Welding rods, especially those designed for tubular structures, are indispensable tools in construction, fabrication, and a variety of industrial applications. Ensuring that these rods meet both performance and quality standards is essential to the success of any project. Here, we explore the intricacies and considerations for selecting the optimal welding rod for tubular applications, aiding in the delivery of superior welds with lasting integrity.
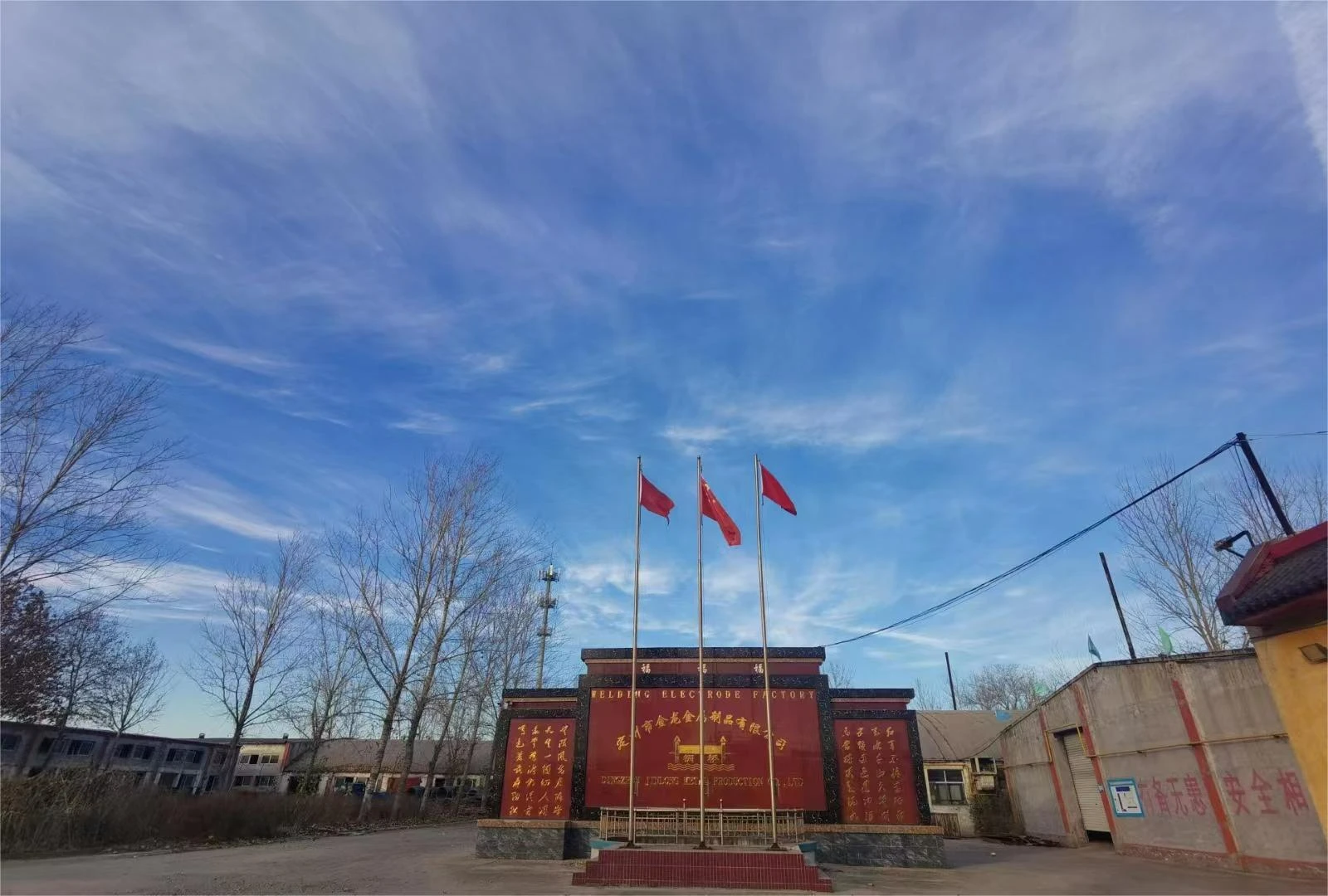
Tubular structures present unique challenges in welding due to their geometric complexity and the variety of material compositions. The welding rods used must accommodate these unique variables to ensure a weld that is both strong and durable. For tubular structures, welding rods must ensure proper penetration and fill in the weld joints, enhancing load-bearing capacities and extending the lifespan of the structure.
