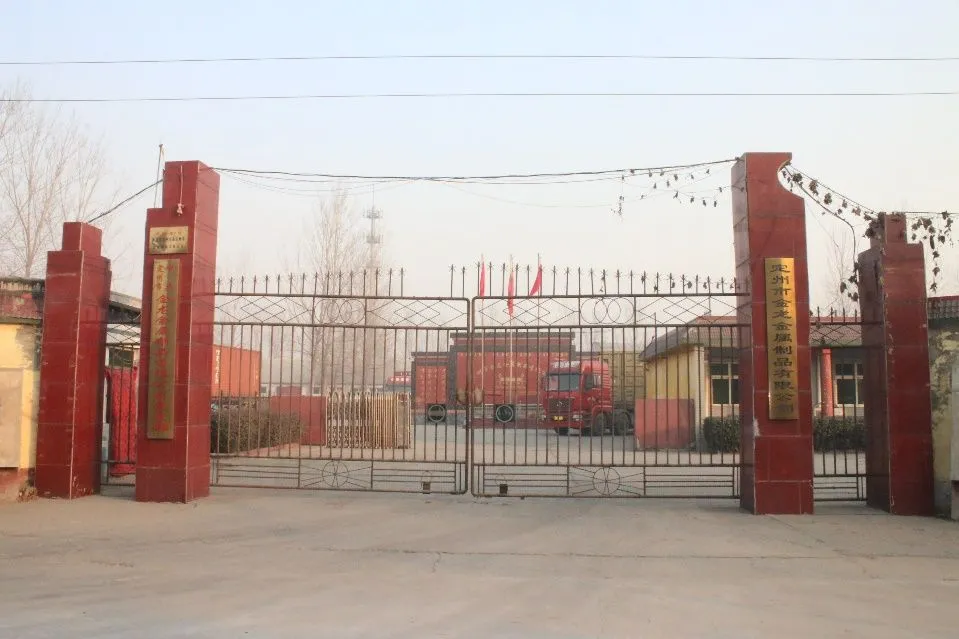
Understanding the composition of stainless steel is vital in choosing the appropriate welding rod. Stainless steel is an alloy primarily made from iron, chromium, nickel, and several other elements. The chromium content, which provides corrosion resistance, and the nickel content, which offers toughness, vary depending on the specific alloy grade. Common stainless steel grades like 304 and 316 have different properties and thus require different welding approaches.
Expert welders often turn to a few trusted types of welding rods that are specifically designed for stainless steel. One of the most widely used is the E308L-16 welding rod,
especially for 304-grade stainless steel. This rod is known for its low carbon content, which helps in minimizing carbide precipitation, a process that can lead to corrosion. For welding 316-grade stainless steel, the E316L-16 rod offers similar benefits, designed to handle the structure of 316 steel's molybdenum content, enhancing corrosion resistance in chloride environments.
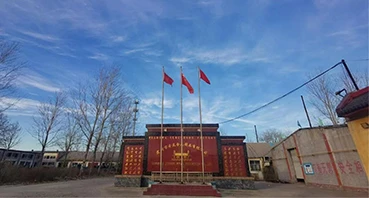
Another key consideration is the welding process itself. Shielded Metal Arc Welding (SMAW), Gas Tungsten Arc Welding (GTAW), and Gas Metal Arc Welding (GMAW) are commonly used methods. The expertise lies in selecting the right combination of rod and welding process to match the project requirements. GTAW, for instance, is revered for producing precise and clean welds on stainless steel, which is critical in industries like food processing and pharmaceuticals where hygiene is paramount.
welding rod used for stainless steel
The authority of a welder's choice extends beyond the mere selection of the welding rod; it encompasses the skillful application of welding techniques. Consistent, uniform welds free from defects such as hot cracking—a common pitfall with stainless steel—demonstrate professional prowess. Expertise in managing heat input, controlling welding speed, and choosing the correct shielding gas all contribute to the integrity of the weld.
Building trustworthiness with clients and stakeholders is essential for businesses dealing with stainless steel welding. Providing evidence of certified processes, such as those adhering to ISO standards or AWS certifications, underpins the reliability and quality of the welds produced. Transparency about the materials and methods used in welding projects further enhances trust. Ensuring traceability of welding rods and materials used, and maintaining meticulous records of welding procedures and outcomes, can provide clients with confidence in the durability and safety of the final product.
Real-world experience and in-field application provide invaluable insight that no amount of theoretical knowledge can match. Welders who have mastered the art of working with stainless steel offer invaluable advice always perform welding in a clean environment, maintain equipment precision, and never compromise on the quality of materials. These practices ensure the welds stand the test of time, resisting corrosion and structural failures.
In summary, the process of choosing and using welding rods for stainless steel is not just about technical specifications; it's a culmination of experience, expertise, authority, and trustworthiness. By prioritizing these elements, professionals can produce superior quality welds that meet the demanding standards of various industries. With meticulous approach and continuous skill enhancement, welding with stainless steel can achieve outstanding results.