When it comes to assembling strong and durable structures, welding iron rods is an indispensable skill in the field of construction and metalwork. Understanding the technical nuances of welding these essential components can significantly impact the quality and longevity of a project. This article delves into the intricacies of welding iron rods, encompassing practical experience, expert insights, and authoritative guidance to enhance usability and reliability.
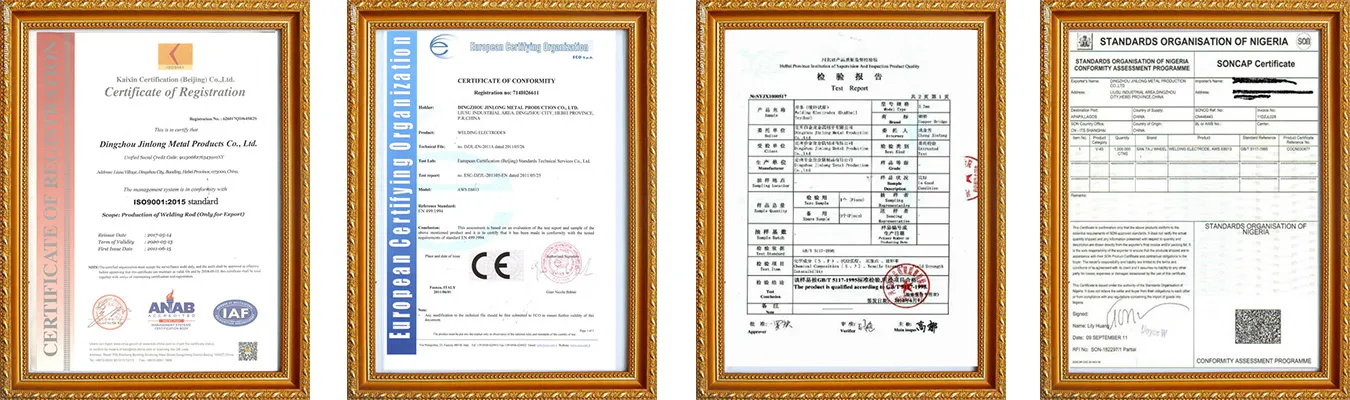
Iron rods have been the backbone of civil engineering projects for centuries, providing structural integrity to buildings, bridges, and frameworks. The versatility of iron rods makes them a popular choice for various applications, from reinforcing concrete to constructing intricate metal frameworks. However, welding these rods requires a high level of skill and precision to ensure a secure and lasting bond.
One of the fundamental aspects of successfully welding iron rods is selecting the appropriate welding technique. Among the many techniques available, Shielded Metal Arc Welding (SMAW) and Flux-Cored Arc Welding (FCAW) are often preferred for their effectiveness with iron and steel. SMAW, commonly known as stick welding, is celebrated for its simplicity and adaptability in outdoor and indoor environments. It is particularly effective for joining thick iron rods, where deep penetration is required. On the other hand, FCAW is advantageous in situations demanding higher deposition rates, providing robust joints in large-scale projects.
