Selecting the appropriate welding electrode is crucial for ensuring high-quality welds, especially when transitioning from stainless steel (SS) to mild steel (MS). For many engineers and welders, this task demands a deep understanding of both materials’ properties, the welding process, and the specific project requirements. Getting it right not only affects the structural integrity of the finished product but also impacts efficiency and cost-effectiveness.
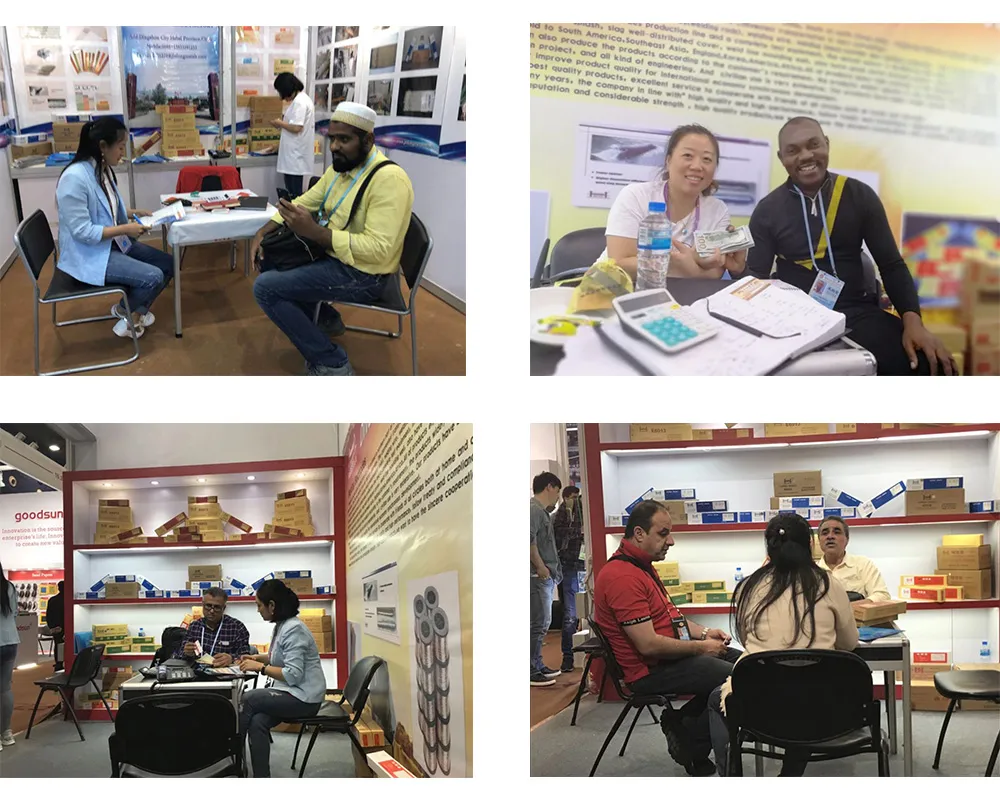
Every professional welder knows the importance of using the correct electrode. In projects involving SS to MS welding, there is an inherent challenge due to the differing compositions and mechanical properties of the materials. Stainless steel boasts corrosion resistance and a higher melting point thanks to its chromium content. Conversely, mild steel, known for its ductility and weldability, lacks chromium, making it susceptible to corrosion. When welding these two together, the choice of electrode can either mitigate or amplify these material disparities.
One of the most recommended electrodes for welding stainless steel to mild steel is the E309 series. This electrode is popular for a few critical reasons. First, its composition is tailored to handle the carbon diffusion that occurs between SS and MS during welding, reducing the risk of welding defects such as fissures or cracks. Additionally, E309 electrodes provide a weld deposit with adequate corrosion resistance, a necessity given the propensity of SS to corrode when improperly welded. The chromium and nickel content in E309 matches the need for a transitional weld that can maintain structural integrity while preserving the attributes of both parent metals.
