The manufacturing process of welding electrodes is a meticulously crafted procedure that underscores years of scientific expertise, precise engineering, and stringent quality control measures. It reflects not just the evolution of the industry but also the accumulated wisdom and innovations that have elevated welding to an art form. The journey from raw materials to finished electrodes embodies a commitment to excellence, underscoring the industry's pledge to deliver products of superior performance and unmatched reliability.
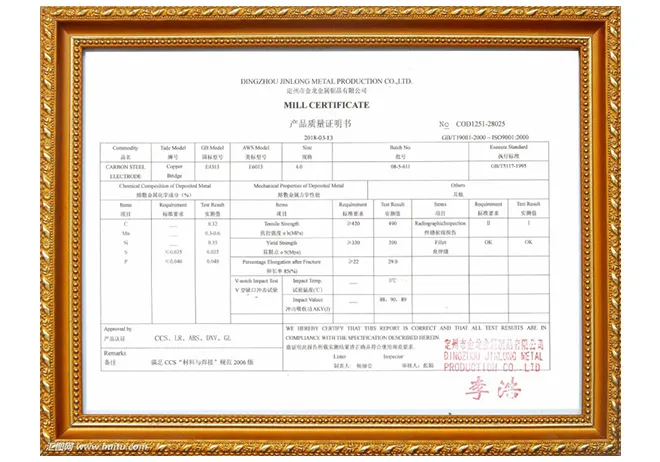
To begin, the selection of core wire is paramount. High-quality steel is chosen based on its chemical composition, which directly affects the electrode's performance. The diameter of the core wire is meticulously controlled to meet specific standards essential for achieving consistent welding results. This steel wire is drawn through dies to reach the desired thickness, ensuring uniformity throughout the production process.
The next stage is coating, an intricate process that enhances the electrode's abilities. The coating is composed of minerals, ferroalloys, and proprietary binders — elements carefully measured and mixed to create a slurry. This mixture is then applied to the wire core via a precision extrusion process, ensuring a uniform thick layer. The coating's composition is crucial as it determines the electrode's arc characteristics, slag formation, penetration, and overall welding quality.
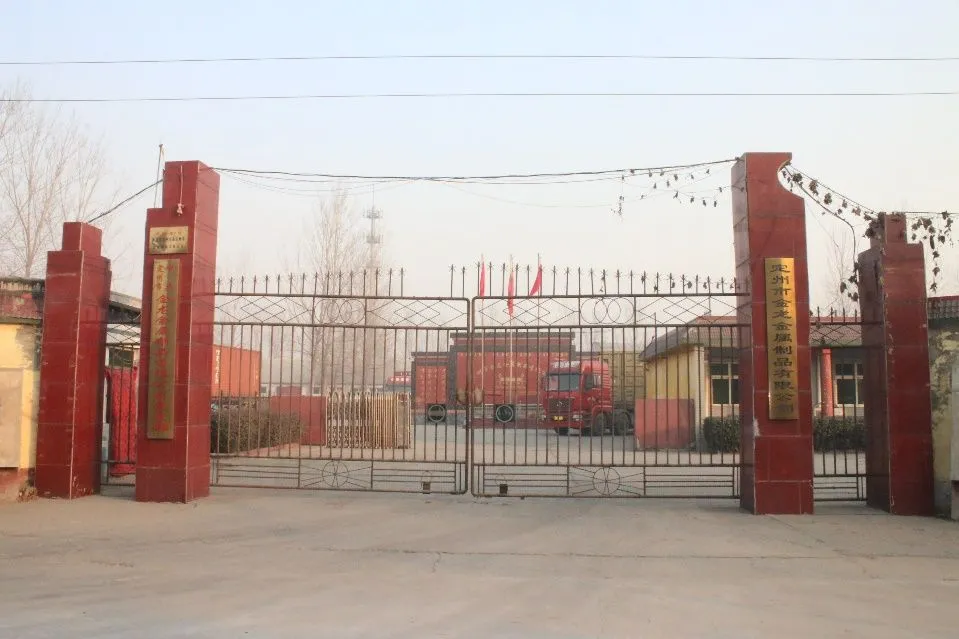
Following the coating process, electrodes undergo a drying and baking phase. This is conducted in controlled atmospheres to eliminate moisture and achieve the desired coating hardness. The temperature and duration of the drying process are critical parameters that can significantly influence the electrode's performance. This step is pivotal in enhancing the durability and usability of the electrodes in various welding environments.
welding electrodes manufacturing process pdf
Quality control is woven into every step of the manufacturing process to uphold the integrity of the product. Stringent tests are conducted to assess physical dimensions, consistency of the coating, and mechanical properties. The electrodes are also subjected to rigorous performance evaluations in welding operations to ensure they meet predefined welding standards. Only those that meet or exceed these stringent criteria are deemed fit for distribution.
The packaging of welding electrodes is another area where precision and care are paramount. Designed to protect against environmental factors like moisture or mechanical damage, the packaging ensures that the electrodes preserve their integrity until they reach the end-user. Additionally, clear labeling provides critical information regarding the type, diameter, and recommended usage of the electrodes, facilitating ease of use.
In conclusion, the manufacturing process of welding electrodes is a testament to the blend of tradition and innovation. It is characterized by a detailed series of operations that require expert knowledge and unwavering attention to detail. For manufacturers, this is not only a business process but an ongoing commitment to providing tools that empower professionals around the globe. Trust and authority in the welding industry are built on a foundation of consistent quality and performance, ensuring that when a welder picks up a set of electrodes, they are holding the result of decades of expertise, innovation, and passion for excellence in their field.