Choosing the right welding rod is essential for ensuring the strength and durability of welded structures. This comprehensive guide on welding rod selection is crafted to give a novel perspective, offering practical insights based on real experiences while grounding the knowledge in expertise and authoritative guidance.
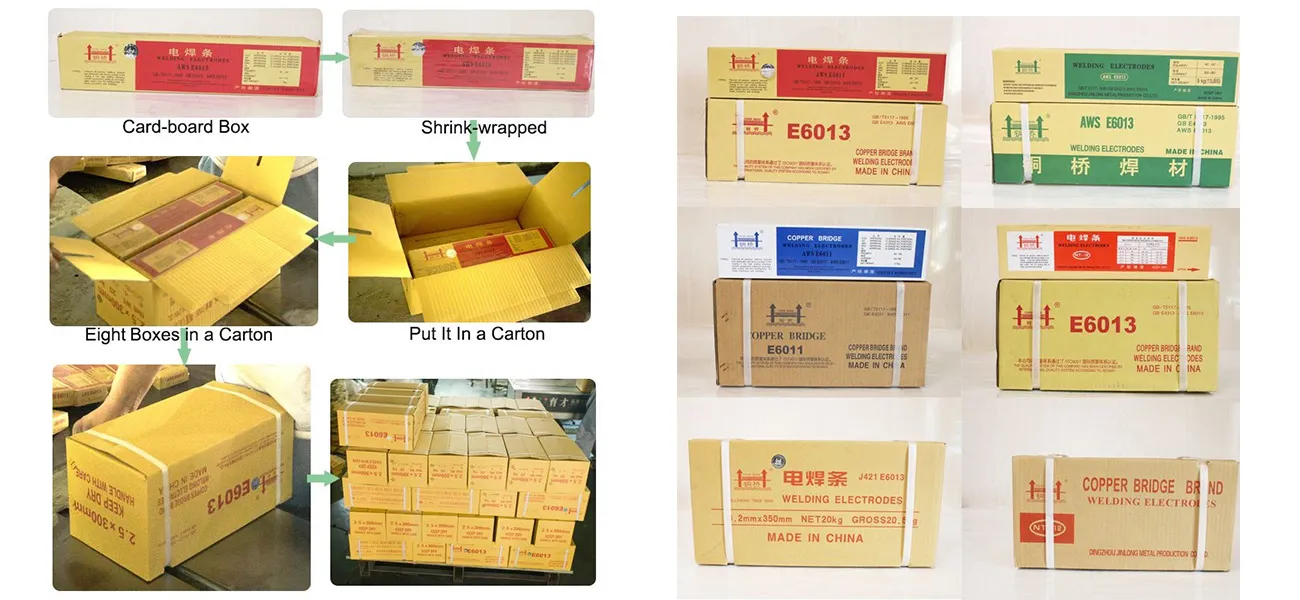
Understanding the nuances of welding requires an appreciation for the complexities of metallurgy and practical applications. Each welding project, whether industrial or DIY, presents unique challenges that are best addressed by selecting the optimal welding rod. Experienced welders acknowledge that the choice of electrode impacts not only the appearance of the weld but its structural integrity.
To begin, different types of welding rods are designed for various metals and welding techniques. Whether dealing with steel, stainless steel, cast iron, or aluminum, the electrode must be chosen based on the material properties and the specific requirements of the project. E6010 and E6011 rods, for instance, are noted for penetrating deep and forming durable welds, ideal for pipelines or structural work, especially with dirty or rusty surfaces. Their penetration power and ability to work with DC currents make them favorites among professionals tackling challenging repair jobs.
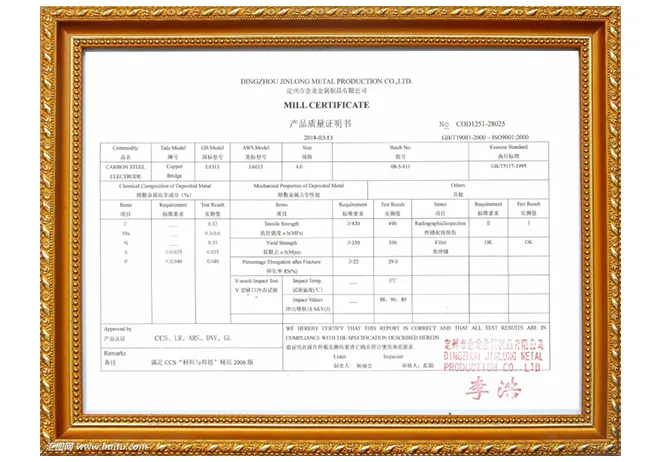
Conversely, E7018 rods have gained popularity for their low hydrogen composition, reducing the chances of cracking in heavy-duty applications. Welders operating in code-compliant environments trust these rods due to their reliability in creating strong, defect-free welds, especially in critical infrastructure projects like bridges or pressure vessels. Additionally, the smooth, clean welds these rods produce make them excellent for aesthetic projects.
The type of welding process also influences electrode selection. Shielded Metal Arc Welding (SMAW), with its versatility and simplicity, often employs E6013 for non-critical applications given its user-friendliness and ability to stabilize the arc. This rod produces less spatter, making it ideal for novice welders while still promising satisfactory results in light to medium gauge steel work.
welding rod selection guide
Consideration of the welding position is another critical factor. The electrode’s coating affects its usability in various positions—whether flat, vertical, horizontal, or overhead. E6010 rods are especially preferred for out-of-position welding due to their fast-freezing characteristics.
Breakthroughs in welding technology have introduced advanced rods that cater to specific industrial demands. Innovators in electrode manufacturing continually develop rods with unique specifications to reduce common welding challenges like splatter, slag inclusions, and porosity. Testing new products on the market when intricate or high-stakes projects arise not only keeps a welder's toolkit fresh but ensures that the latest technological advancements are harnessed for efficiency and precision.
Real-world experience helps refine the rod selection process. Experienced welders often emphasize the importance of electrode diameter, which correlates with material thickness. Using the correct diameter aids penetration and contributes to weld consistency, achieving both strength and appearance. Professional insights underscore that maintaining a stock of varied rods ensures preparedness for diverse project requirements, enabling immediate response to unexpected situations without compromising on quality.
In conclusion, successful welding demands a deep understanding of both theoretical knowledge and practical application. A methodical approach to welding rod selection, informed by material compatibility, welding position, and real-world conditions, ensures structural integrity and efficiency. As welding technology evolves, staying informed about new developments and innovations will contribute significantly to maintaining high standards of quality and trustworthiness in every welding endeavor.