Welding rod selection can be a daunting task, especially when specific material compatibility and structural integrity are at stake. In the world of stainless steel (SS) to mild steel (MS) welding, understanding the appropriate welding rod code is crucial to achieving optimal results. A well-informed choice hinges on comprehensive expertise, real-world experience, authoritative recommendations, and a firm foundation of trustworthiness.
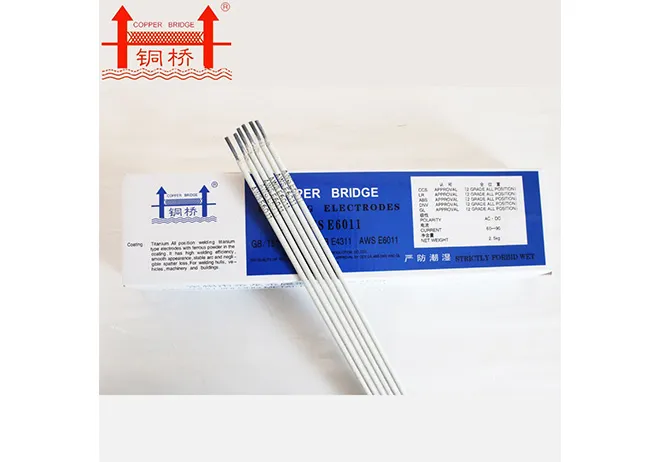
Stainless steel and mild steel each possess distinct chemical compositions and material properties, posing unique challenges when fused together. The key lies in using a welding rod that can accommodate the differing expansion rates, melting points, and corrosion resistance properties inherent to both metals. When welding SS to MS, E309L electrodes are highly recommended and widely endorsed by industry experts.
The E309L welding rod is engineered for joining dissimilar metals. It boasts a low carbon composition, designed to minimize carbide precipitation during the welding process. This feature is particularly significant when working with stainless steel, as it prevents intergranular corrosion—a common issue that can weaken the welds over time. Industry professionals emphasize the importance of choosing a low-carbon variant, particularly when the finished product will be subjected to high heat or corrosive environments.
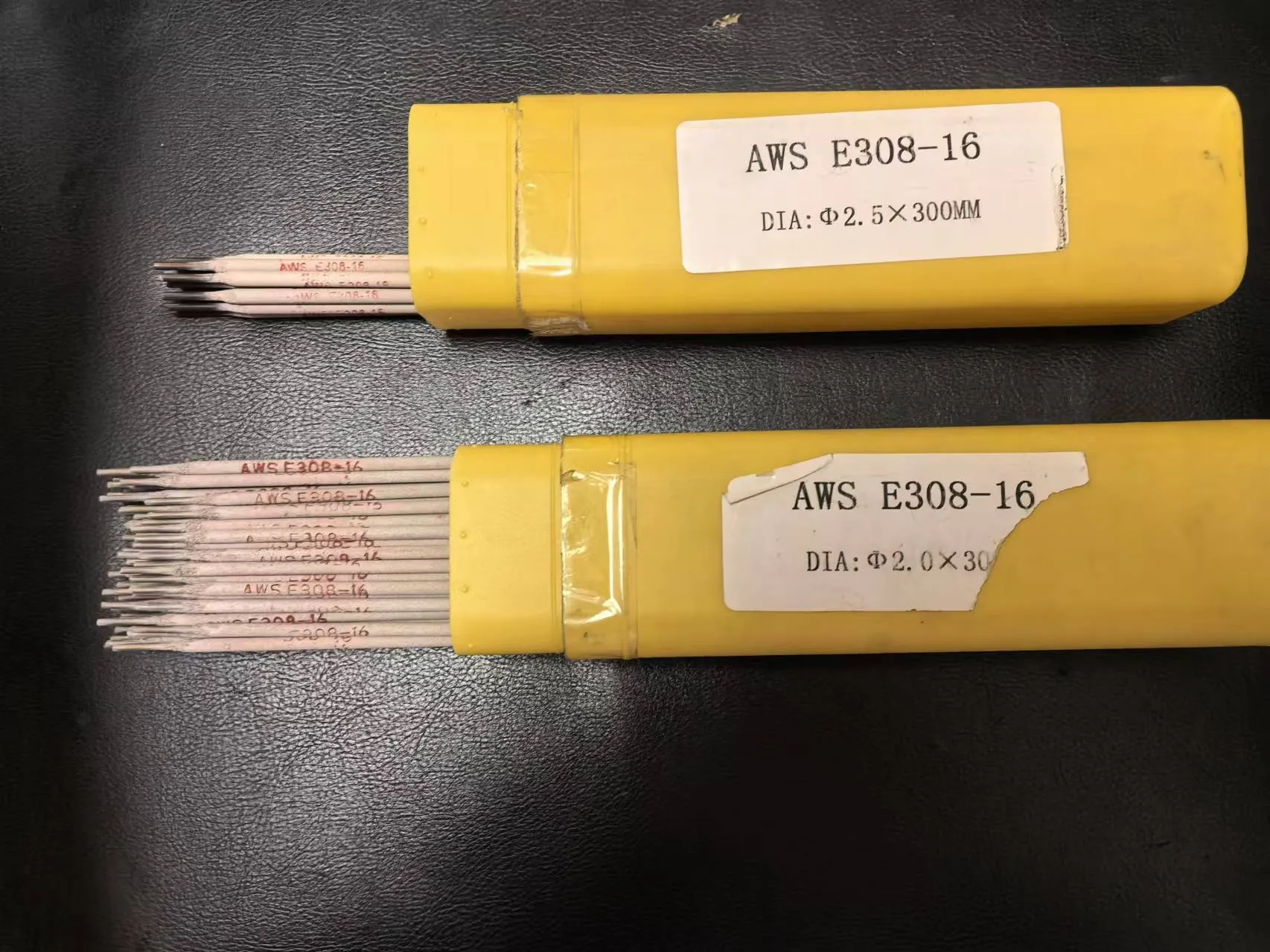
For welders seeking to ensure structural integrity and durability, the real-world performance of E309L welding rods speaks volumes. Reports from the field consistently indicate that these rods provide excellent fusion between stainless and mild steel, producing a stable and resilient joint. In industries where reliability is paramount, such as construction, piping, and automotive manufacturing, E309L’s performance is proven and trusted.
Expertise within the welding community underscores the significance of selecting a rod that not only aligns chemically but also facilitates ease of use and consistent performance. E309L electrodes stand out for their superior arc stability, a feature that simplifies the welding process and reduces the likelihood of defects such as porosity or cracks. This characteristic makes them a favored choice for both seasoned welders and newcomers who demand precision and reliability in their projects.
