When selecting the appropriate welding rod, many parts of welding and metalworking rely on a reliable and comprehensive selection chart. A well-structured welding rod selection chart is not just a reference tool; it is a cornerstone of effective and high-quality welding practices. Ensuring your choice of welding rod meets your project's specific requirements can significantly influence the durability and strength of the weld, as well as the overall structural integrity of the workpiece.
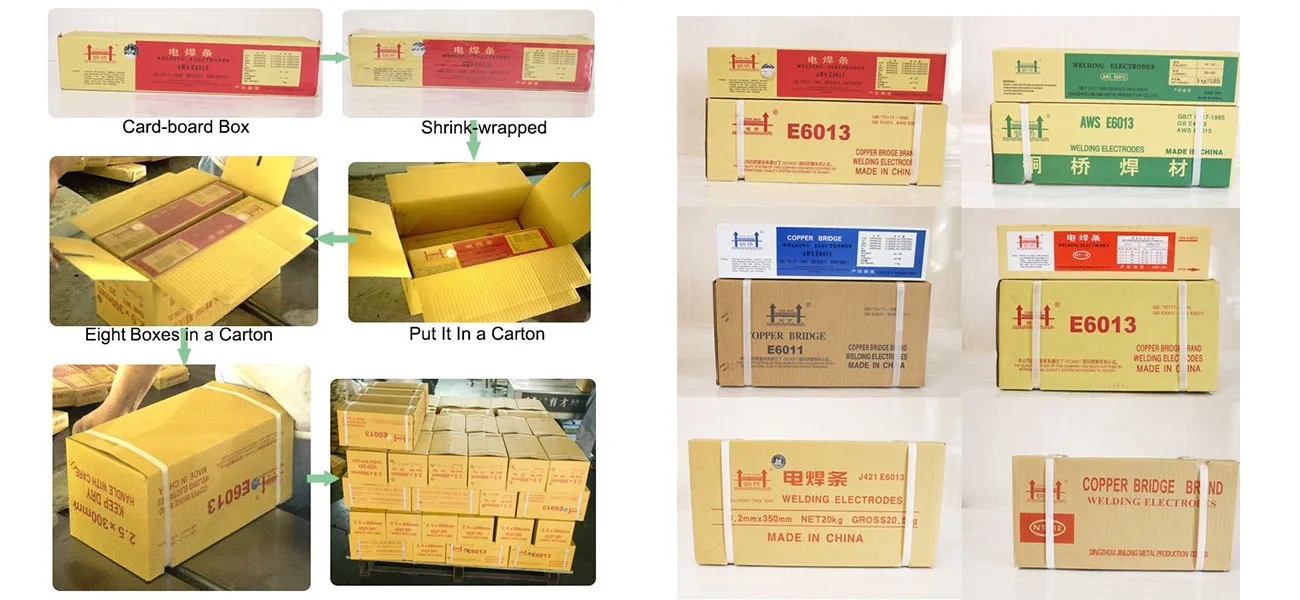
The welding rod selection chart offers detailed insights into numerous factors, including material type, electrode coating, welding position, current type, and base metal thickness. Experienced welders understand that the key to successful welding lies in matching the rod to the specific conditions of the job.
Material type is perhaps the most critical starting point. Different metals require different rods, with commonly welded metals including mild steel, stainless steel, cast iron, and aluminum. Each of these materials has unique properties that respond differently to heat, and therefore, selecting an electrode that complements these characteristics is vital for achieving a quality weld. For instance, mild steel welding often utilizes E7018 rods known for their versatility and ability to produce strong welds with good deposition rates.
