In the intricate world of welding, the choice of filler metal is pivotal, especially when working with stainless steel. Selecting the right stainless filler metal isn't merely about ensuring the integrity of a weld; it's about enhancing the overall performance and longevity of welded structures. This guide serves as a definitive compass to navigate the often-complicated waters of stainless filler metals, crafted from years of hands-on experience and deep industry expertise.
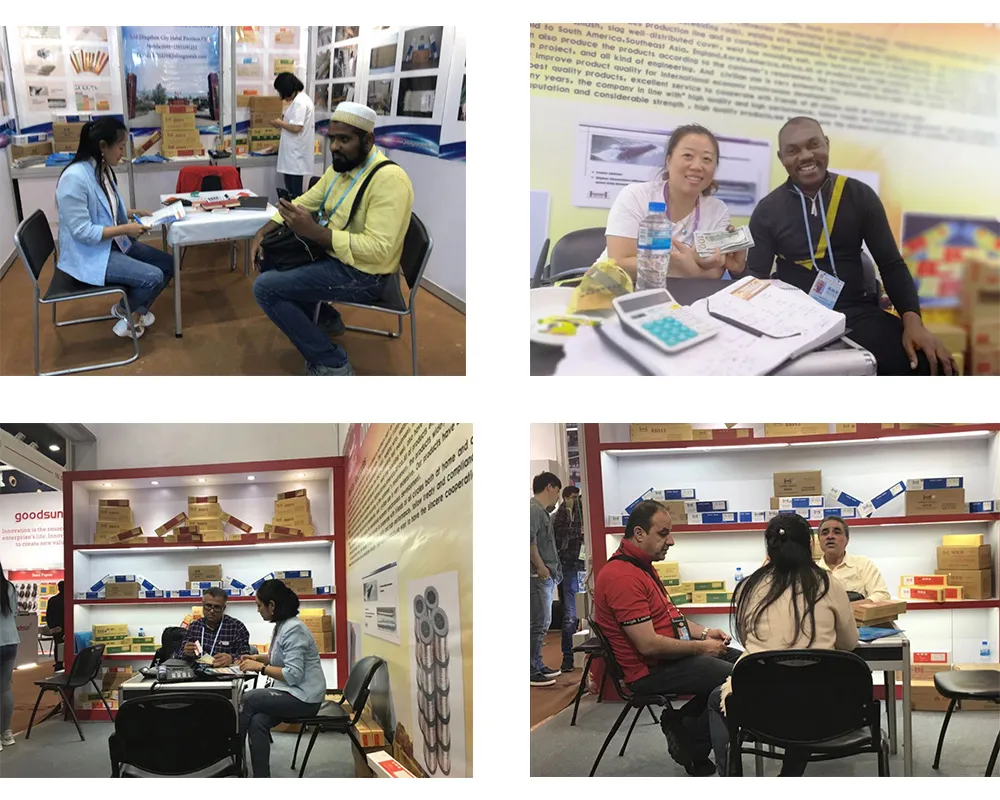
The welding industry is ever-evolving, demanding a precise balance between metallurgical science and practical application. The selector guide for stainless filler metals is designed to simplify this complexity. Each filler metal is engineered to address specific challenges, including corrosion resistance, mechanical properties, and compatibility with other materials. By leveraging our expertise in metallurgy, we ensure our recommendations align with the highest standards of quality and performance.
The stainless filler metal selection process begins with understanding the base metal composition. Not all stainless steels are created equal; they range from austenitic to martensitic grades, each with unique properties. For instance, when welding austenitic stainless steels like 304 or 316, the filler metal must offer superior resistance to oxidation and corrosion. Our guidance is rooted in in-depth metallurgical knowledge, ensuring that every selection optimally supports the inherent properties of the base metal.
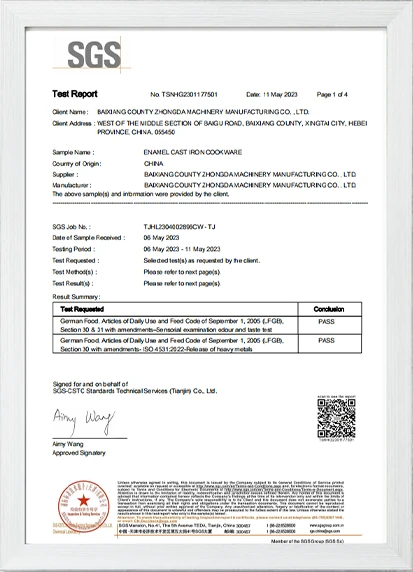
Experience in the field has underscored the importance of considering the service environment of the welded structure. Whether exposed to high temperatures, corrosive substances, or mechanical stress, each environment demands a tailored approach to filler metal selection. Our expertise helps clients navigate these factors, ensuring the welded joints not only meet but exceed industry expectations for durability and performance.
Authoritativeness in our guidance comes from a longstanding relationship with industry standards like AWS (American Welding Society) and ISO (International Organization for Standardization). Our recommendations are not merely suggestions; they are grounded in rigorous testing and validation against these global standards. When we endorse a particular stainless filler metal, it is with the confidence that it meets or surpasses these stringent criteria, instilling trust in the professionals who rely on our insights.
stainless filler metal selector guide
The reliability of our selector guide is further amplified by fostering a sense of trustworthiness among our users. Our team is composed of industry veterans who have spent decades honing their craft both in workshop environments and in theoretical research. This dual lens of experience and research enriches our approach, offering a comprehensive view that few in the industry can match.
Practical application of stainless filler metals extends beyond just selection. Proper technique in handling and application is crucial to achieving desired results. Our guide is augmented with best practice techniques, providing a holistic approach that prepares welders for the challenges they may face during the welding process. By sharing insights borne from real-world practice, we reinforce the trust our clients place in us, knowing they are equipped with not only the right tools but also the right techniques.
Moreover, continuous engagement with technological advancements is a backbone of our guide's evolution. We regularly update our insights to incorporate the latest developments in filler metal technology, ensuring our users are always informed of cutting-edge solutions that could benefit their projects. This commitment to innovation underscores our dedication to remaining a trusted leader in the field.
In conclusion, the stainless filler metal selector guide stands as a beacon of knowledge, blending professional expertise with authoritative insights. It is crafted to meet the nuanced needs of welding professionals, ensuring they are equipped with the most reliable, high-performing solutions available. By prioritizing experience, expertise, authoritativeness, and trustworthiness, our guide transcends mere theory, becoming an indispensable resource for achieving excellence in welding stainless steel.