Stainless steel welding rods are essential for any welding project involving stainless steel, and choosing the right type can significantly impact the quality and durability of the weld. As an authority in metal fabrication and a trusted voice in welding expertise, this guide explores the various types of stainless steel welding rods, offering insights into their applications and advantages.
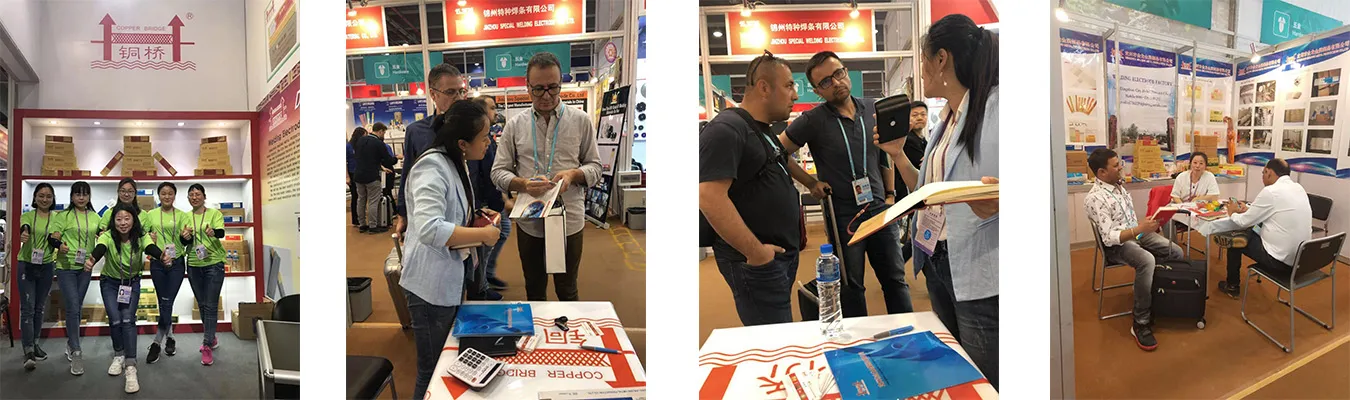
E308L-16 is one of the most commonly used stainless steel welding rods. It's designed for welding 304 and 304L stainless steels, ensuring excellent corrosion resistance and mechanical properties. Its low carbon content minimizes the risk of carbide precipitation, a crucial factor when welding stainless steel that will be exposed to corrosive environments. Welders often appreciate its arc stability and ease of use, which makes it suitable for a range of applications, including food and chemical equipment.
E309L-16 rods are preferred for welding dissimilar metals, such as stainless steel to mild steel. The higher chromium and nickel content in these rods provides good crack resistance and maintains strength even after repeated exposure to high temperatures. This versatility makes E309L-16 ideal for maintenance and repair work, as well as for transitional welds in construction and machinery where different metals are joined.
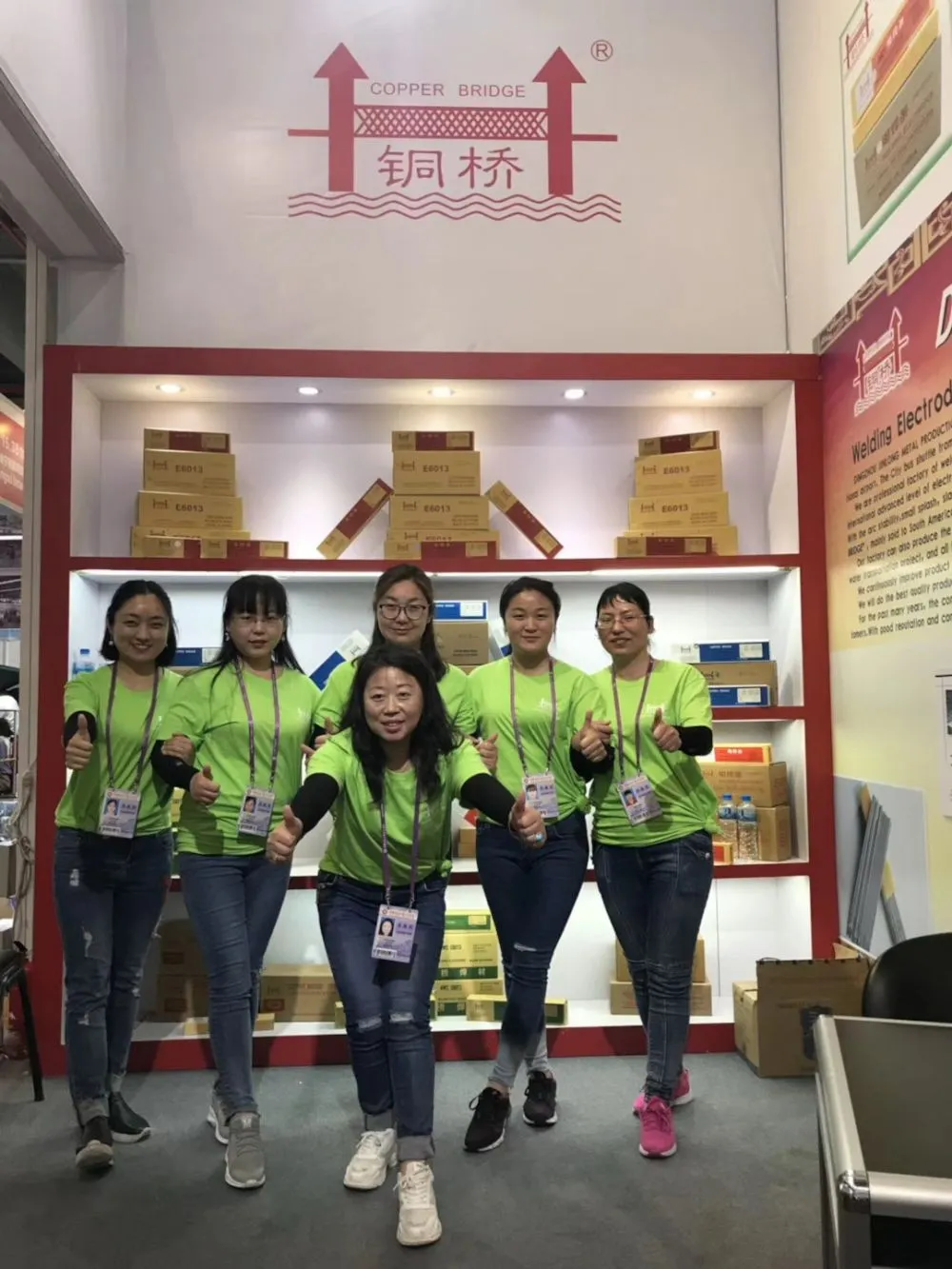
E316L-16 rods offer superior resistance to corrosion, especially in environments where chemical exposure is a concern, like in pharmaceutical and petrochemical facilities. These rods are optimal for welding 316 and 316L stainless steels, which contain molybdenum for added corrosion resistance. Welders dealing with projects that require exposure to chlorides often choose E316L-16 for its ability to maintain a resilient and stable weld over time.
