Welding mild steel to stainless steel presents a unique set of challenges that necessitate careful consideration of various factors, ranging from the choice of welding rod to the techniques employed. This expertise-driven guide demystifies the process, helping you achieve exceptional results when combining these two distinct metals.
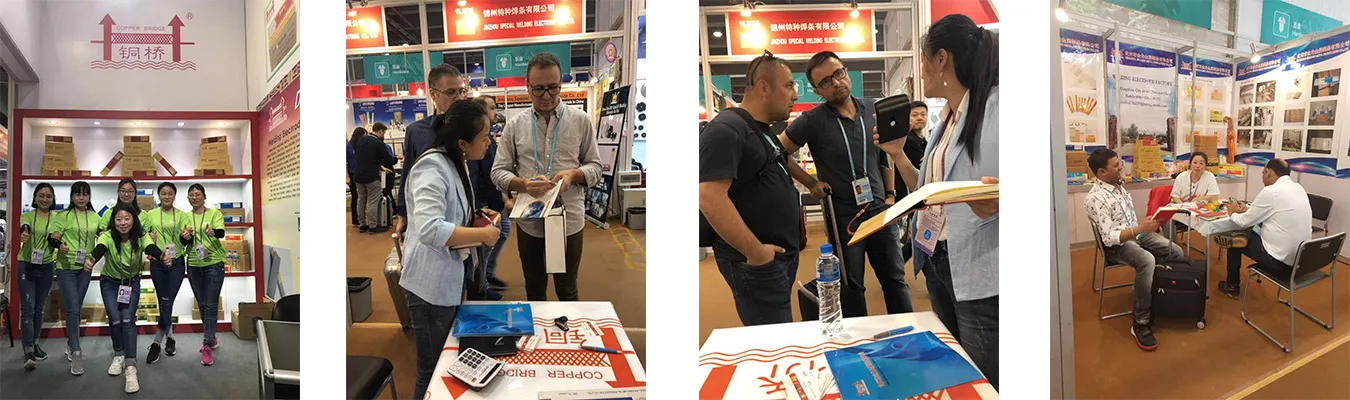
Welding dissimilar metals, such as mild steel and stainless steel, demands a profound understanding of metallurgy and precision techniques. Stainless steel, known for its corrosion-resistant properties due to its chromium content, behaves differently under heat compared to mild steel, which is composed primarily of iron and carbon. Mismatched thermal expansion rates, along with differing melting points, can lead to weld cracking or structural failures if not addressed skillfully.
The selection of the right welding rod is paramount. Experts often recommend using a rod specifically designed to bridge the gap between the two metals. A common choice is the 309L electrode, renowned for its compatibility and ability to fuse stainless steel to mild steel effectively. This electrode contains a balanced mix of chromium and nickel, providing the necessary alloying elements that help in accommodating different expansion rates. Its low carbon content minimizes the risk of carbide precipitation, a common concern when welding stainless steel.
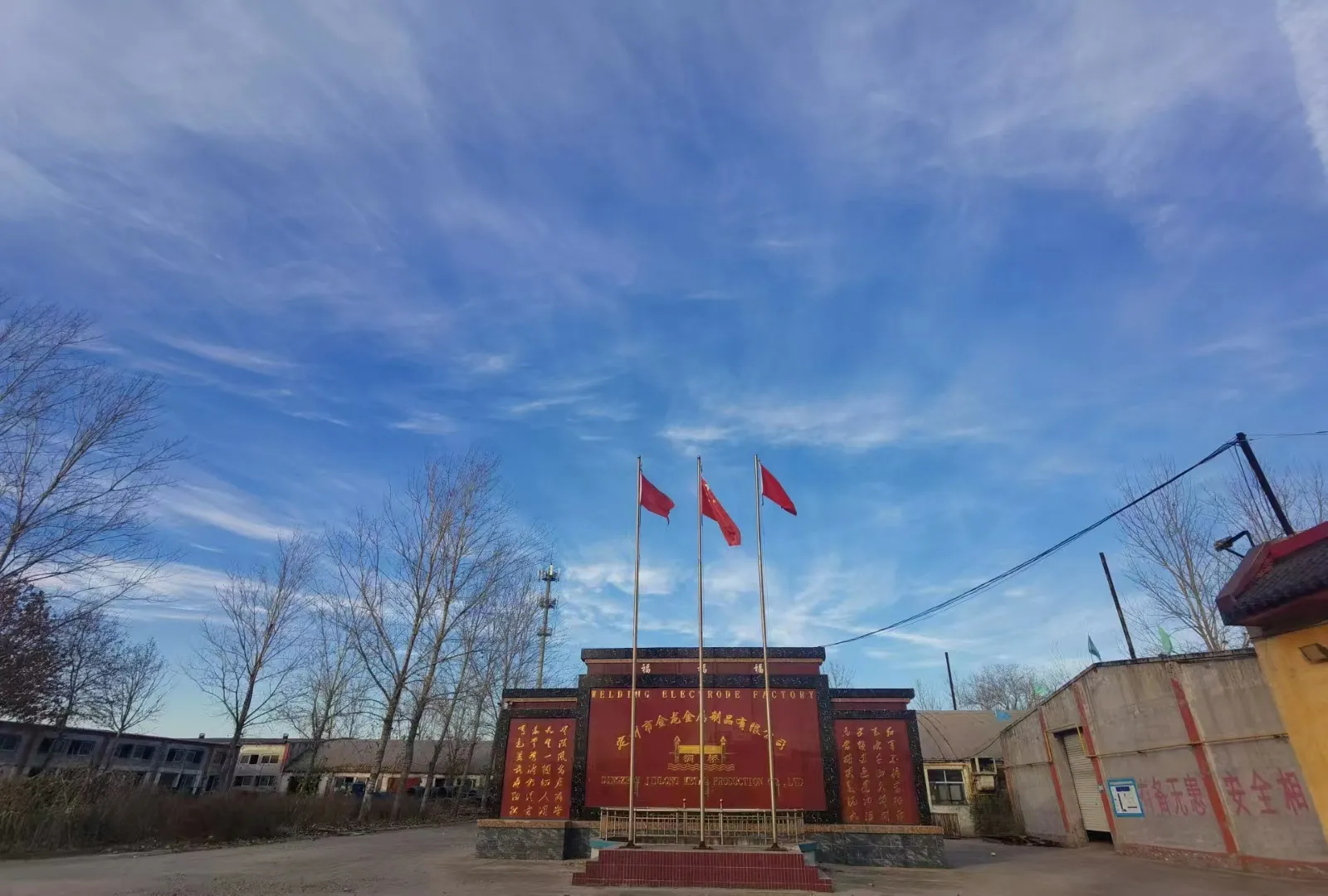
Beyond material selection, employing the appropriate welding technique is crucial. TIG (Tungsten Inert Gas) welding is often preferred due to its precision and control, allowing for meticulous technique in managing heat input. This is particularly important to avoid excessive overheating, which can cause warping or compromise the structural integrity of the weld joint. When performing TIG welding, it's critical to maintain a consistent arc length and employ a weaving motion to ensure uniform penetration and fusion.