One crucial aspect to consider when selecting welding rods for tubular applications is the base material. Tubing can be made from a variety of materials, including steel, stainless steel, and aluminum, each requiring specific rod types. For instance, when working with carbon steel tubes, E7018 rods are often recommended due to their all-position capability and smooth finish. In contrast, stainless steel tubes may require E308 or E309 rods to prevent corrosion and maintain metallurgical compatibility.
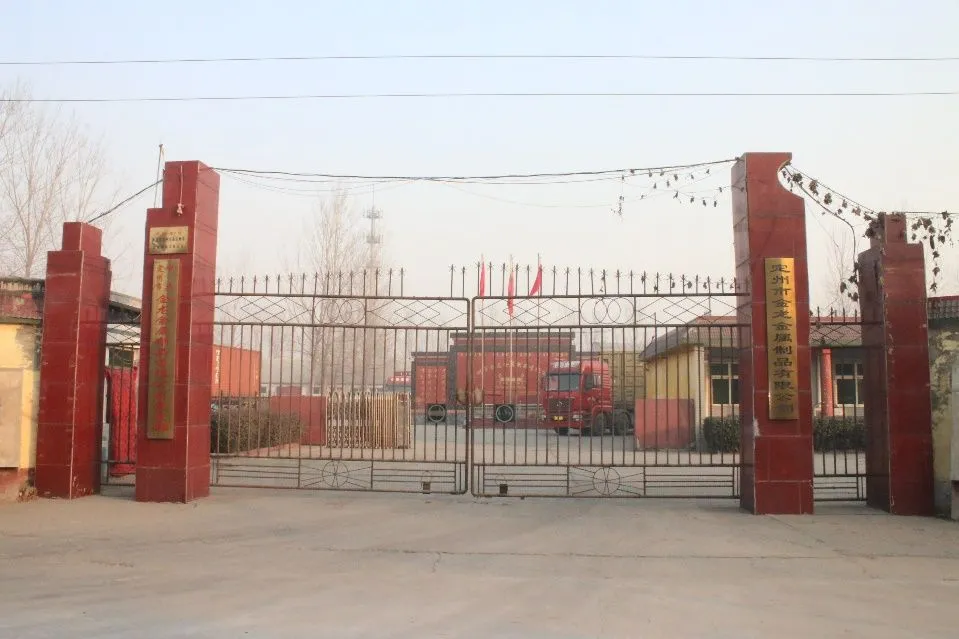
Expertise in welding techniques also plays a vital role. Professionals experienced in welding tubular structures recognize the importance of controlling heat input and travel speed to prevent warping and ensure the structural integrity of the tube. Proper technique reduces the occurrence of welding defects such as porosity and cracking, which are critical in applications like pipeline construction or automotive frames where failure is not an option.
welding rod for tubular
The authority of a welding rod manufacturer is another factor that should be weighed carefully. Established manufacturers with a reputation for quality assurance and testing protocols offer an added layer of trust. Products from these manufacturers typically come with data sheets detailing mechanical properties, recommended application scenarios, and safety guidelines. This information is pivotal for ensuring compliance with industry standards and achieving reliable results.
Moreover, trustworthiness extends into the supply chain and customer service offered by the welding rod provider. Suppliers who ensure timely delivery and offer technical support can significantly mitigate the risks associated with project delays and unexpected challenges. An accessible and responsive customer service team can provide insights and solutions to optimize welding processes, further enhancing productivity and welding quality.
Finally, investing in quality welding rods tailored for tubular structures aligns with a long-term vision of structural reliability and safety. The meticulous selection of the appropriate welding rod, matched with skilled execution, contributes not only to the immediate success of a project but also to its sustained performance under operational stresses.
In conclusion, the importance of selecting the right welding rod for tubular applications cannot be overstated. By considering factors such as material compatibility, manufacturer credibility, and expert welding techniques, industrial professionals can ensure robust, high-quality welds. This methodical approach supports both the functional requirements and the safety standards necessary for modern engineering ventures, ultimately delivering projects that stand the test of time.