The art of welding involves a delicate balance of skill, material knowledge, and the right equipment. One common challenge many welders face is the need to join stainless steel to mild steel—a task that requires careful consideration of the welding rod used to ensure strength and durability in the finished product.

Selecting the appropriate welding rod is crucial in achieving a successful weld between stainless steel and mild steel. The dissimilarity in the two metals' properties, such as their melting points and thermal expansion rates, can complicate the bonding process. Therefore,
it's essential to use a welding rod designed to accommodate these differences.
An expert welder understands that a high-nickel content welding rod, such as an ERNiCr-3, is often recommended for this type of welding. This rod is advantageous due to its ability to handle the expansion and contraction differences between stainless and mild steel during the heating and cooling phases of welding.
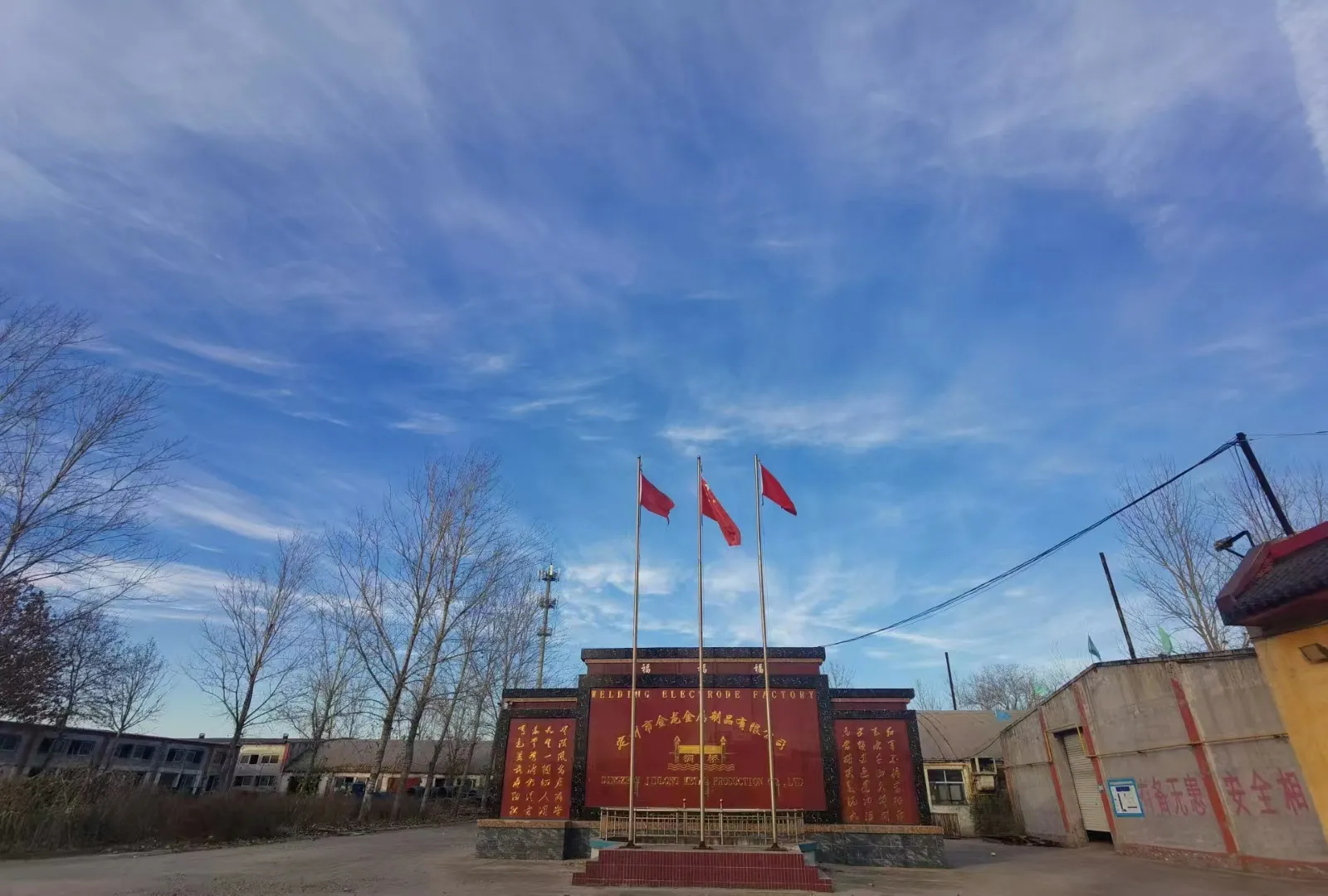
The experience of seasoned welders suggests that preparation is key. Grinding the surfaces of both the stainless and mild steel can eliminate contaminants, such as oxidation or mill scale, ensuring a clean welding area. A carefully cleaned metal surface allows for optimal penetration and meld of the welding rod into the base metals, forming a sturdy joint.
Safety cannot be understated in the welding process, particularly when dealing with dissimilar metals. Diligent use of personal protective equipment (PPE), including gloves and appropriate eye protection, forms an integral part of every welding project. Furthermore, using a stable workbench with proper ventilation mitigates the risk of inhaling potentially harmful fumes emitted during the welding process.
stainless to mild steel welding rod
Mastery over heat management is another hallmark of a proficient welder when fusing stainless to mild steel. Maintaining a consistent heat input prevents warping while ensuring complete fusion without excessive burn-through, especially in thinner sections of the material. Expert welders often recommend stitching techniques or intermittent welding to manage heat distribution effectively.
Documentation from authoritative welding institutions often highlights the mechanical properties of the finished weld as a combination of the parent metals and filler metals. The resultant weld should exhibit sufficient ductility and tensile strength to withstand the intended application's operational demands. As a welder looking to enhance trustworthiness and professionalism, it’s prudent to conduct weld testing, such as bend or tensile tests, to certify the integrity of your work.
In the context of yield and thoroughness, examining the weld’s aesthetic is equally important. A proficiently welded joint should display an even, consistent bead with an absence of visible porosity or inclusions. This emphasis on quality demonstrates an unwavering commitment to excellence, fostering credibility among peers and clients alike.
Finally, the choice of welding technique, whether shielded metal arc welding (SMAW) or gas tungsten arc welding (GTAW), can influence the outcome significantly. Scholars and industry veterans often suggest that while SMAW provides flexibility and ease of use, GTAW might be advantageous for more precision-oriented projects requiring cleaner welds.
In conclusion, the confluence of precise equipment, preparation expertise, and exceptional skill brings about the successful welding of stainless steel to mild steel. For those in search of a high-performing weld, leveraging industry insights and adhering to best practices ensures credibility and unmatched quality in every project undertaken.