When it comes to welding stainless steel, selecting the appropriate welding rod is crucial for achieving optimal results. This decision impacts not only the quality and durability of the weld but also affects the performance and aesthetics of the finished product. In the realm of stainless steel welding, there are several types of welding rods, each tailored to specific tasks and requirements. Understanding these types and their applications can significantly enhance the effectiveness of your welding projects.
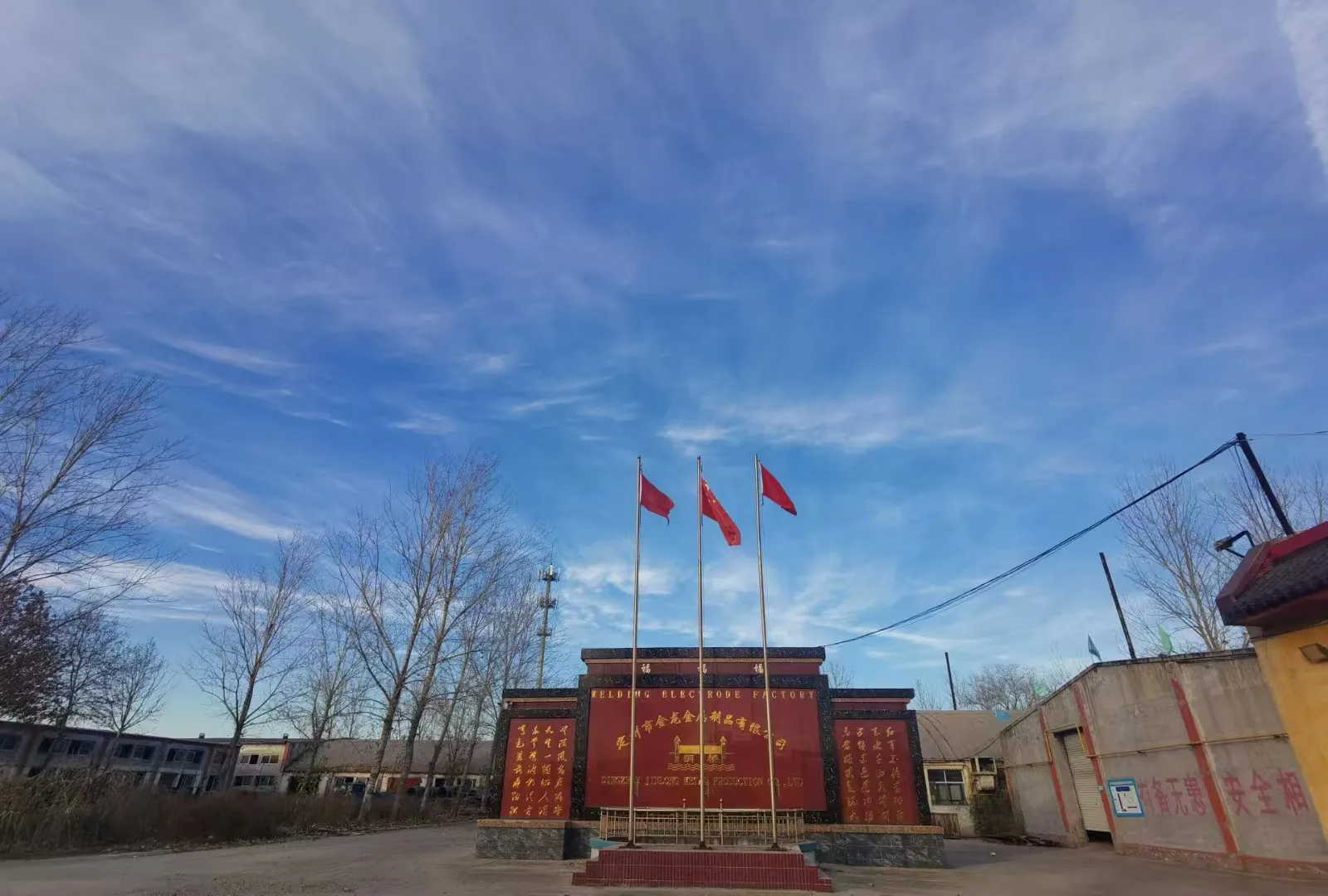
One of the most commonly used stainless steel welding rods is the E308L. This rod is particularly valued for its low carbon content, which minimizes the risk of carbide precipitation. Carbide precipitation is a phenomenon that can lead to corrosion and weaken the structural integrity of the weld. As a result, E308L rods are preferred for welding similar base metals, such as 304 and 347 stainless steel. They provide excellent resistance to intergranular corrosion and are ideal for applications where post-weld heat treatment is not feasible.