E347 stainless steel welding rods are the go-to option when welding stainless steel that will operate at high temperatures. These rods are stabilized with niobium, which prevents carbide precipitation during welding. This feature is essential for maintaining the integrity of storage tanks, pressure vessels, and high-temperature pipelines, industries where temperature fluctuations are a constant challenge.
types of stainless steel welding rods
For welding projects where heat is a significant factor, E410 rods are often employed. This type is used for welding stainless steels that are subjected to high heat and require high strength and hardness, such as those found in turbine blades and other high-stress components. E410 offers the advantage of being air hardenable, making post-weld heat treatment possible to achieve desired mechanical properties.
When welding duplex stainless steels, E2209 rods provide the balanced properties of both austenitic and ferritic stainless steels. This balance offers excellent strength and corrosion resistance to chloride stress corrosion cracking, often required in marine, chemical, and oil and gas industries. Welders dealing with complex applications rely on E2209 for its enhanced durability and toughness.
Ultimately, the selection of a stainless steel welding rod involves understanding the specific requirements of the material and the environment in which the final product will be used. Welder expertise plays a crucial role in assessing these needs to ensure that the appropriate rod is used for each application. By understanding the characteristics and advantages of different stainless steel welding rods, one can achieve reliable and long-lasting welds that meet industry standards and withstand environmental challenges.
This comprehensive knowledge not only builds trust with clients and stakeholders but also exemplifies authority and expertise in the welding sector, contributing to enhanced project outcomes and extended service life of welded components.