In the world of welding, the E7018 electrode stands as a pillar of reliability and strength. Widely used across industries, its tensile strength is crucial for ensuring secure and lasting welds.
Let's delve deeper into what makes the tensile strength of an E7018 electrode a preferred choice for professionals seeking durability and performance.
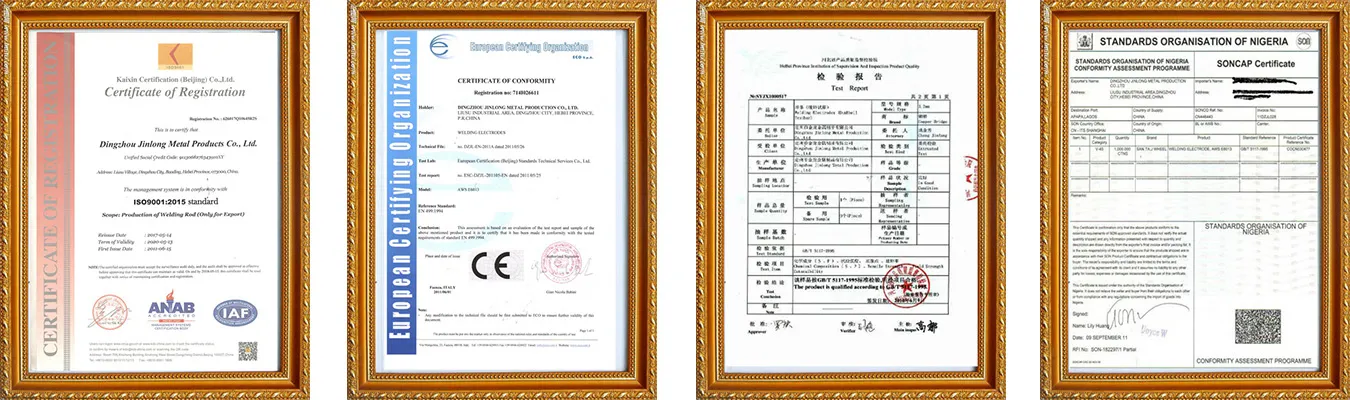
First, it's essential to understand what tensile strength means in the context of welding. Tensile strength refers to the maximum amount of tensile stress that a material can withstand before failure. For welding electrodes like the E7018, this translates to the ability of the weld to resist breaking under tension. The E7018 electrode boasts a tensile strength of approximately 70,000 pounds per square inch (psi), making it an ideal candidate for projects demanding robustness and longevity.
The composition of the E7018 electrode is one of the critical factors contributing to its high tensile strength. Comprising primarily of low-hydrogen iron powder, the electrode is crafted to minimize hydrogen embrittlement—a common cause of weld failure. This low-hydrogen nature prevents cracks and ensures that the weld remains intact under substantial stress, a characteristic highly valued in structural welding applications like buildings, bridges, and pressure vessels.
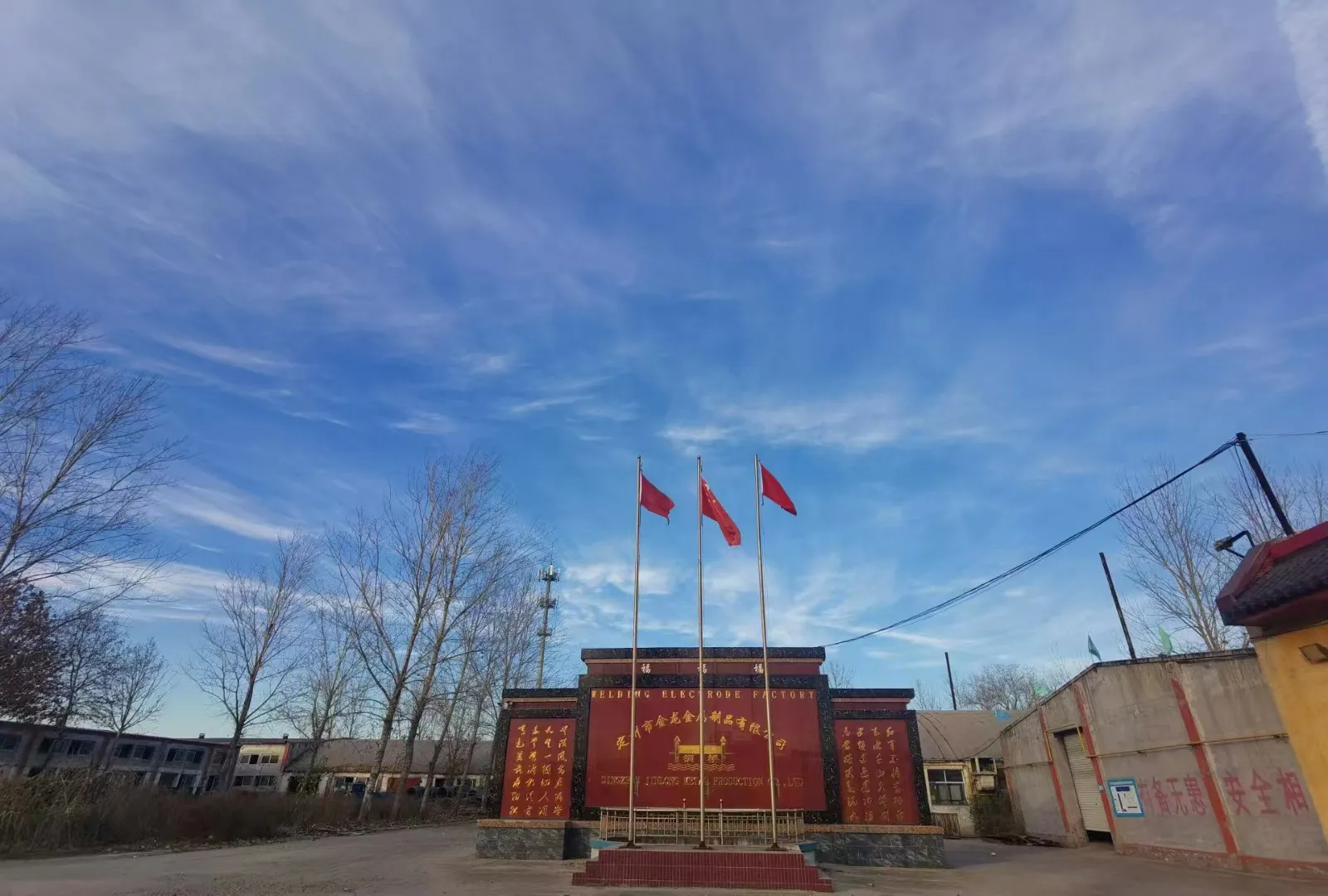
Experience has shown that the E7018 is particularly favored for its versatility and ease of use. Its design allows it to produce a clean, strong weld even in out-of-position jobs, which can be more challenging with other types of electrodes. Welders with firsthand experience consistently tout the E7018 as forgiving and adaptable, making it suitable even for less-than-ideal conditions—such as damp environments—without sacrificing the integrity of the weld.
