Selecting the appropriate stainless steel TIG rod is essential for ensuring long-lasting and structurally sound welding joints. With numerous options available, understanding the details of the stainless steel TIG rod chart is crucial for making informed choices. Stainless steel welding with TIG (Tungsten Inert Gas) technique offers precision and control, but the key lies in selecting the right filler rod according to the material specifications and project requirements.
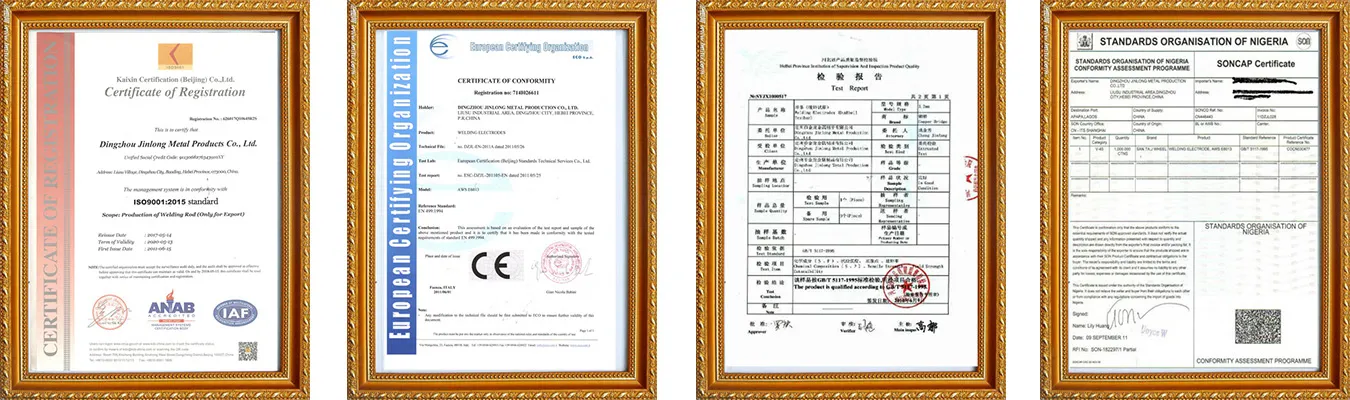
Stainless steel TIG rods are known for their versatility, being used across various industries such as automotive, aerospace, and construction where corrosion resistance and strength are paramount. A reliable TIG rod chart offers insights into which rod to choose for different stainless steel grades, taking into consideration factors such as tensile strength, corrosion resistance, and weldability.
Commonly used stainless steel TIG rods include ER308, ER308L, ER309, ER316, and ER316L. Each of these rods has distinct properties
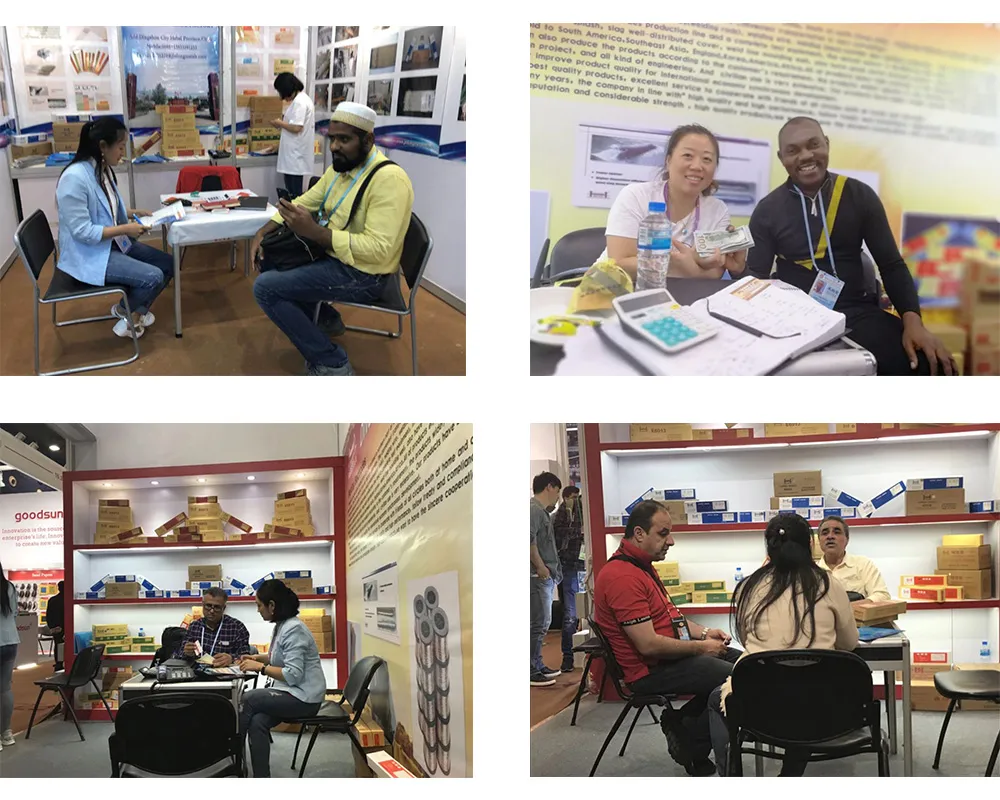
1. ER308 and ER308L These are among the most popular TIG rods for 304 stainless steel. ER308 is suitable for welding similar base metals, while ER308L, with its lower carbon content, is designed to provide better resistance to intergranular corrosion. This makes it highly suitable for applications where the weld is exposed to corrosive environments.
2. ER309 This rod is often used when welding dissimilar metals, such as joining stainless steel to mild steel. Known for its high resistance to thermal expansion, ER309 is ideal for high-heat applications, ensuring strong joints with excellent corrosion resistance.
3. ER316 and ER316L Used for 316 and 316L stainless steel grades, these rods offer superior performance in marine environments due to their resistance to chloride corrosion. ER316L has a lower carbon content, which enhances its resistance to intergranular corrosion, making it the preferred choice for more sensitive applications.
stainless steel tig rod chart
Expertise in using these TIG rods effectively comes from understanding their melting points, tensile strengths, and applications. This knowledge aids in achieving optimal weld chromaticity and preventing common issues such as cracking and warping. Professional welders appreciate these details, as utilizing the right rod ensures efficiency and reliability, ultimately driving project success.
When consulting a stainless steel TIG rod chart, it is paramount to consider the compatibility with the base metal, allowed heat input, and desired mechanical properties of the weld. Charts typically list rod diameters alongside expected welding positions—flat, horizontal, vertical, or overhead—providing welders with guidance to tailor their techniques accordingly.
For those engaging in high-specification projects, such as those in petrochemical plants or high-pressure vessels, attention to metallurgy and precise rod selection is crucial. Here, the choice of rod also influences the post-weld treatment required to maintain integrity and compliance with stringent standards.
Experienced welders recognize the importance of a reliable supplier who can provide consistent quality in TIG rods, ensuring that their projects meet both industry standards and client expectations. Trustworthiness in material composition, batch consistency, and availability of technical support are factors that elevate a supplier's status within the field.
In essence, a comprehensive understanding of the stainless steel TIG rod chart transforms basic welding tasks into refined craftsmanship. It empowers welders to produce joints that are not only functional but also aesthetically pleasing, embodying a seamless integration of form and function. This mastery is what sets apart skilled professionals in an industry where precision and quality are non-negotiable.