Nickel-chromium welding rods, commonly referred to as Ni-Cl rods, have become a cornerstone in various industrial applications due to their exceptional properties. These types of welding rods are particularly revered in sectors that demand robust performance under strenuous conditions—such as aerospace, petrochemical industries, and power generation. This detailed examination delves into the various intricacies that make Ni-Cl welding rods indispensable, offering insights enriched by hands-on experience and technical expertise.
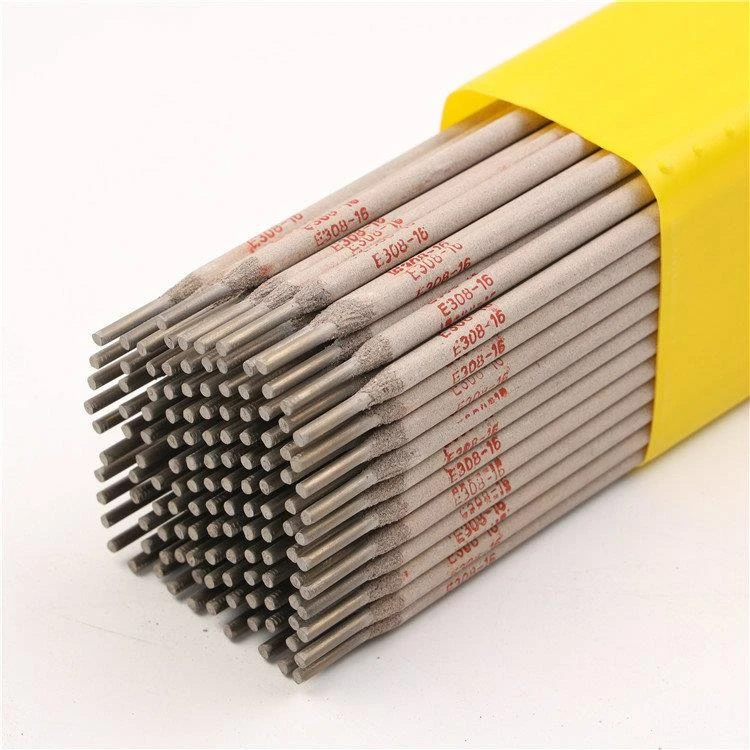
Understanding the Composition and Its Benefits
At the core of Ni-Cl welding rods is an alloy primarily comprising nickel and chromium. Nickel contributes to its superior corrosion resistance, ensuring longevity even when exposed to harsh chemical environments. Chromium enhances the alloy's ability to withstand oxidation, particularly at elevated temperatures. This blend transforms the rods into a reliable choice for welding tasks that involve stainless steel and other nickel-based alloys.
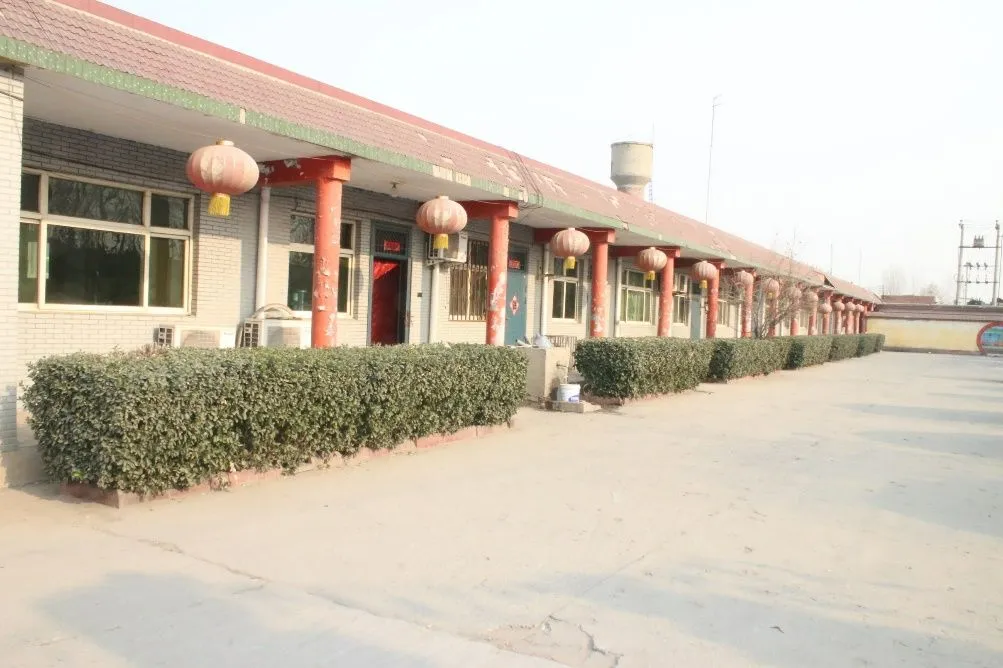
Industry Usage and Advantages
In the aerospace industry, welding rods made from nickel-chromium are pivotal. Aircraft systems often require components that can resist extreme thermal stresses and corrosive elements. Ni-Cl welding rods provide a seamless joining solution that maintains structural integrity despite these challenges. For instance, in turbine components where high thermal efficiency is crucial, the use of these rods ensures durability and reliability.
Similarly, in the petrochemical industry, pipelines and reactors often face the dual challenge of high temperatures and corrosive chemicals. Employing Ni-Cl rods facilitates the maintenance of a leak-proof and corrosion-resistant infrastructure. This is not merely theoretical—engineering reports and case studies have demonstrated that the long-term operational efficiency and safety of pipelines are significantly enhanced when welded with these materials.
Practical Considerations and Professional Recommendations
Welders with experience in using Ni-Cl rods often emphasize the importance of pre-weld preparation and post-weld heat treatment. Proper cleaning of the base metal is essential; any residual contaminants can lead to defective welds. Furthermore, maintaining the correct welding temperature is critical, as excessive heat can lead to unwanted metallurgical changes that compromise the strength of the welded joint.
