Welding all rods requires a blend of skills, expertise, and the right equipment to ensure high-quality results. This guide provides insights and professional tips for achieving the perfect weld, enhancing your craftsmanship and ensuring durability and reliability in your projects.
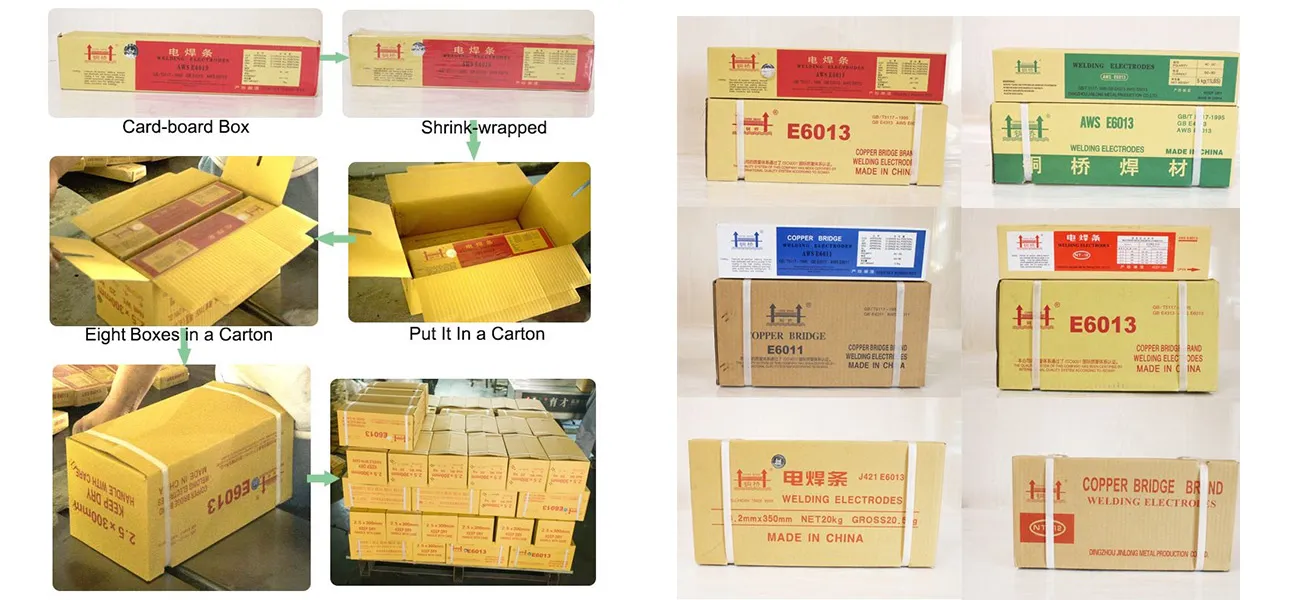
The first step in welding rods is selecting the appropriate type for your specific application. Typically, welding rods are designed for different kinds of metalwork, including steel, aluminum, and other alloys. Knowing the properties of each type of metal is crucial, as it directly influences the choice of welding rod. For example, steel rods are generally used for construction projects due to their strength and ease of use, while aluminum rods are preferred for their lightweight and corrosion-resistant properties.
Having the right tools is equally essential. Invest in a high-quality welding machine capable of adjusting parameters like amperage and voltage, as these factors significantly affect the quality of the weld. A versatile machine that can handle different types of rods can be a pivotal factor in your success.
