Stainless steel to stainless steel (ss to ss) welding rods are a critical component in the fabrication and repair of stainless steel structures. The growing demand for stainless steel in various industries necessitates a deep understanding of the welding products used in its assembly. This article delves into the unique attributes of ss to ss welding rods, essential for professionals in fields ranging from construction to automotive manufacturing.
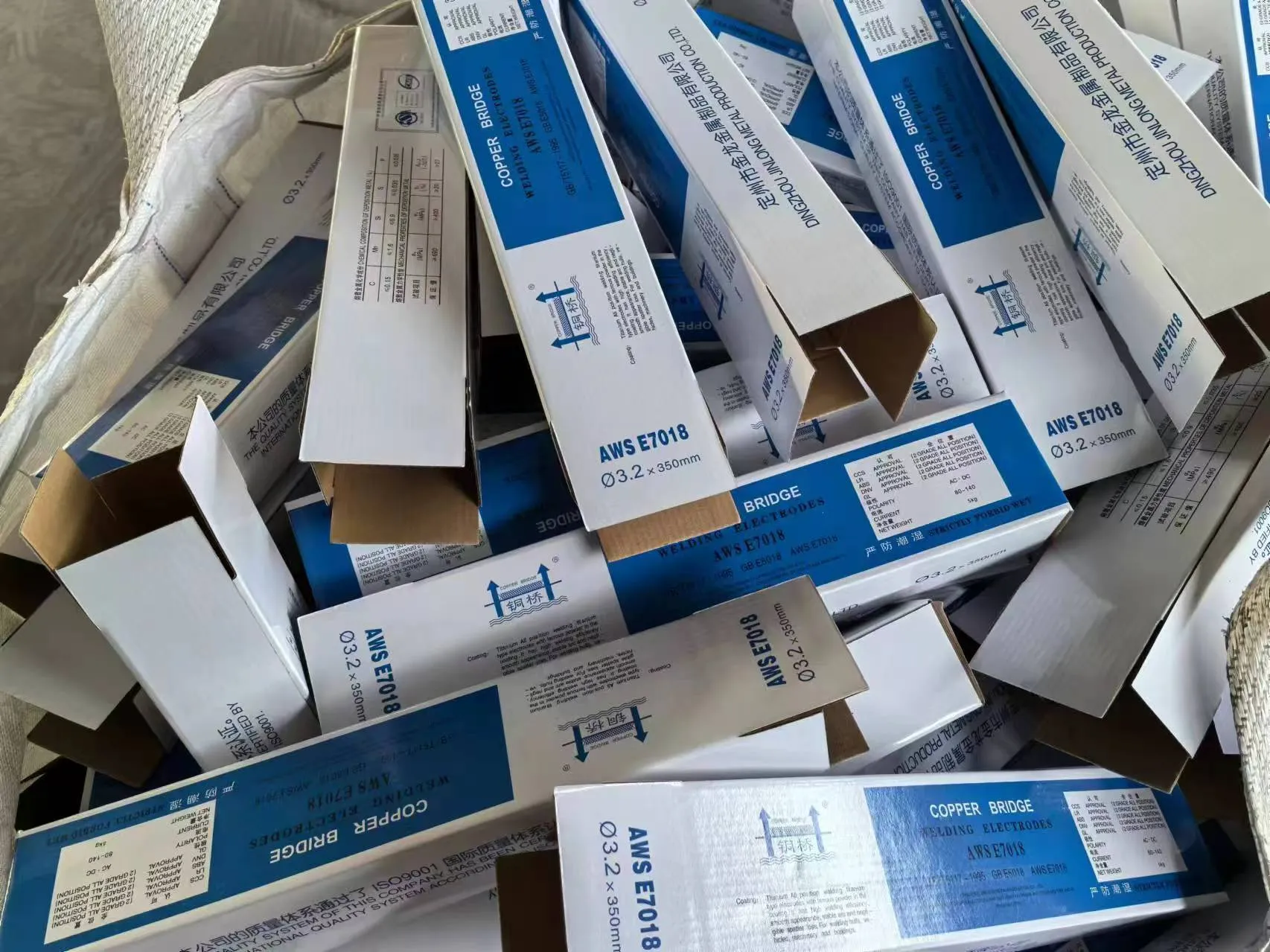
Stainless steel welding rods, typically composed of various alloys, are engineered to meet specific performance standards in terms of strength, corrosion resistance, and thermal conductivity. The choice of a welding rod can significantly impact the durability and safety of the welded component. Welding professionals understand that not all rods are created equal and that selecting the right type requires a nuanced understanding of the material properties of the stainless steel in question.