ss to ms welding rod code
The authoritativeness of E309L welding rods is supported by numerous standards and certifications from reputable bodies such as the American Welding Society (AWS). These rods meet stringent quality criteria, ensuring that they can withstand rigorous operating conditions while maintaining performance integrity. Adherence to such standards reinforces trust among welders and engineers, promoting confidence in the materials used for critical applications.
On the frontlines of welding safety, using the correct rod code is paramount. E309L is formulated to produce a minimal spatter compared to alternative options, thereby reducing clean-up time and enhancing operator safety. Given that welding processes inherently involve exposure to high temperatures and fumes, selecting an electrode that minimizes potential hazards aligns with best safety practices. Occupational health and safety professionals consistently advocate for using materials like E309L that align with these principles.
The trustworthiness of welding materials can significantly impact the quality of the finished product. E309L electrodes are manufactured by reputable companies known for their commitment to quality control and consistency. When sourcing welding rods, selecting a trusted manufacturer ensures that each batch meets high standards of performance and reliability, minimizing the risk of failures that could lead to costly reworks or safety incidents.
In summary, the importance of choosing the right welding rod code when joining stainless steel to mild steel cannot be understated. Real-world experience, professional expertise, and authoritative validation favor E309L electrodes as the premier choice for such applications. Their proven performance, ease of use, adherence to standards, and commitment to safety make them a reliable and trusted solution in diverse welding scenarios. As innovation in material science continues, staying informed about the best practices and latest advancements further enhances the quality and durability of welded structures.