Welding stainless steel with rods is a critical task that requires precision, knowledge, and the right tools to achieve high-quality results. Unlike other metals, stainless steel is popular for its resistance to corrosion and rust, making it ideal for various applications ranging from industrial machinery to architectural designs. To weld stainless steel efficiently, professionals must gain insights from real-life experiences and understand key elements like technique, equipment, and safety precautions.
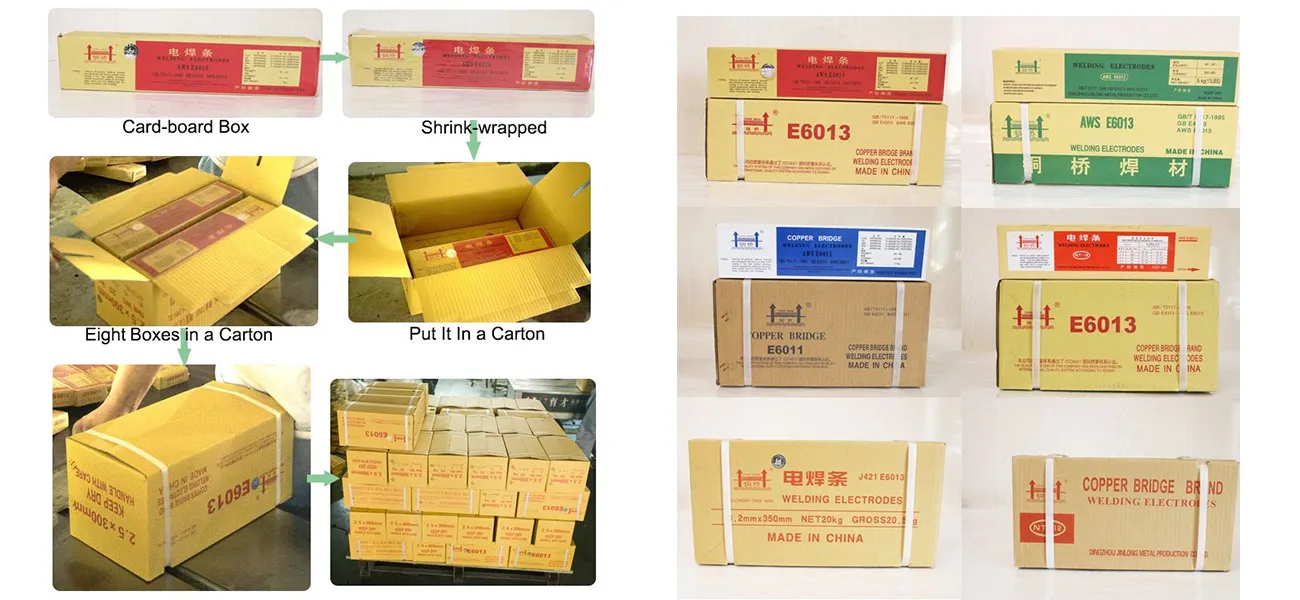
Experience plays a crucial role in rod welding stainless steel. Welders must adapt to different grades of stainless steel, each with unique properties that can affect the outcome of the weld. For instance, Austenitic stainless steels, such as 304 and 316, are commonly used and have high nickel and chromium content, which require careful handling to avoid warping. The experience gained from hands-on projects allows welders to master the dexterity and control needed to produce consistent and flawless weld joints.
Expertise in rod welding stainless steel involves understanding the nuances of welding processes like GTAW (Gas Tungsten Arc Welding) and SMAW (Shielded Metal Arc Welding). GTAW, also known as TIG welding, is often preferred for stainless steel due to its precision and ability to create clean, strong welds without the need for filler material in some cases. SMAW, or stick welding, offers more portability and is versatile but can introduce more impurities if not done correctly. Selecting the right welding process depends on the project requirements, material thickness, and operator skill level.
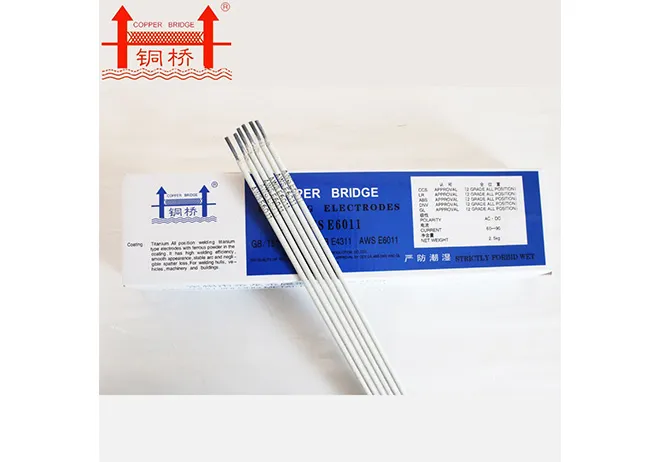
When it comes to the welding rods themselves, choosing the appropriate filler material is equally important. For stainless steel, rods such as ER308L and ER309L are frequently used. The number '308L' indicates a lower carbon content, which helps minimize carbide precipitation and enhances anti-corrosive properties. Welding professionals will often select a filler that matches the material's base composition to ensure compatibility and maintain the structural integrity of the weld.
Authoritativeness in the field is established by following industry standards and guidelines. Organizations like the American Welding Society (AWS) set standards that ensure quality and safety across welding projects. Utilizing certified equipment and adhering to these standards not only improves the credibility of a welding professional but also ensures client satisfaction by reducing the likelihood of weld failures or defects.
rod welding stainless steel
Trustworthiness is cultivated through a commitment to safety and quality assurance. Welding stainless steel rods involves handling high-heat equipment and potentially hazardous materials. Special attention must be paid to protective gear, including helmets, gloves, and clothing rated for welding tasks. Regular maintenance and inspection of welding tools serve as another layer of trustworthiness, guaranteeing that projects are completed safely and efficiently.
Fabricators and welders working with stainless steel must also keep an eye on heat control. Excessive heat can lead to distortion and reduced corrosion resistance, which compromised the material's expected lifecycle. Effective heat management techniques include delivering proper heat input, using intermittent welds, and allowing for adequate cooling periods between passes.
Continuous learning and keeping abreast with technological advancements play a vital role as the industry evolves. Focusing on the latest trends, such as robotic welding and advancements in welding technology, offers competitive advantages and the opportunity to enhance working methods and output quality. Attending workshops, certifications, and welding seminars contribute to building a solid foundation of knowledge and staying updated with the latest practices.
Ultimately, mastering rod welding stainless steel combines real-world experiences, specialized expertise, adherence to authoritative guidelines, and an ingrained culture of safety and trustworthiness. These elements not only lead to superior welding outputs but also ensure that professionals maintain a competitive edge in a demanding field, delivering exceptional results that meet and exceed client expectations.