When it comes to welding cast iron to mild steel, selecting the right welding electrode is paramount. This matter, while technical, speaks directly to both seasoned professionals and novices looking to bridge these two distinct metals effectively. The challenges involved are well documented, yet the solutions continue to evolve as technology advances in the metallurgy and welding fields.
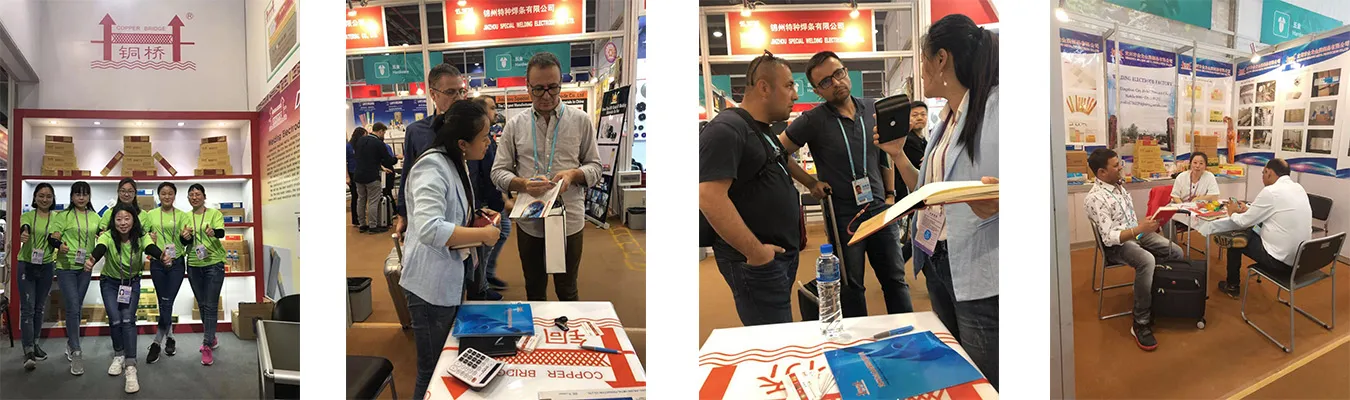
Welding cast iron to mild steel is complex due to their differing properties. Cast iron, known for its high carbon content, exhibits brittleness and different thermal expansion characteristics compared to the more ductile mild steel. The welding process must therefore accommodate these differences to achieve a robust bond.
A popular and effective choice for this task is the nickel-base electrode. Nickel electrodes offer several advantages, primarily due to their ability to absorb carbon from the cast iron, minimizing cracking risks. Two common types include pure nickel 99% electrodes and nickel-iron (55% nickel) electrodes. Pure nickel electrodes, while costlier, produce softer and machineable welds, which is ideal for applications requiring post-weld machining.
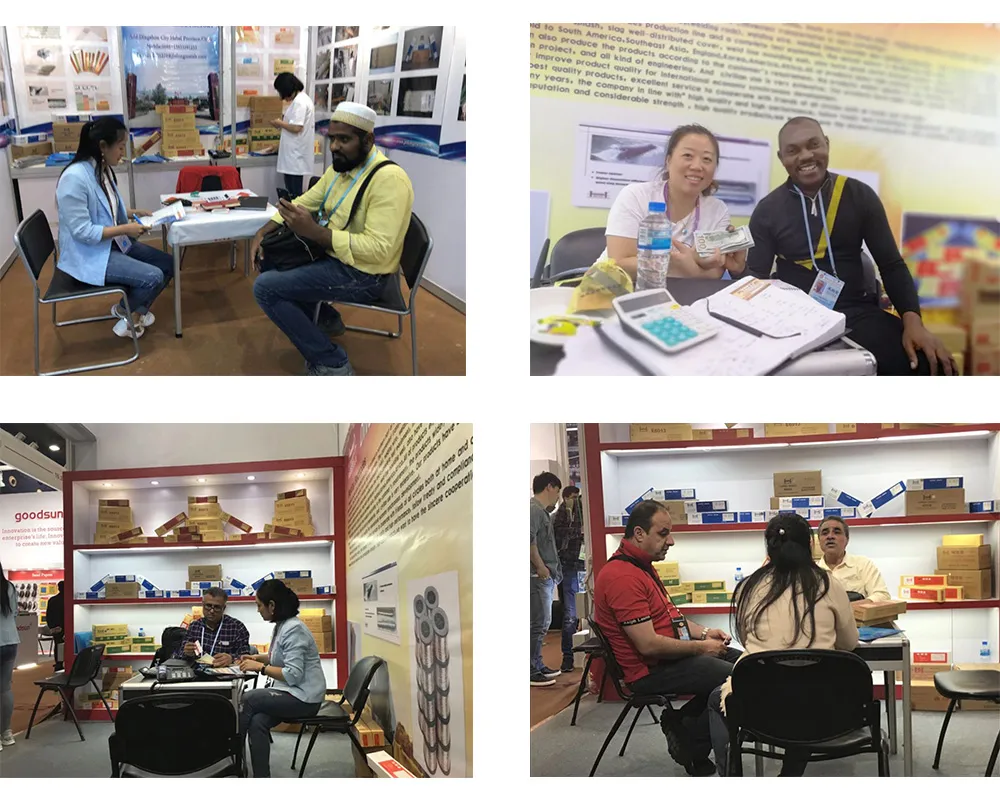
In practice, selecting the nickel-iron electrode can be beneficial for larger structures where strength is a paramount concern. These electrodes are more affordable and offer greater weld strength, although the weld might be less machinable compared to pure nickel electrodes. Ensuring pre-heat treatment of the cast iron part before welding and controlled cooling post-welding, can mitigate thermal shock and stress cracking. This process aligns perfectly with best practices in handling varied thermal expansion rates between the two metals.
Furthermore, another modern solution includes the use of stainless steel electrodes. These help by creating a cushion layer that balances the differing expansion rates and adds a layer of corrosion resistance. The welding community often trusts 309 or 312 stainless steel electrodes for their versatile compatibility with both cast iron and mild steel.
welding electrode for cast iron to mild steel
Another crucial consideration is the skill of the welder. Even with the most suitable electrode, the welder's proficiency largely dictates the joint quality. Skilled interpretation of the electrode’s performance, adjusting for heat and electrode angle, can bridge the gap between theory and practice. Professional training, therefore, is strongly recommended for those undertaking such projects. This experience factor cannot be overemphasized and can result in either a successful weld or a compromised joint prone to failure.
In addition, consistent quality checks and stress tests post-welding educate the welder about potential fracture points, which assists in future endeavors. Coupled with a thorough understanding of metallurgical principles, these evaluations enhance both the welder’s skillset and the reliability of the welds produced.
For industry professionals seeking authoritative guidance, referencing works and publications by institutions like the American Welding Society (AWS) can equip welders with the latest best practices and theoretical insights. Their certifications often demonstrate a commitment to maintaining high standards, boosting the trustworthiness and credibility of professional welders.
Whether you are an engineer, fabricator, or a DIY enthusiast, understanding the intricate dynamics between cast iron and mild steel, and selecting the appropriate welding electrode solution, can greatly affect the outcome of your project. The focus on niche expertise, leveraging the right tools, and understanding material science culminate in a superior welding experience that stands the test of time. Through ongoing education and adherence to industry standards, optimal outcomes in welding projects involving cast iron to mild steel are attainable and repeatable.