Choosing the right pipe welding rod can significantly impact the quality and longevity of a welded joint. This is an area that requires a substantial amount of understanding and expertise, particularly when dealing with various materials, environments, and project specifications. Pipe welding rods, also known as filler metals, are crucial components in the welding process as they fill the joint between the pipes. Therefore, selecting the appropriate type is vital for achieving optimal results.
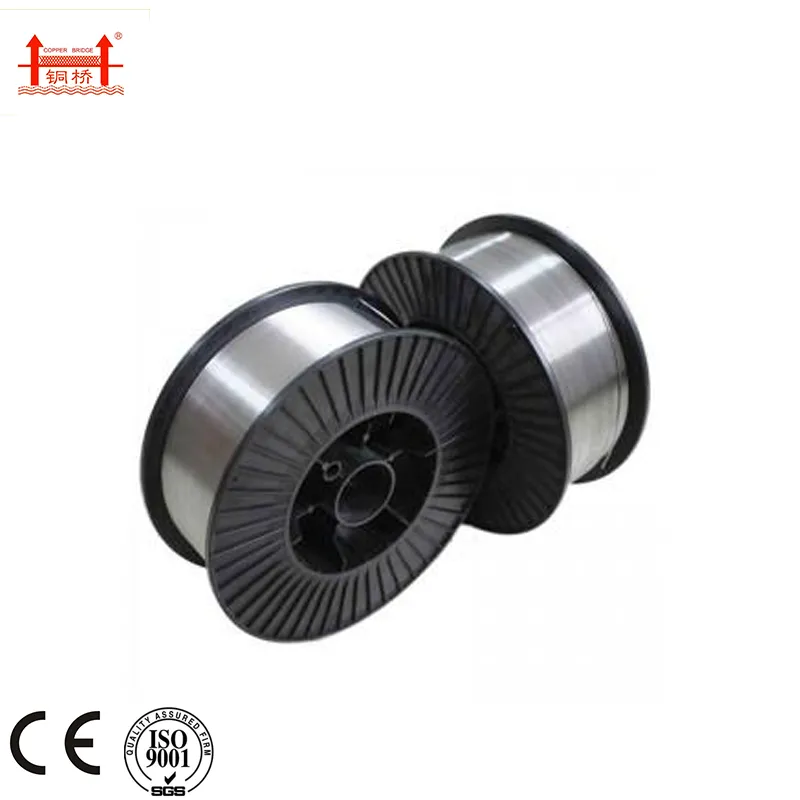
One of the most extensively used rods is the E6010 electrode, widely recognized for its versatility and reliability. This rod is ideal for root passes in pipe welding, especially in scenarios where deep penetration is required. Its ability to create stable arcs even under harsh conditions, such as greasy, dirty, or rusty surfaces, makes it a go-to choice for professionals tackling challenging projects. Welders trust this rod to deliver consistent quality, maintaining structural integrity in pipelines subjected to high-pressure environments.
In contrast, the E7018 electrode is highly recommended for projects demanding smooth finishes and strong mechanical properties. Its low-hydrogen makeup reduces the risk of cracking, offering enhanced ductility in the resulting welds. It’s especially favored in construction and structural applications, where the aesthetics and strength of the weld are paramount. Expert welders underline the importance of keeping the E7018 dry to preserve its properties, as moisture can compromise its integrity and lead to porosity.
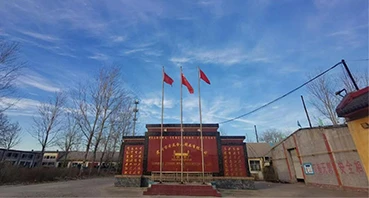
For stainless steel pipes, ER308L is frequently used because of its compatibility and performance with such materials. Its low carbon content minimizes the possibility of carbide precipitation during welding, which can otherwise lead to intergranular corrosion. This rod offers excellent resistance to corrosion, a critical factor in industries such as food processing or chemical manufacturing, where welded pipes might contact reactive substances.
pipe welding rod types
Another essential type is the E316L-16 rod, designed for welding molybdenum-bearing austenitic stainless steels and sometimes low-carbon stainless grades. It provides exceptional corrosion resistance in acidic environments, making it suitable for chemical processing plants. Welders with expertise in stainless steel applications often choose this rod for projects that necessitate enduring reliability and robustness under corrosive conditions.
While selecting a pipe welding rod, factors such as the base material, the environment the pipe will be exposed to, and the desired mechanical properties should be considered. It's not just the type of rod but also the skills of the welder that determine the success of a welding project. Welders with a high level of expertise bring experience, precision, and a nuanced understanding of how different rods behave under varying conditions.
Trust in the quality and the performance of your chosen welding rod can only be built through experience and robust knowledge of the welding field. Manufacturers often provide detailed specifications and certifications to support welders in making informed decisions. This information is essential for those looking to comply with industry standards and regulations, ensuring safety and efficacy in their welding projects.
In conclusion, understanding the diverse types of pipe welding rods available and their specific applications can greatly enhance the quality and durability of your welded joints. By leveraging professional knowledge and experience, welders can select the most appropriate rods for their specific needs, ensuring long-lasting and high-quality results in their pipeline projects. The right choice not only achieves technical specifications but also builds a foundation of trust and authority in the competitive field of welding engineering.