Tensile strength is a critical factor in evaluating the performance of welding electrodes, especially when it comes to the E7018 electrode, which is widely known for its performance across various applications. Understanding the nuances of this specification helps in ensuring optimal outcomes in construction, repair, and manufacturing tasks.
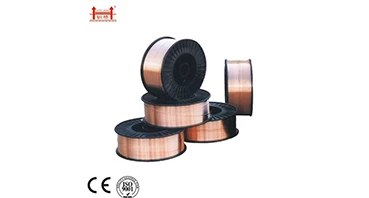
E7018 electrodes are low-hydrogen electrodes made primarily of carbon steel. These electrodes are designed to deposit weld metal that exhibits excellent mechanical properties, including high tensile strength, good ductility, and crack resistance.
Based on industry standards, the 70 in E7018 represents the minimum tensile strength of welds made with this electrode, which translates to 70,000 psi (pounds per square inch). This level of tensile strength plays a pivotal role in the structural integrity of welded assemblies. It ensures that the welded connections can withstand significant amounts of tensile stress without failure, thereby safeguarding against catastrophic structural issues.
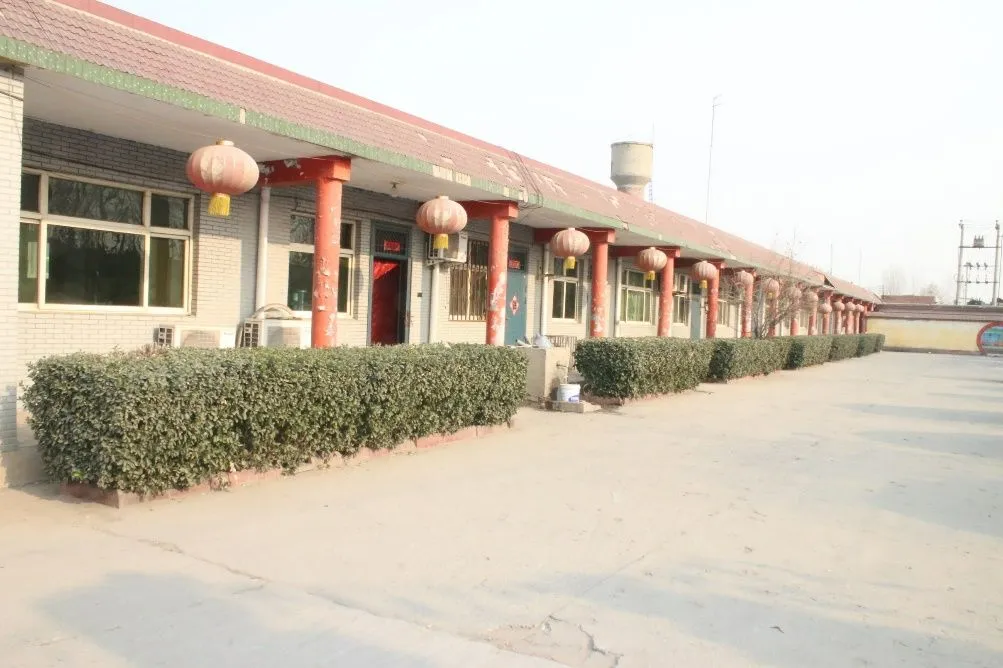
A critical insight comes from field evaluations where welders have applied E7018 electrodes extensively. Experienced professionals note that one of the superior qualities of E7018 is its performance in vertical and overhead welding situations. Its ability to maintain tensile strength in challenging positions is a testament to its versatile nature. Additionally, welds created with this electrode display a smooth bead appearance, which is not just aesthetically pleasing but indicates a sound structural bond.
Professional welders appreciate the balancing act E7018 performs between high tensile strength and operational flexibility. It handles the moderate presence of contaminants and rust on metal surfaces better than many other electrodes. This adaptability makes it an ideal choice for outdoor and repair work where surface cleanliness cannot always be controlled to perfect standards.
Testing and research-backed investigations into the E7018 electrode's performance show that maintaining its superior tensile strength involves adhering to strict moisture control. Due to its low-hydrogen nature, moisture can compromise the electrode's integrity, leading to hydrogen-induced cracks upon cooling of the weld metal. Pre-heating the base material and maintaining electrode storage at the recommended temperatures are key practices emphasized by experts within the industry to preserve electrode performance.
tensile strength of e7018 electrode
Moreover, E7018’s tensile strength can be attributed to its coating, which is composed of iron powder and low hydrogen potassium. The coating plays a significant role not only in maintaining arc stability but also in shielding the molten weld pool from atmospheric contamination, thereby maintaining the desired mechanical properties of welded joints.
In the realm of product safety and standards, E7018 electrodes are often scrutinized to meet industry regulations and customer requirements. Ensuring the tensile strength adheres to minimum specifications is part of compliance with standards such as the American Welding Society (AWS) and American Society for Testing and Materials (ASTM). Manufactures invest heavily in R&D and mechanical testing to certify each batch meets or exceeds specified tensile strength before reaching consumers.
Trustworthiness in electrode performance is paramount for establishing credibility with stakeholders, whether they be construction engineers, quality inspectors, or fabrication managers. Demonstrations through onsite tests, webinars, and technical seminars serve as effective tools in highlighting the tensile strength properties and overall benefits of E7018 electrodes, fostering a deeper trust relationship with end-users.
In closing, those invested in achieving the highest standards of weld quality and reliability recognize the E7018 electrode not merely as a tool, but as a component driven by expert engineering and seasoned user experiences. Consistent application of best practices, understanding product limitations, and keeping abreast with emerging technologies all contribute to enhancing the utility and perceived value of E7018 within professional and industrial settings.
Thus, for businesses and individual practitioners keen on optimal welding outcomes, leveraging E7018's tensile strength is not just a consideration, it's a cornerstone for building sturdy and enduring metallurgical bonds.