ni cl welding rod
Expert welders suggest a few other practical tips. For instance, maintaining a steady hand and consistent speed is vital to prevent overheating and subsequent warping. Additionally, using controlled environments such as inert gas chambers can help maintain the purity of the weld area, further enhancing joint quality.
Technical Specifications and Choosing the Right Rod
Selection of the appropriate Ni-Cl welding rod depends on several technical factors—tensile strength, ductility, and work environment among them. Typical tensile strengths for these rods range from 70,000 to over 100,000 psi, making them suitable for high-stress applications. Ductility, on the other hand, ensures that the weld can absorb shocks and vibrations without cracking.
For power generation facilities, particularly those involving nuclear power, the choice of Ni-Cl rods is often mandatory. The rods' ability to create joints that withstand not only thermal cycling but also radiation exposure underscores their critical importance. According to various industry standards and certifications, these rods are often recommended or required by both national and international safety boards.
Future Trends and Innovations
The landscape of welding rods, including those made from nickel-chromium, is gradually evolving with technological advancements. Innovations such as automation in welding processes and the use of AI for precision operations are anticipated to increase welding efficiency and reduce human errors. Welding rods are now being developed with even more resilient alloys to cater to the ever-increasing demands for performance and safety.
Reputable stakeholders in the industry, such as manufacturers and regulatory bodies, continue to invest in research to refine and test these rods under new environmental challenges. Their insights and findings are invaluable resources for welding professionals aiming to stay updated with the latest practices.
By emphasizing real-world applications, technical excellence, and continuous innovation, Ni-Cl welding rods prove their indispensability in modern industry. Their robust nature and versatility not only meet but often exceed the stringent demands of specialized fields, solidifying their reputation as a critical component in the toolkit of skilled welders worldwide.