In the ever-evolving world of welding technology, choosing the right welding rod can significantly impact the durability and quality of a weld. Among the various types of welding rods available, the transition from stainless steel (SS) to carbon steel (CS) welding rods often raises pertinent questions among professionals. Understanding this transition requires a deep dive into the mechanics and metallurgical aspects of welding. Here’s a comprehensive exploration, blending experience, expertise, and authoritative guidance to illuminate the intricacies involved in using SS to CS welding rods.
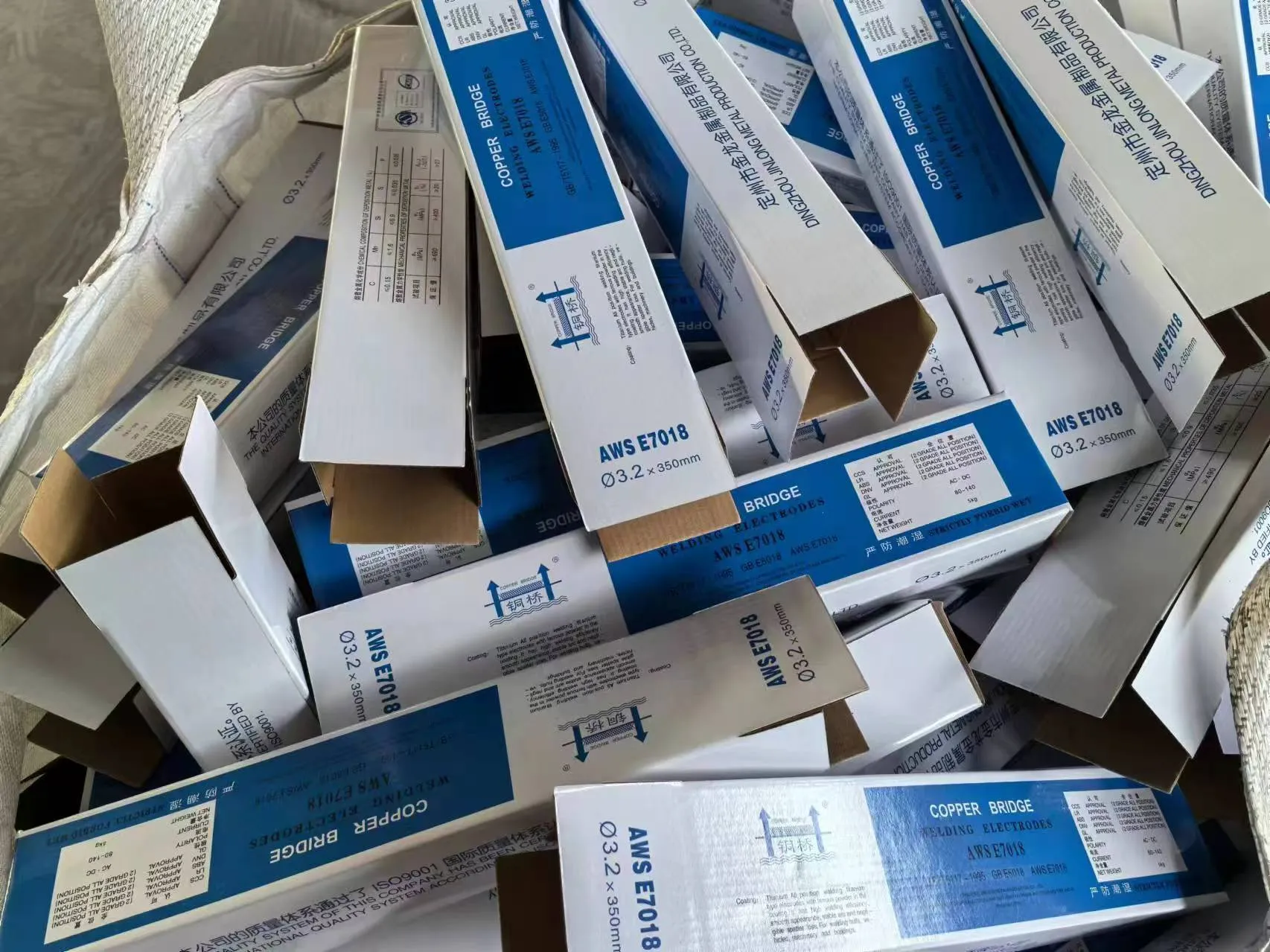
Stainless steel to carbon steel welding is a process that necessitates precision and an understanding of differing material properties. Stainless steel, prized for its corrosion resistance, owes this characteristic to its chromium content. On the other hand,
carbon steel is well-regarded for its strength and flexibility. When welding these two materials, the selection of an appropriate welding rod is crucial in bridging the gap between these distinct properties.
A professional wielding considerable experience would highlight that the first step in this process is to decide on a rod that can withstand the temperature and stress differentials between stainless steel and carbon steel. Welding experts often opt for austenitic stainless steel rods such as 309L. This type of rod provides a favorable weld by forming a buffer, which accommodates differences in thermal expansion and reduces the risk of corrosion at the joint.
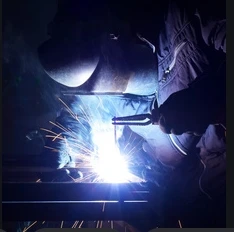
The expertise of seasoned welders underscores the importance of maintaining proper technique and the relevance of rod composition. Using a rod with a distinct chromium and nickel base ensures the weld's integrity and prevents the formation of brittle fusion zones. Knowledgeable professionals may also advise using 308L rods for specific applications, which although primarily suited for stainless-to-stainless welding, can sometimes offer versatility in specific SS to CS applications due to its inherent ductility and corrosion resistance.
ss to cs welding rod
Experience further dictates that pre-weld preparation is pivotal. Cleaning both metal surfaces extensively to remove contaminants can alleviate potential welding defects. The effectiveness of the welding rod is maximized when couched in thorough pre-weld cleaning, thereby augmenting the structural cohesiveness of the weld.
Authoritative voices within the industry stress the critical nature of temperature control during the welding process. Alterations in temperature can drastically affect the weld's outcome, particularly when joining dissimilar metals like SS and CS. The choice of welding rod can influence the ease with which the weld remains consistent under thermal stress, maintaining composition without unwanted dilution or the formation of unwanted carbides.
Trustworthiness is cultivated through a disciplined adherence to safety standards and industry regulations. For instance, ensuring that the welding environment is optimized for ventilation can mitigate the risk associated with fumes generated during the welding process. Certified rods, which undergo rigorous testing and come highly recommended by industry standards, provide an additional layer of reliability, ensuring that professionals utilize products that have been vetted for performance and safety.
In conclusion, the nuanced task of welding stainless steel to carbon steel requires an integration of specialist knowledge, practical expertise, and authoritative guidance. The choice of welding rod serves as the cornerstone in achieving a robust, reliable weld that meets professional standards. By paying meticulous attention to the compatibility of materials, welding techniques, and safety protocols, welders can effectively bridge the material divide, ensuring that both integrity and performance are uncompromised. This understanding is vital for fostering trust and credibility within the industry, upholding the high standards synonymous with expertly executed welding projects.