Achieving impeccable welds with 7018 electrodes is the hallmark of skill and expertise in the welding sector. As a staple in the welding industry, 7018 welds are characterized by their versatility and ability to produce high-quality joints, even under challenging conditions.
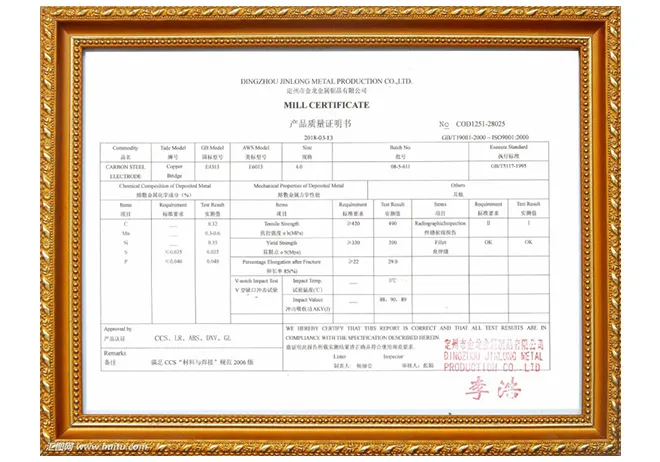
Welding with 7018 electrodes is akin to crafting art with metal. Known for their low-hydrogen characteristics, these rods require adept handling to prevent weld defects such as porosity or cracking. The expertise begins with understanding the composition a flux coating rich in iron powder and designed for easy slag removal, facilitating smooth, aesthetically pleasing finishes. Crafting good 7018 welds demands strict adherence to handling and storage protocols to avoid moisture contamination, which could compromise weld integrity.
Preparation is paramount. The workpiece's surface must be thoroughly cleaned to rid it of rust, oil, and dust, ensuring a pristine base for welding. Given the rod's susceptibility to moisture, storing them in a controlled dry environment is crucial. A rod oven at temperatures between 250°F to 300°F is ideal for preserving the electrode's low-hydrogen properties.
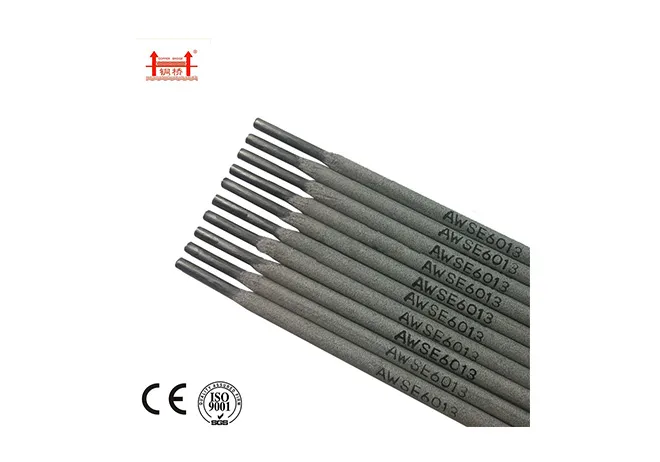
Hands-on experience plays a critical role when welding with 7018 rods. A crucial aspect is mastering the flat position, which is typically the most forgiving and yields optimal deposits. Positioning the electrode correctly—at a consistent angle—ensures proper penetration and bead appearance, which effectively unifies the joints. The technique requires holding a slight drag angle, typically between 10 to 15 degrees. This angle aids in controlling the puddle and maintaining an ideal arc length, critical for preventing undercut or excessive spatter.
Dodging common pitfalls is essential for creating quality welds. Experts emphasize maintaining consistent heat input, thereby avoiding excessive heat that could lead to distortion or weakening of the weldment. Alternating current (AC) or direct current electrode positive (DCEP) settings can significantly impact the outcome. Adjusting the amperage in accordance with electrode size is a subtle yet powerful means to achieve optimal penetration and fusion.
good 7018 welds
Expert welders focus on crafting continuity within weld passes. Each pass should blend seamlessly into adjacent ones, creating an unbroken line that indicates uniform penetration and coverage. With practice, welders develop an almost intuitive sense for judging the temperature and behavior of molten metal—a skill that distinguishes seasoned professionals from novices.
An authoritative foundation in metallurgy further informs expertise with 7018 welds. Understanding the impact of the iron powder coating on weld deposition rate and tensile strength can guide decisions on joint design and application. Furthermore, this knowledge extends into troubleshooting issues, such as pinpointing reasons for weld cracking or identifying the source of surface impurities.
Trustworthiness is developed through consistent delivery of robust, clean, and durable structures. Welders build reputations on their ability to leverage the strengths of 7018 electrodes across diverse applications—from load-bearing beams and structural steel to pipelines and general fabrication.
Success with 7018 rods hinges on blending advanced skill with continued learning and adherence to best practices. It's not just about the welds made today, but a continuous journey of mastering the craft to meet ever-evolving industry standards. Embracing both tradition and innovation, skilled welders with a penchant for precision and quality ensure that each weld tells a story of expertise and professionalism.