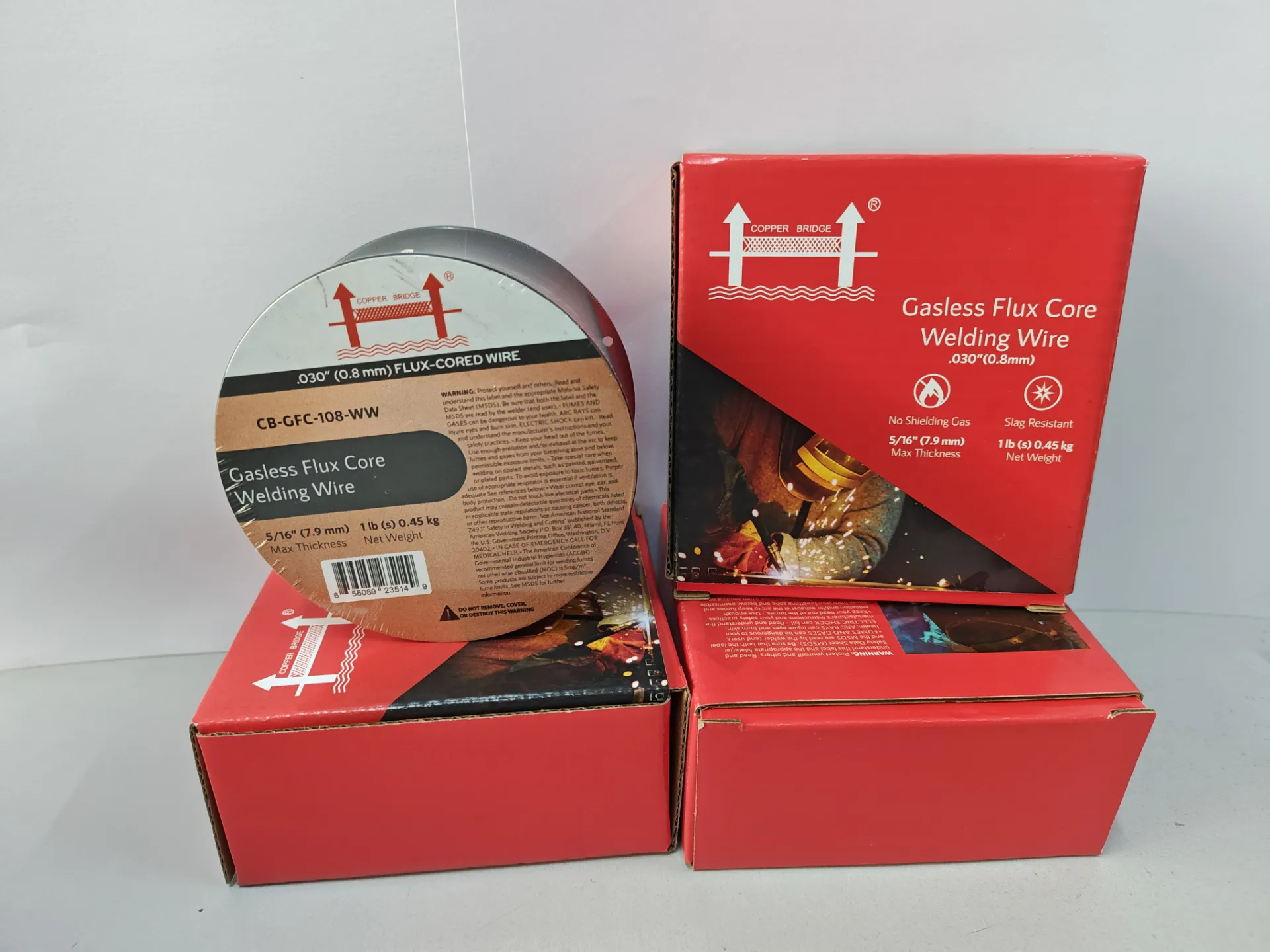
Electrode coating is another crucial component that cannot be overlooked. Coatings can vary significantly between rods, affecting penetration depth, arc stability, and slag formation. Depending on your project requirements, you might need a rod with a specific type of coating, such as iron powder for better deposition rates or cellulose for deep penetration.
The welding position is also fundamental in making your choice. Depending on whether your welds will be flat, horizontal, vertical, or overhead, different rods will perform better in different scenarios. Some rods, like the E6010, are renowned for their ability to maintain performance regardless of position, providing flexibility and convenience in less-than-ideal conditions.
welding rod selection chart pdf
The type of current—whether AC or DC—impacts rod choice as well. Some electrodes, such as the E6011, are versatile enough to work well with both AC and DC currents, making them suitable for a variety of welding machines and applications.
Finally, the thickness of the base metal is an important consideration. Thinner metals typically require lower amperage settings and smaller diameter rods to prevent burn-through and warping. Conversely, thicker materials might necessitate larger rods and higher amperage for adequate penetration and fusion.
Incorporating these considerations into the welding rod selection chart maximizes its value as a tool. It transforms the chart from a mere list of options into a comprehensive guide that aids in decision-making, ensuring that each weld is as strong and reliable as possible.
In conclusion, utilizing a well-structured welding rod selection chart can drastically improve both the efficiency and quality of welding projects. By factoring in material type, electrode coating, welding position, current type, and metal thickness, the chart becomes an indispensable resource for achieving optimal welds. Whether for novice welders seeking guidance or seasoned professionals ensuring precision, the welding rod selection chart remains integral to successful metalworking projects.