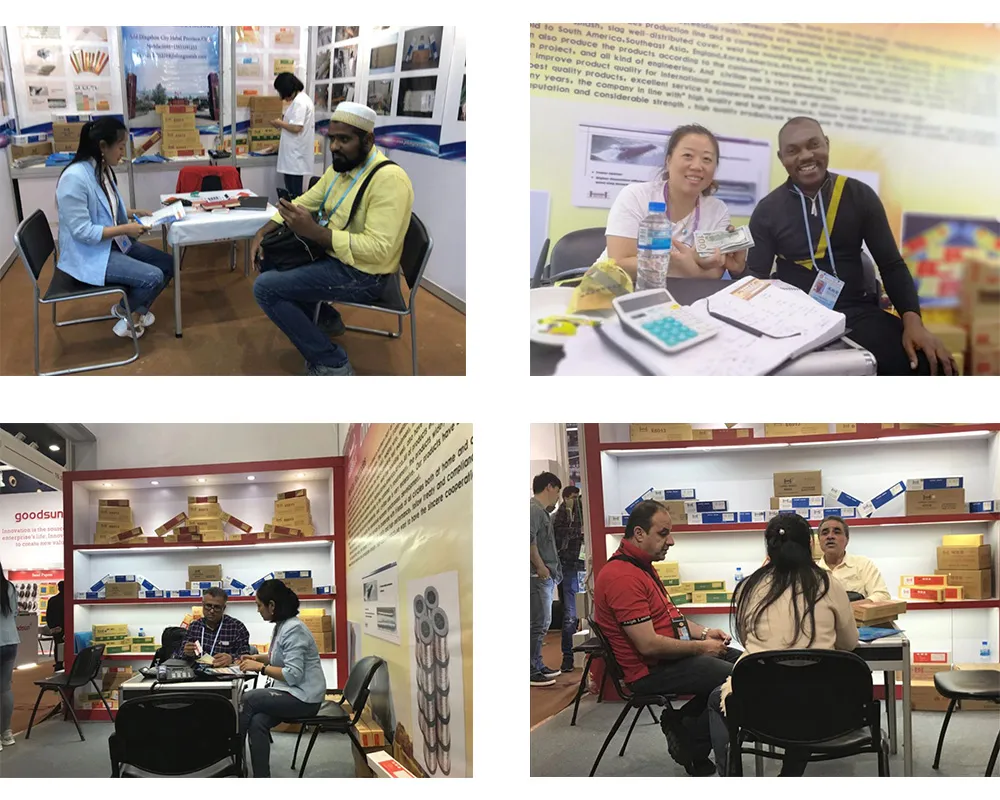
Safety is paramount in any welding operation. Experienced welders emphasize the importance of personal protective equipment (PPE), including helmets, gloves, and protective clothing. Iron rods, when welded, generate intense heat and ultraviolet radiation, posing risks such as burns and eye damage. Welders must ensure their workspace is well-ventilated to prevent the accumulation of hazardous fumes released during the welding process. Furthermore, recognizing the potential structural implications of improperly welded joints underscores the necessity of thorough inspection and quality control.
The expertise involved in welding iron rods extends to the understanding of materials. Iron, with its tendency to oxidize, necessitates careful preparation before welding. Removing rust and contaminants from the surface is essential to achieve a clean joint. It’s common practice to employ wire brushes or chemical rust removers to prepare the rods adequately. Additionally, selecting the right filler material is critical. The filler must complement the iron's characteristics and match the mechanical requirements of the project. Quality welding rods with appropriate tensile strength and corrosion resistance ensure a uniform and strong weld.
welding iron rods
Authoritative guidance is vital in fostering credibility and trust in welding operations. Adhering to industry standards and codes, such as those outlined by the American Welding Society (AWS), ensures that work meets safety and quality benchmarks. AWS standards provide a framework for procedures, qualifications, and specifications that govern welding processes, guaranteeing a uniform approach across different projects.
In terms of trustworthiness, engaging certified welders or professionals with a proven track record is crucial. Their experience can mitigate potential risks and enhance the outcome's reliability. Consulting with industry veterans or seeking training and certification from accredited institutions bolsters a welder's capabilities and confidence.
Projects that involve welding iron rods benefit from meticulous planning and execution. Understanding load-bearing capacities, environmental considerations, and structural demands is imperative. Collaboration among engineers, architects, and welders ensures that the final product is not only functional but also adheres to aesthetic and regulatory requirements.
In conclusion, the process of welding iron rods is a complex interplay of skill, knowledge, and precision. Harnessing the right techniques, prioritizing safety, understanding materials, adhering to standards, and leveraging expert insights are all integral elements that contribute to the successful execution of welding projects. Whether it’s constructing a towering skyscraper or a simple reinforcing framework, the meticulous craftsmanship involved in welding iron rods stands as a testament to human engineering and innovation.