Attention to pre- and post-weld treatments also plays a significant role in ensuring a robust weld. Pre-weld cleaning is vital; both the mild steel and stainless steel surfaces must be free from contaminants like oils, dirt, or rust. This can be achieved through thorough brushing, grinding, or the use of chemical cleaners. Post-weld, a controlled cooling process is advisable to reduce the risk of stress corrosion cracking or distortion. In some cases, a heat treatment process known as post-weld annealing may be utilized to relieve residual stresses and enhance the corrosion resistance of the joined metals.
mild steel to stainless steel welding rod
A critical aspect often overlooked is quality inspection. Employing methods such as dye penetrant inspection or ultrasonic testing can help detect surface and subsurface imperfections, ensuring that the weld is free from defects.
In terms of authoritative best practices, consulting standards from recognized bodies such as the American Welding Society (AWS) or the International Organization for Standardization (ISO) can provide valuable guidelines and specifications that enhance the credibility and trustworthiness of the welding process.
Additionally, real-world experience underscores the importance of environmental factors during the welding process. Avoiding breezy or humid conditions can prevent the shielding gases from being disrupted, which could otherwise lead to weld defects or oxidation.
In summary, the welding of mild steel to stainless steel using the right rod requires not only a theoretical understanding but practical expertise in metallurgy, precision techniques, and rigorous quality standards. By adhering to best practices and continually refining your methods based on experience, you can navigate the complexities of this process with confidence and achieve superior, durable welds.