The selection of welding rods plays a pivotal role in achieving high-quality welds, whether in industrial applications, art projects, or simple home repairs. While the plethora of options available may seem overwhelming, understanding the different types of welding rods and their specific uses can dramatically influence the success of a project. Expertise in this domain is not merely about knowing types but also their practical applications, supported by real-world experience.
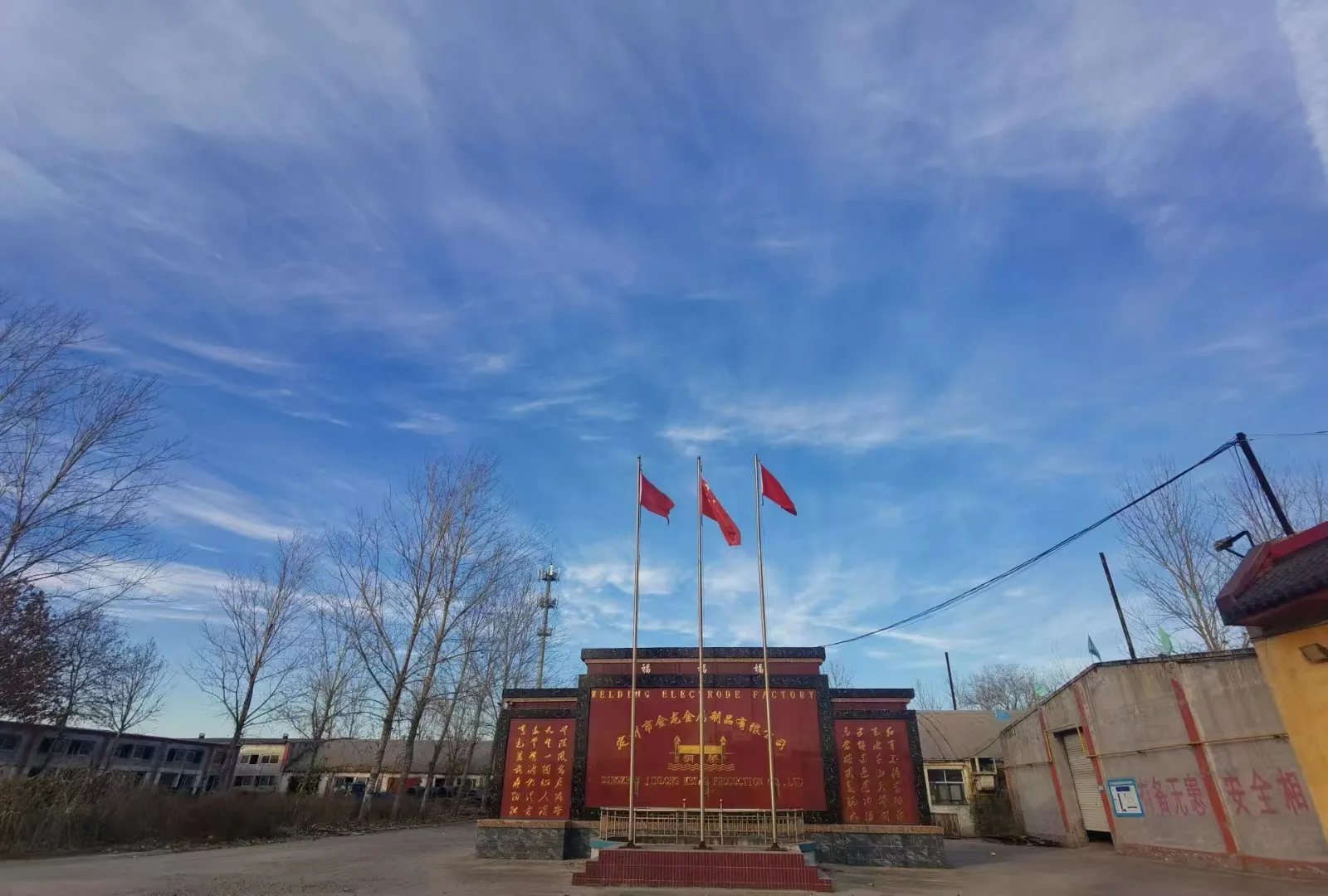
Welding rods, or electrodes, are divided into two main classifications consumable and non-consumable. Consumable electrodes melt and become part of the weld itself, whereas non-consumable electrodes do not. Each type serves distinct welding processes like Shielded Metal Arc Welding (SMAW), also known as stick welding, Gas Metal Arc Welding (GMAW), and Tungsten Inert Gas Welding (TIG), among others.
