Cast iron repair is a unique challenge in the world of welding, requiring specialized techniques and materials to ensure successful and durable outcomes. When embarking on a cast iron welding project, one critical choice is the selection of filler material. Nickel rods, often referred to as ni rods, have emerged as an industry favorite due to their compatibility and effectiveness.
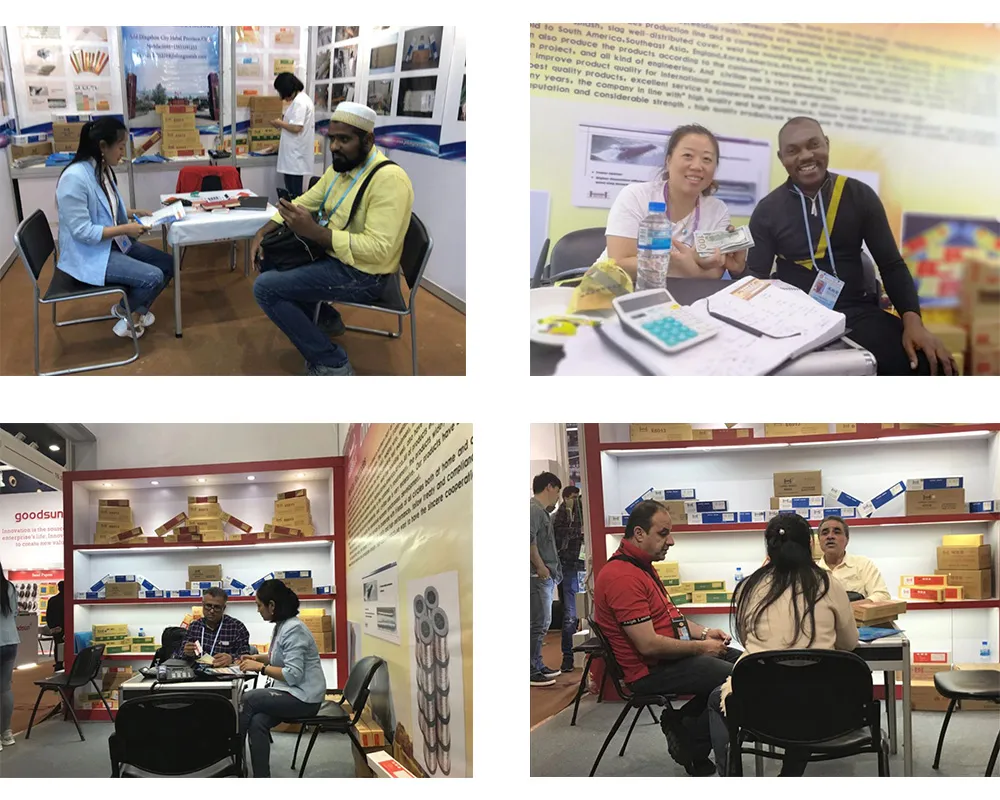
Understanding the composition and properties of cast iron is paramount to effectively welding it. Cast iron, known for its excellent compressive strength and wear resistance, contains a high percentage of carbon, which can cause challenges such as cracking when welding. The carbon content in cast iron tends to create a brittle phase with the high thermal stresses involved in welding. This brittleness is where the choice of filler material comes into play.
Ni rods offer several advantages, making them a prime choice for cast iron welding. Firstly, nickel has a thermal expansion rate similar to that of cast iron, which reduces the risk of cracking due to thermal stress. This compatibility ensures that as the welded area cools, the chances of stress-induced cracks are minimized.
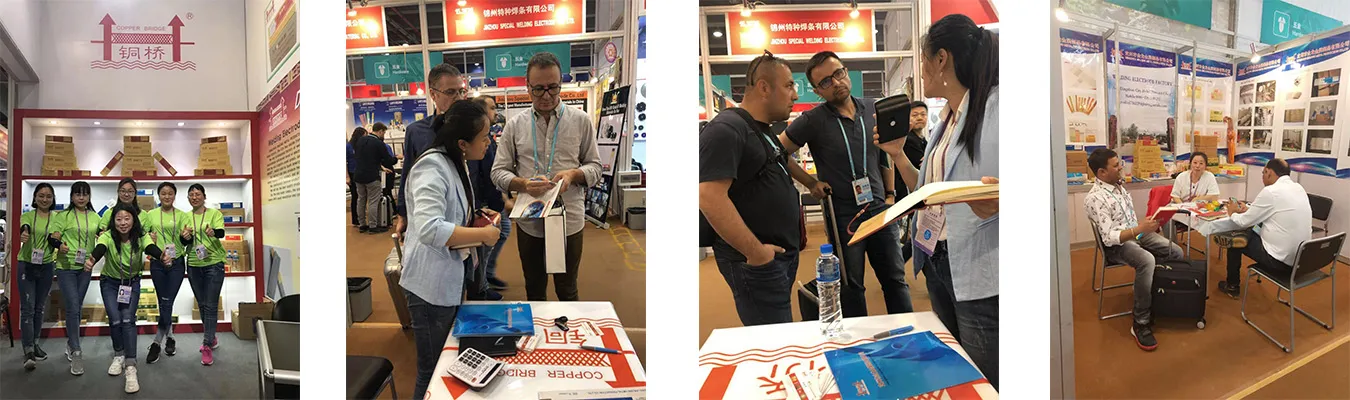
Additionally, nickel rods provide excellent machinability. After the weld cools and solidifies, machining might be required to restore the part to its original specifications. Using ni rods ensures that this machining can be done with ease, saving time and resources. Furthermore, nickel exhibits corrosion resistance properties, an added advantage in extending the life of the repaired item in environments where corrosion is a concern.
Beyond technical specifications, experience plays a crucial role in the successful application of ni rods in welding cast iron. It's imperative for welders to preheat the cast iron component before beginning the welding process. The reason is to reduce thermal shock and to slow down the cooling process post-welding, both of which are essential to prevent cracking. The preheat temperature can vary but often falls between 500 to 1200 degrees Fahrenheit depending on the size and shape of the piece.
ni rod welding cast iron
In actual practice, one must pay attention to welding techniques as well. Short weld passes are advisable since they help in controlling the heat input into the cast iron, again minimizing the risk of heat-related issues like cracking. Peening the weld bead after each pass can also relieve stress, a technique often incorporated by expert welders who use ni rods.
Authoritative sources in the welding industry often recommend nickel rods specifically when dealing with high-stress applications where mechanical reliability is non-negotiable. Their backing and endorsements add a layer of trust and credibility in choosing ni rods for cast iron welding projects.
From a professional's standpoint, the trustworthiness of ni rods is demonstrated over countless projects where failure is not an option. Extensive testing and approval by industrial bodies further cement their place in professional welding kits around the globe. By implementing these techniques and tools, fabricators and welders can not only ensure their work stands the test of time but also build a reputation for quality and reliability in the repair and maintenance sector.
In conclusion, choosing the right filler material is more than just a technical decision—it requires a balance of expertise, experience, and trustworthiness. When it comes to welding cast iron, ni rods offer the most comprehensive solution, combining material compatibility, ease of use, and excellent post-weld properties. Through thoughtful application and a deep understanding of the material's characteristics, welders can achieve remarkable results, ensuring their projects are both durable and reliable.