Welding electrodes play an essential role in the welding process, serving as the filler metal that bonds two pieces together. A deep understanding of electrodes can dramatically enhance the quality of your weld, regardless of whether you're a seasoned professional or a passionate hobbyist. This article discusses welding electrodes from a product-focused viewpoint, expounding on their essential features, applications, and how to select the right one for your project.
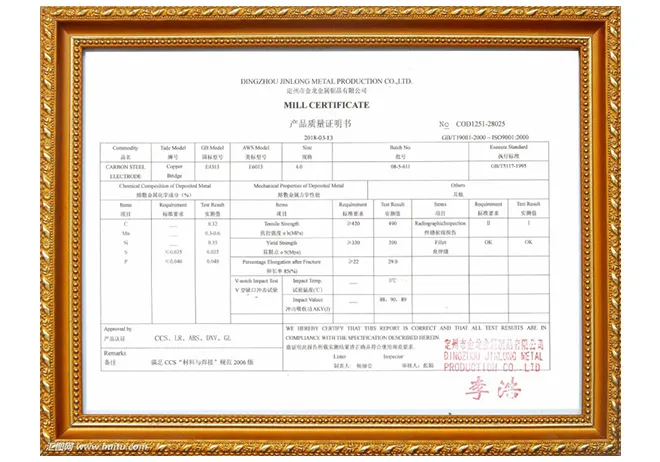
At the heart of any welding operation, electrodes serve as the conductive metal rods that are used to close the welding circuit and provide filler metal for the joint. The two main types of electrodes are consumable and non-consumable. Consumable electrodes melt and become part of the weld pool, while non-consumable electrodes do not melt and are used in processes like TIG welding where the filler metal is introduced separately.
For consumable electrodes, one of the most common is the shielded metal arc welding (SMAW) electrode, often known as the stick electrode. These are available in a variety of sizes and compositions, typically characterized by their American Welding Society (AWS) classification, such as E6010 or E7018. Each electrode type has attributes that make it suitable for specific materials and welding positions.
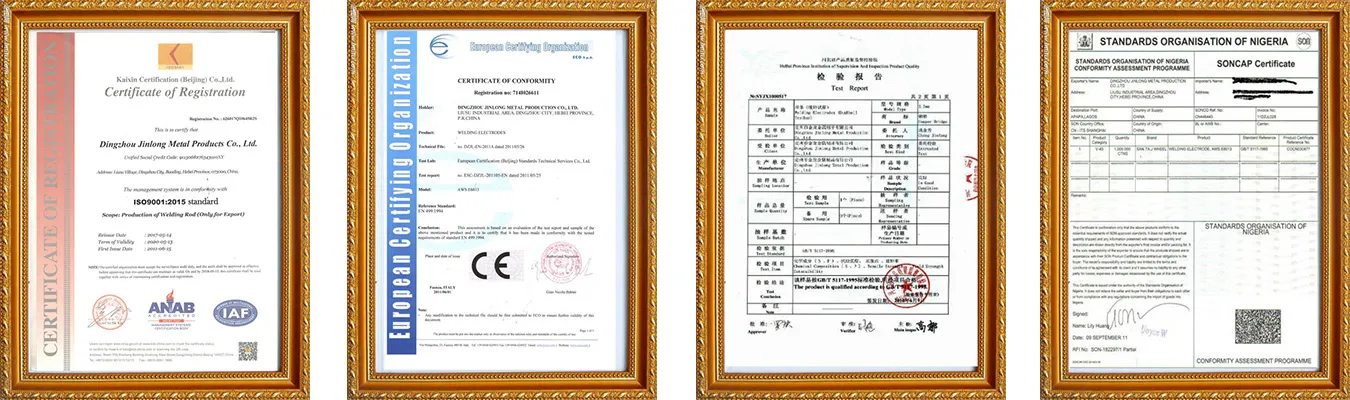
The coatings on these electrodes are not merely cosmetic; they offer several functions. They stabilize the arc, protect the weld pool from contamination, and sometimes even influence the mechanical properties of the weld. For instance, acidic coatings offer deep penetration, whereas rutile coatings allow for a smoother arc and finer appearance.
When choosing the right electrode, consider the material you'll be welding. For instance, if you're working with mild steel, an E7018 electrode might be ideal due to its high strength and ductility, combined with relatively easy handling. However, for more robust and corrosion-resistant welds, such as those required in stainless steel welding, specialized electrodes such as E308L are appropriate.
welding electrodes explained
Furthermore, understanding the position in which you'll be welding can guide your electrode choice. Some electrodes are versatile and can be used in all positions (flat, horizontal, vertical, and overhead), while others specialize in either vertical or flat positions. For instance, E6010 is valued for its deep penetration and versatile position use, making it suitable for root passes in pipe welding.
In addition to the material and position, the power source being used also impacts electrode selection. Certain electrodes are designed for alternating current (AC), while others work best with direct current (DC). Knowing your equipment's capabilities ensures you select an electrode that will function optimally with your setup.
Storage and care of welding electrodes is another point of consideration. Proper storage conditions, such as a dry, climate-controlled environment, extend the life of your electrodes and prevent moisture-induced issues like hydrogen cracking. It's advisable to individually inspect electrodes before use, ensuring they are free of rust or any coating damage.
Safety should never be overlooked. Appropriate gear, including gloves, protective eyewear, and ventilation systems, is essential during welding to avoid injuries from high temperatures, sparks, and harmful fumes.
In summary, the adept selection and use of welding electrodes can significantly influence the quality and durability of your welds. By understanding the different types of electrodes, their appropriate applications, and how to handle them correctly, you position yourself not just as a user, but as a master of your welding craft. From the right electrode, a world of superior welding awaits.