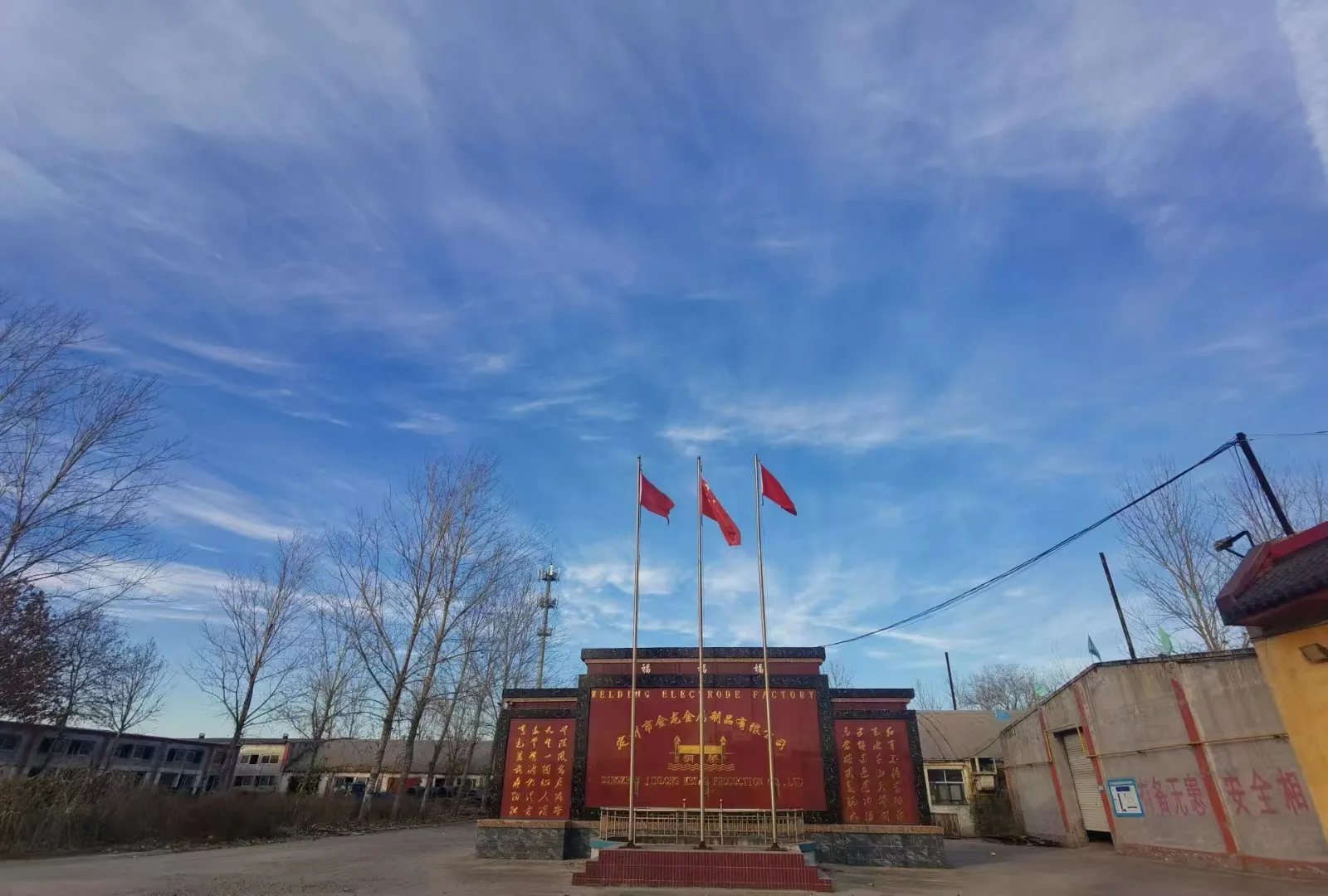
Another excellent option is the E312 electrode. This particular electrode is often highlighted for its high tensile strength and its ability to bridge dissimilar metals. E312 is superb for applications where the joint may experience high stress or dynamic loading due to its robustness and its ability to endure significant thermal cycling. This makes it particularly useful in fabrication projects where welds between SS and MS are exposed to mechanical stresses or thermal fluctuations.
For welders, thorough preparation is equally as vital as selecting the right electrode. Before initiating the weld, it’s paramount to clean the base metals meticulously. Any remnants of oxides or contaminants can compromise the integrity of the weld. Mechanical cleaning with brushes or grinders is advisable, followed by chemical cleaning solutions if necessary. A prepared, clean surface ensures maximum penetration and fusion, crucially averting common problems such as porosity or weak joints.
ss to ms welding electrode number
Moreover, managing the heat input during welding is a skill that experienced welders cultivate. Excessive heat can distort the base metals or lead to inadequate fusion, especially when dealing with dissimilar metals. A balance must be struck where the heat is sufficient to facilitate the fusion without altering the desirable properties of the stainless steel or causing excessive brittleness in the mild steel.
Post-weld treatments, such as passivation for stainless steel components, further enhance the longevity and performance of the weld. This treatment involves cleaning the weld area with acid solutions to remove free iron from the surface, thereby restoring the corrosion resistance of the stainless steel. It’s an essential process, particularly in projects subjected to corrosive environments.
Ultimately, the success of welding stainless steel to mild steel heavily depends on the expertise leveraged during the planning and execution phases. Skilled professionals understand that each step, from choosing the right electrode to performing post-weld treatments, contributes to the overall quality and durability of the weld. When executed correctly, SS to MS welds exhibit both strength and resilience to environmental stressors.
In conclusion, welding SS to MS effectively is a testament to a welder’s ability to merge theory and practice, integrating materials science, precision techniques, and post-weld treatment processes. The strategic choice of electrodes, such as E309 and E312, along with meticulous preparation and execution, are the hallmarks of a successful weld in this challenging yet rewarding application.