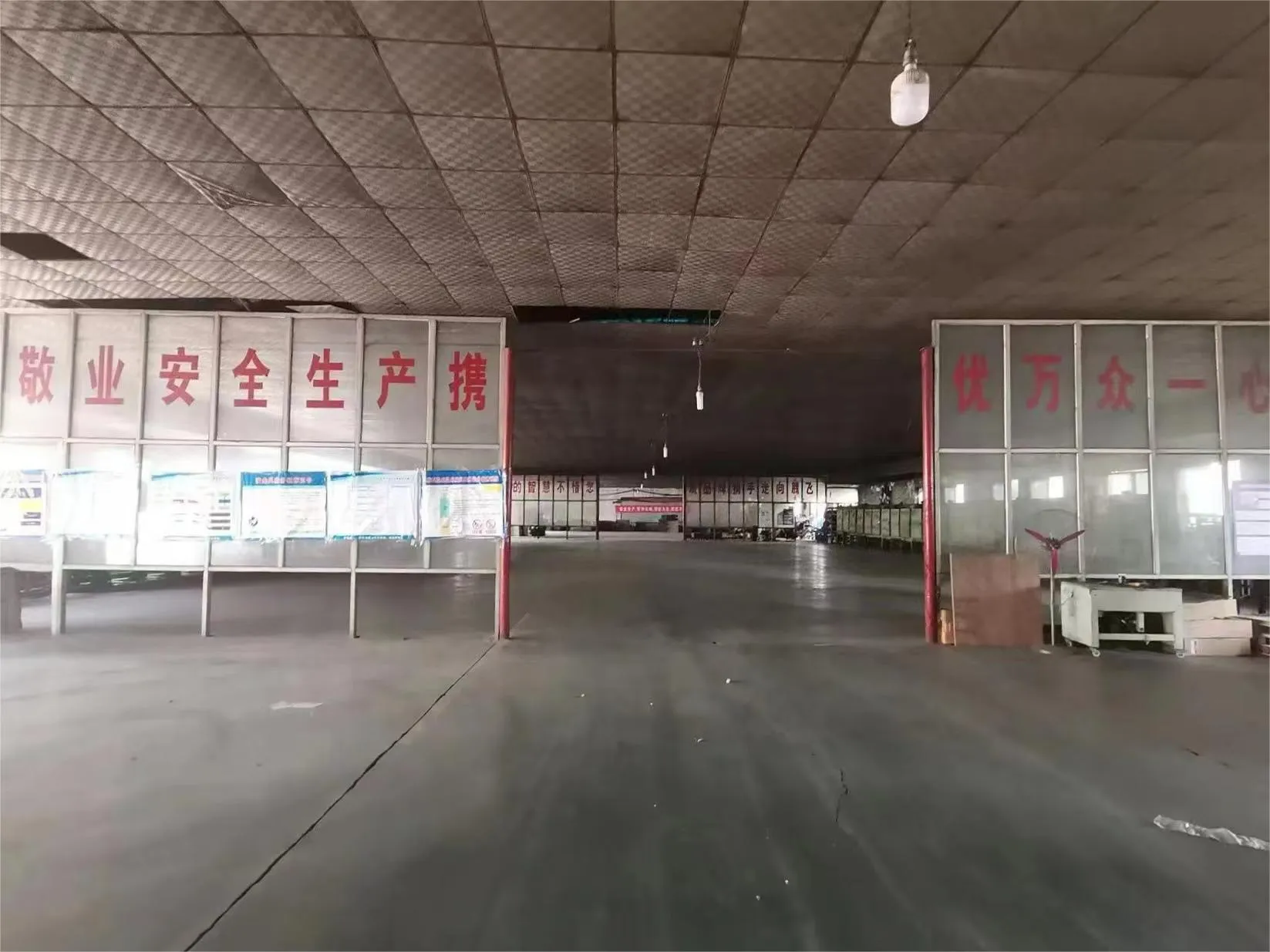
When it comes to expertise, understanding the different welding techniques that complement various rods is beneficial. Techniques such as Shielded Metal Arc Welding (SMAW), Gas Tungsten Arc Welding (GTAW), and Gas Metal Arc Welding (GMAW) each have specific applications depending on the welding rod in use. For instance, SMAW is widely suitable for a variety of rods and is often used in industrial applications because of its simplicity and effectiveness in different environments.
Proper preparation of the materials is another key component. Cleaning the rods and the metal surface to remove any contaminants like oil, rust, and dirt will ensure a stronger bond. Also, maintaining a suitable angle and distance between the rod and the surface during welding is essential to achieving a uniform, clean weld.
weld all rods
Safety cannot be overlooked when welding all rods. Use protective gear, including a welding helmet with an auto-darkening visor, gloves, and flame-resistant clothing to protect yourself from harmful UV and IR rays, as well as molten metal splatter. Ensure your workspace is well-ventilated to avoid inhaling fumes and gases produced during the welding process.
Another important aspect is the authoritative knowledge in troubleshooting common issues that may arise during welding. Problems like porosity, cracking, and incomplete fusion are common and can compromise the integrity of your welds. Understanding how to adjust your equipment settings and techniques in response to these issues reinforces trust in your craftsmanship.
For beginners seeking to develop their skills, engaging in training or certification courses can provide invaluable experience and improve your understanding of the complex interactions involved in welding different kinds of rods. This investment not only enhances your expertise but also establishes you as a credible professional in the field.
Lastly, the experience of continuous practice and learning cannot be understated. With each weld, observation and adaptation can refine your technique and build confidence in handling various situations. Collaborating with seasoned welders and participating in workshops can further enhance your skills, making you adept at approaching each job with authority and precision.
In conclusion, welding all rods proficiently necessitates a combination of the right knowledge, equipment, safety practices, and a commitment to ongoing learning. By adhering to these principles, you not only ensure the structural integrity of your projects but also establish trust and authority as a skilled welder in the industry.