Choosing the right welding rod is essential when joining stainless steel to mild steel, a process that demands precision and understanding of material properties. This article delves into the intricacies of this welding process, offering insights based on real-world experience and industry expertise to ensure optimal results.
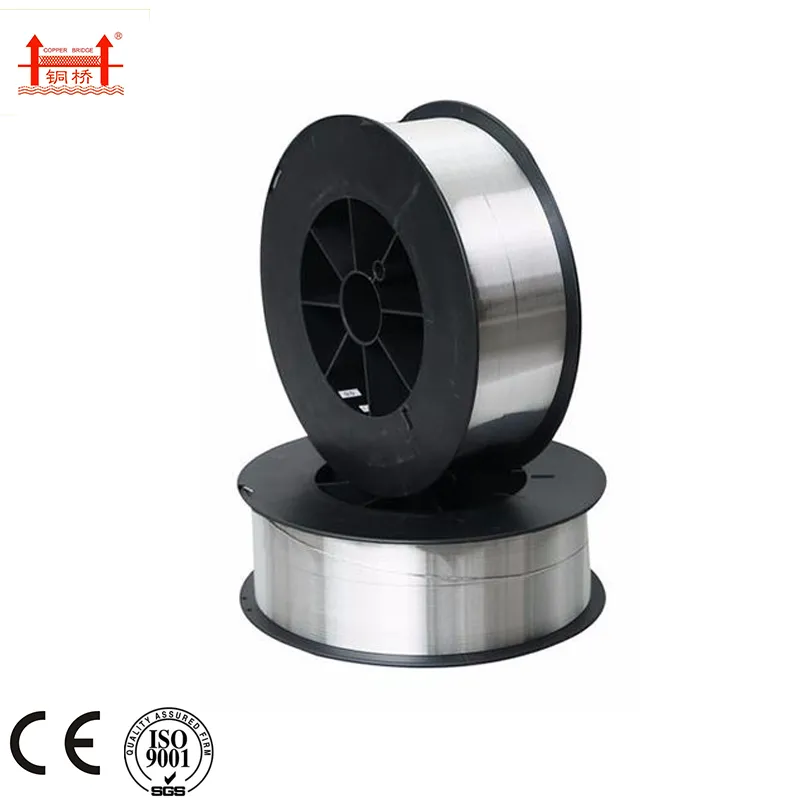
Understanding the Metallurgy Welding stainless steel to mild steel is fundamentally about merging two distinct metallurgical families. Stainless steel is known for its corrosion resistance and chromic properties due to its chromium content, typically above 10.5%. Mild steel, on the other hand, is composed primarily of iron with a small percentage of carbon, which makes it more malleable and less resistant to corrosion. Experts emphasize the importance of understanding these foundational differences, as they influence the choice of the welding rod and other parameters.
Selecting the Appropriate Welding Rod The choice of welding rod is critical in achieving a successful weld.
For joining stainless steel to mild steel, professionals often recommend using a 309L welding rod. This rod contains higher chromium and nickel contents, facilitating a smooth transition between the dissimilar metals and minimizing the potential for cracking. The 309L rod also helps maintain the corrosion resistance properties of stainless steel while accommodating the ductility of mild steel.
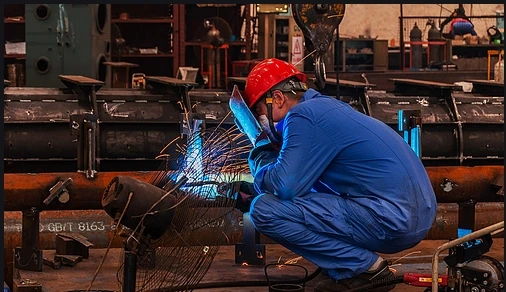
Pre-Weld Preparations Proper preparation is essential for achieving a high-quality weld. This involves thoroughly cleaning the surfaces of both metals to remove contaminants, rust, and oils that could inhibit fusion. Sandblasting or grinding the mild steel component can help create a cleaner, oxidation-free surface, improving the adhesion during welding. Additionally, maintaining a slight gap between the two metals can be beneficial in accommodating thermal expansion, a reflection of expertise gleaned from countless hours in the field.
Welding Techniques and Parameters When it comes to welding stainless steel to mild steel, the techniques employed can significantly influence the final outcome. Experts often advocate for TIG (Tungsten Inert Gas) welding due to its precision and control, although MIG (Metal Inert Gas) welding is also a viable option for thicker materials. Emphasizing controlled heat input to avoid overheating, welders should adopt techniques like intermittent welding to manage thermal stress. These practices not only prevent warping but also maintain the structural integrity of the weld.
welding rod stainless to mild steel
Post-Weld Considerations After completing the weld, it's vital to inspect the joint for integrity and potential flaws such as cracks or porosity. The cooling process should be gradual, as rapid cooling can lead to thermal shock and compromised strength. For enhanced durability, post-weld heat treatment can be employed to relieve internal stresses. This step, typically reserved for critical applications, showcases an authoritative understanding of both materials and welding processes.
Application-Based Expertise The utility of joining stainless steel to mild steel spans across various industries, from construction and automotive to food processing equipment. Each application poses its unique challenges and demands an authoritative approach. For instance, in the construction industry, the weld must withstand environmental elements, while in the food industry, maintaining the hygiene and corrosion resistance of stainless steel is paramount.
Building Trust Through Quality Assurance Consistently delivering high-quality welds is a testament to the trustworthiness of a welding professional or company. Adopting rigorous quality assurance protocols, such as non-destructive testing, can help in validating the weld’s strength and reliability. Such measures are indicative of a commitment to excellence and customer satisfaction, reinforcing confidence in the welding process.
In conclusion, welding stainless steel to mild steel, while challenging, is achievable through a nuanced understanding of both materials' properties. The expertise of selecting the correct welding rod, precise preparation and technique, and thorough post-weld evaluation are crucial in achieving a weld that stands the test of time. By leveraging professional knowledge and adhering to industry best practices, welders can ensure that their joints are robust, reliable, and meet the highest standards of quality.