For tasks involving high-temperature exposure, the E309L welding rod is often the go-to choice. This rod is designed to weld dissimilar metals and is often used for welding austenitic stainless steel to carbon steel or for overlay applications. Its high chromium and nickel content provides superior heat resistance, making it suitable for applications such as furnace parts, heat exchangers, and kiln linings. The E309L's versatility and strength under temperature fluctuations make it a staple in industries where durability and reliability are paramount.
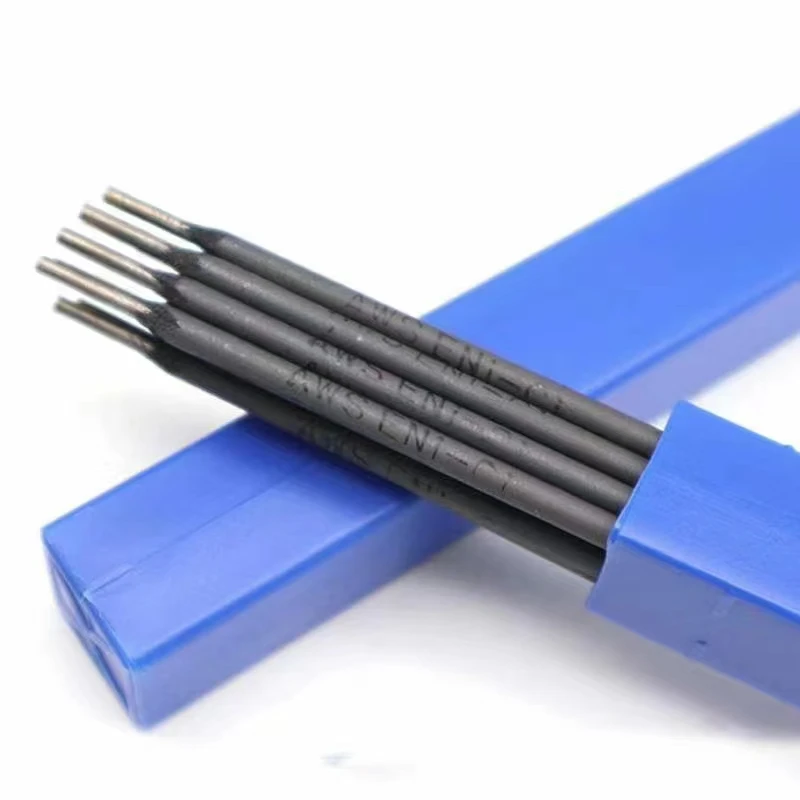
Another essential type is the E316L welding rod, known for its enhanced resistance to chlorides and acids. This makes it especially useful in industries where exposure to harsh chemicals is a concern, such as in chemical processing plants and marine environments. The added molybdenum content in E316L rods provides this additional resistance, helping prevent pitting and crevice corrosion. When welds need to maintain integrity under corrosive conditions, E316L is the preferred choice.
stainless steel welding rod types
For fabrication purposes, especially when aesthetics are as important as functionality, the E347 welding rod offers an excellent solution. This rod incorporates a small amount of niobium (columbium), which stabilizes the weld area and reduces carbide precipitation. The E347 rod is often utilized in applications where the weld zone must endure elevated temperatures, such as in the construction of exhaust systems and aerospace components. Its ability to create a smooth, clean weld appearance makes it ideal for projects where visual presentation is key.
While these are some of the primary types of stainless steel welding rods available, choosing the right one involves considering several factors. Firstly, assess the base materials involved in your project, as this will often dictate the type of rod needed to ensure compatibility and performance. Secondly, consider the environmental conditions the weld will be exposed to, such as temperature extremes or corrosive elements. Finally, factor in any industry-specific standards or regulations that may influence your choice of welding rod.
In conclusion, understanding the nuances of different stainless steel welding rod types is critical to the success of welding projects. Each rod offers unique properties, tailored to specific applications, ensuring that welds are strong, durable, and resistant to environmental challenges. By selecting the right welding rod, professionals can ensure their work is not only efficient and effective but also of the highest quality, meeting the stringent demands of modern industries. With careful consideration and application of expertise, the right choice can make a significant impact on the longevity and performance of welded structures.