the tensile strength of a e7018 electrode
For those in industries that require adherence to rigorous standards, the expertise surrounding the E7018 electrode becomes even more critical. Understanding the appropriate techniques for utilizing this electrode plays a significant role in maximizing its tensile strength benefits. Experts advocate for a clean workpiece and proper electrode storage to avert moisture absorption, which can lead to hydrogen-induced cracking. Additionally, maintaining the correct arc length and employing proper welding techniques ensures the electrode’s full potential is realized.
Authoritativeness in the world of welding comes from both individual skill and adherence to established industry standards. The E7018 electrode is often specified in engineering plans due to its dependable tensile strength and consistency. Its widespread acceptance in industry codes and welding certifications speaks volumes about the trust professionals place in its capabilities. Welding instructors regularly emphasize the E7018 in educational settings, marking it as a benchmark for assessing welding proficiency.
To conclude, the trustworthiness of the E7018 electrode is well-supported by both scientific and anecdotal evidence. Its high tensile strength, coupled with a composition that curtails hydrogen-induced failures, makes it an optimal choice for critical welding tasks. As one gains hands-on experience and a deeper understanding of this electrode, it becomes clear why it is held in such high regard among seasoned welders and industry authorities alike.
While the tensile strength of an E7018 electrode is a defining characteristic, its broader value lies in the combination of performance, reliability, and adaptability it offers. This makes it an invaluable asset in any welding toolkit, delivering results that withstand the test of time and stress.