One of the most notable qualities of stainless steel is its corrosion resistance, primarily due to the presence of chromium, which forms a passive layer on the surface that prevents oxidation. When welding stainless steel, it's vital to use rods that maintain this layer's integrity to prevent future corrosion-induced failures. Therefore, the welding rods designed for ss to ss applications are enriched with elements like chromium, nickel, and molybdenum, which contribute to enhanced corrosion resistance.
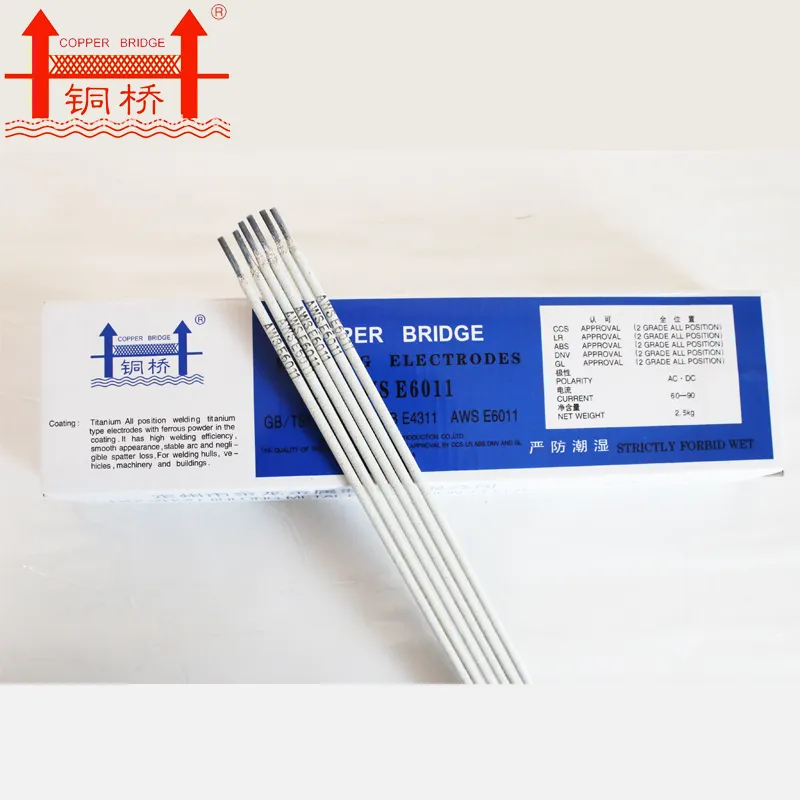
Another critical aspect of ss to ss welding rods is their capacity to operate effectively at high temperature cycles, which is crucial in industries such as aerospace and automotive where thermal stress is a regular occurrence. The careful balance of elements in these rods ensures that they maintain their structural integrity even when subjected to extreme temperature variations.
The welding technique employed also plays a crucial role in the success of the task. Depending on the application, whether it's MIG, TIG,
or stick welding, the choice of rod will vary. TIG welding, for instance, is often the preferred method for thinner gauges of stainless steel since it provides better control and cleaner weld seams. The precision offered by TIG welding is crucial in high-stakes industries, where joint failure is not an option.
ss to ss welding rod
In practical terms, professionals often rely on stainless steel welding rods such as ER308L, ER316L, and ER309L, among others. ER308L is commonly used for welding similar grades of stainless steel, ensuring a low carbon content to prevent carbide precipitation. ER316L is preferred for its superior chloride corrosion resistance, making it suitable for marine environments. ER309L, meanwhile, is typically used when joining dissimilar metals, providing stability across varying expansion rates.
The manufacturing process of ss to ss welding rods is another critical aspect contributing to their effectiveness. High-quality rods are manufactured under stringent controls to ensure consistency in size and chemical composition. This consistency is paramount, as even minor deviations can affect the welding outcome, leading to weak joints or increased corrosion susceptibility.
As professionals in the welding industry recognize, the marketplace is awash with products that claim superior performance. However, ensuring the procurement of high-quality ss to ss welding rods involves due diligence, including reviewing certifications and, where possible, undertaking trials to assess compatibility with specific welding projects. Leading manufacturers often subject their products to rigorous quality assurance protocols, which serve as a testament to their reliability and performance.
In conclusion, ss to ss welding rods are an indispensable resource in crafting durable and resilient stainless steel structures. The expertise in selecting, handling, and applying these rods can significantly influence the lifecycle and safety of the final product. Professionals need to remain informed and vigilant, embracing technological advancements and material innovations that enhance welding efficacy. Through a detailed understanding of their properties, and pragmatic approaches to their application, industries can unlock the full potential of stainless steel, ensuring the longevity and safety of their projects.