For consumable welding rods, one of the most common types is the E6010, favored for its ability to deeply penetrate with a forceful arc, making it ideal for welding through rust, paint, or dirt.
It is widely used in pipeline welding, particularly in vertical and overhead positions. Despite its robust capabilities, the E6010 requires a thorough understanding of its fast-freeze characteristics and demands a welder's expertise to manage its challenging arc control.
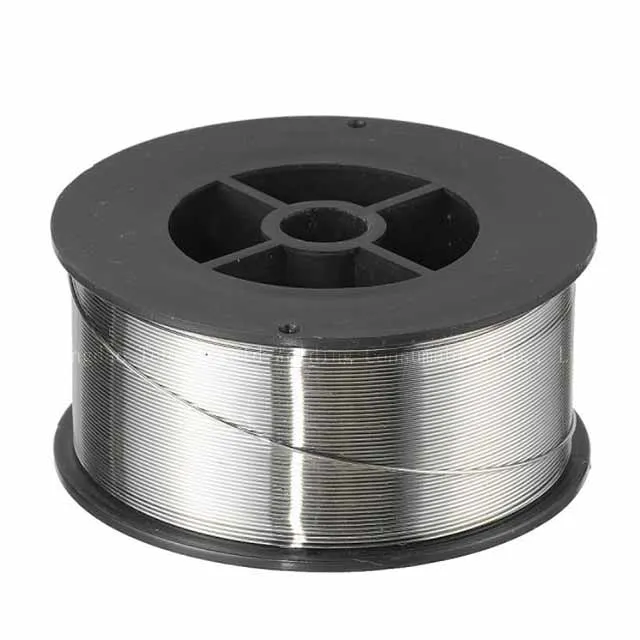
Conversely, the E7018 rod provides a different advantage with its iron powder coating, which offers a smooth, stable arc and produces clean welds with minimal spatter. Known for its versatility, the E7018 is suitable for welding various steels, providing strong welds in construction and shipbuilding industries. Yet, its effectiveness is contingent upon proper storage in a moisture-controlled environment to prevent hydrogen embrittlement, adding a layer of complexity to its use.
different welding rods
On the non-consumable front, tungsten rods are synonymous with TIG welding, valued for precision and control. Available in pure tungsten or alloyed forms like thoriated, ceriated, and lanthanated, each variant is tailored for specific applications and current types. The purity and quality of tungsten rods directly affect the stability of the arc and the integrity of the weld. Therefore, expertise in selecting the right tungsten rod can dramatically enhance both the efficiency and quality of the welding process, particularly in aerospace and automotive industries where exacting standards are non-negotiable.
Trustworthiness in handling welding rods is paramount due to the potential risks associated with faulty welds. Certification and adherence to industry standards ensure that materials meet expectations and perform safely under stress. Furthermore, authoritative guidance from seasoned professionals can significantly elevate the competency of both novice and experienced welders alike.
Ultimately, advancing one's expertise in different welding rods is not solely about understanding the technical specifications but also involves recognizing the role these rods play in the broader context of welding projects. With a trusted source of knowledge and real-world experience, craftsmen can achieve superior results, uphold safety, and enhance the longevity of their creations. This journey towards mastery assures that each weld is not only a connection of materials but a testament to precision and skill.