TIG welding, or Tungsten Inert Gas welding, is a process that has transformed the construction and manufacturing sector, especially when dealing with stainless steel. As a seasoned SEO specialist deeply familiar with the welding industry, let's explore the distinct advantages and technicalities of using TIG welding for stainless steel projects, which could elevate both product quality and business authority.
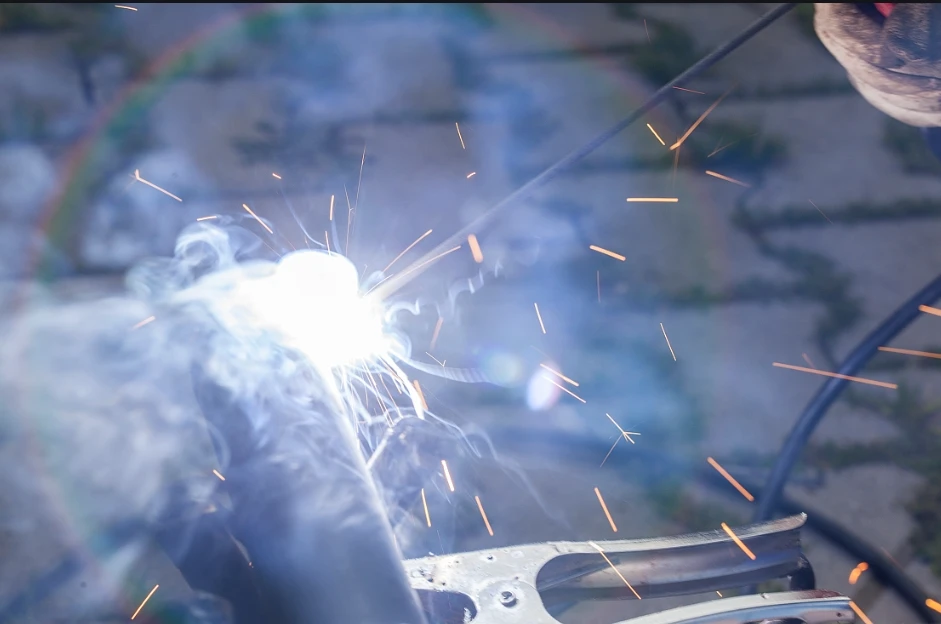
Stainless steel, with its high resistance to corrosion and stunning visual appearance, is the material of choice for numerous industries, including aerospace, automotive, and medical fields. However, welding stainless steel is no simple task—it requires precision and expertise to maintain its integrity and characteristics. TIG welding, an arc welding process that utilizes a non-consumable tungsten electrode to deliver the weld, stands out for its superior and meticulous results.
Experience is a crucial component when deciding on TIG welding for stainless steel. This process offers unmatched control, allowing welders to handle the heat precisely. When welding stainless steel, maintaining a constant, low heat is imperative to prevent the metal from becoming brittle or distorted. With TIG welding, the welder operates with a foot or hand control, carefully adjusting the heat input and ensuring that the stainless steel does not overheat, preserving its physical properties and aesthetic appeal.
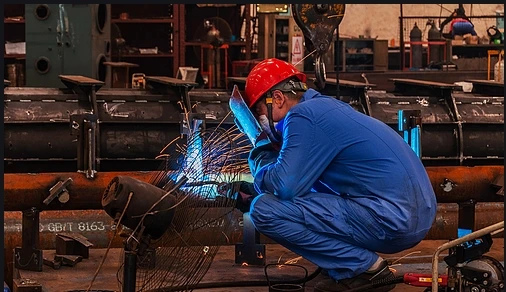
From an expertise perspective, TIG welding is incredibly versatile and can handle various thicknesses and types of stainless steel. Given its ability to produce cleaner and more refined welds compared to other welding methods, it's widely used for creating products that require high-quality visual and structural results, such as in surgical instruments or architectural components. Expertise in TIG welding involves understanding the nuances of welding rod selection, shielding gas applications (typically argon or a mixture of argon and helium), and the fine adjustments needed for welding different stainless steel grades, which can enhance the efficiency and quality of the welding process.
tig stainless steel
The authoritative nature of TIG welding in the stainless steel domain is further underscored by its application in high-stakes industries. Automotive manufacturers employ TIG welding for critical components where weld integrity and durability are non-negotiable. In the aerospace sector, where reliability and safety are paramount, TIG welding is repeatedly chosen for its precision and strength. These industry endorsements amplify the authoritative perception of TIG welding, cementing its status as a preferred welding technique for stainless steel.
Trustworthiness in welding processes, especially with valuable materials like stainless steel, is imperative. TIG welding is lauded for its clean finish; the process does not produce slag and minimizes spatter, reducing the need for post-weld cleanup and increasing productivity. Furthermore, the ability to create a strong and durable weld without additional filler metal enhances the reliability of the welded product. Businesses relying on TIG welded stainless steel products can trust the results for their longevity and minimal maintenance, significantly boosting customer satisfaction and brand reputation.
In conclusion, the heightened control and potential for precision make TIG welding the apex choice for stainless steel fabrications. Companies that master this technique often find themselves revered in circles that value high-quality, aesthetically pleasing, and structurally sound stainless steel products. By integrating TIG welding into their fabrication processes, businesses can elevate their market standing, ensuring that their products not only meet but exceed industry standards. Maintaining expertise in TIG welding guarantees that enterprises remain competitive and authoritative, ensuring that they deliver trustworthy and unparalleled stainless steel solutions to their customers.