Selecting the right welding electrode is crucial for the success of any welding project, whether it's in construction, manufacturing, or repair work. Welding electrodes play a pivotal role in determining the quality and durability of the weld. This guide focuses on providing professional insights into welding electrode specifications, ensuring that your choice meets project demands and regulatory standards.
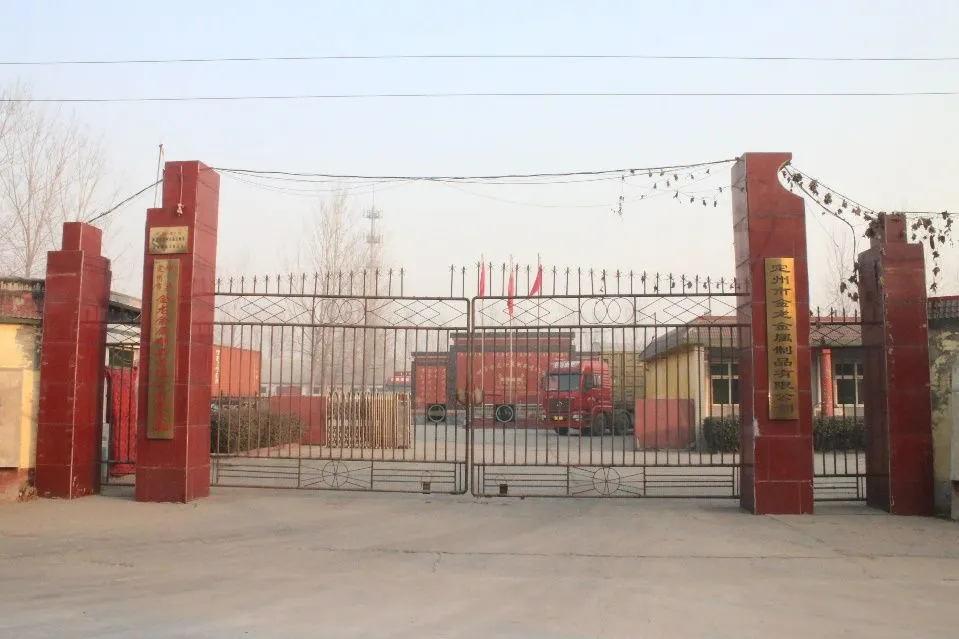
A comprehensive understanding of the electrode specifications begins with the American Welding Society (AWS) classification. Most electrodes used today conform to AWS standards, which assure quality and uniformity. For instance, an AWS classification like E6010 denotes crucial attributes; 'E' stands for electrode, '60' refers to the tensile strength of 60,000 psi, '1' indicates the electrode's position usability, and '0' identifies specific coating characteristics and current type usability. Understanding this classification equips professionals to make informed decisions matching weld requirements to electrode specifications.
Each type of material being welded requires different electrode specifications to maintain the structural integrity of the weld. For example, carbon steel demands electrodes such as E7018 due to their high tensile strength and adaptability across multiple positions. Stainless steel, on the other hand, typically utilizes electrodes like E308L-16, which are designed to resist cracking and ensure durability under harsh environmental conditions.
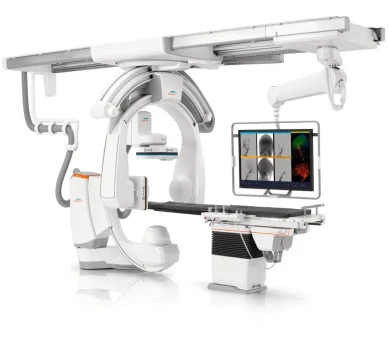
Professional expertise is vital in navigating the complexities of electrode coatings. These coatings play an essential role in stabilizing the arc, shielding the molten metal from atmospheric contamination, and affecting the weld's mechanical properties. Rutile-coated electrodes, with their smooth arc and low spatter, are preferred for providing aesthetic finish and ease of use, while basic-coated electrodes offer superior mechanical properties for high-stress applications.
In terms of practical experience, seasoned welders often share insights about matching electrode diameter to the workpiece's thickness; smaller diameters are suitable for thin materials to prevent burn-through, while thicker materials require larger diameters for adequate penetration and fusion. This hands-on knowledge amplifies the theoretical specifications, ensuring that real-world applications meet all safety and structural criteria.
welding electrode specifications
Moreover, the handling and storage of electrodes heavily influence their performance. Electrodes must be kept in a moisture-controlled environment to prevent hydrogen-induced cracking, a common defect in welding where moisture absorbed by the electrodes deteriorates the weld integrity. Therefore, using electrode ovens or sealed containers ensures optimal performance and longevity of stored electrodes.
Furthermore, product reliability is bolstered by selecting electrodes from reputable manufacturers known for rigorous quality control and compliance with industry standards. A trusted supplier not only guarantees product consistency but also offers technical support and guidance in choosing the right specification according to specific project demands.
Trustworthiness in welding comes from matching the right electrode specification to the job requirement, underpinned by a thorough understanding of material properties, electrode coatings, and application techniques. Reviewing comprehensive product datasheets and leveraging expert consultation can significantly boost confidence in welding outcomes.
In summary, selecting welding electrodes necessitates a blend of theoretical knowledge, practical experience, and a keen attention to specification details. By adhering to rigorous standards and leveraging the expertise of seasoned professionals, project leaders can ensure that their welding activities are performed with precision, reliability, and excellence, ultimately delivering safe and robust structures.