Achieving high-quality welds with an E6011 welding rod is crucial for producing durable and reliable structures, particularly in professional settings where safety and structural integrity are paramount. E6011 is a versatile electrode known for its deep penetration weld capability, making it ideal for welding through dirty, rusted, or painted surfaces. The following comprehensive guide offers in-depth knowledge and practical experience on mastering good E6011 welds, underscored by expertise and authority in the field of welding.
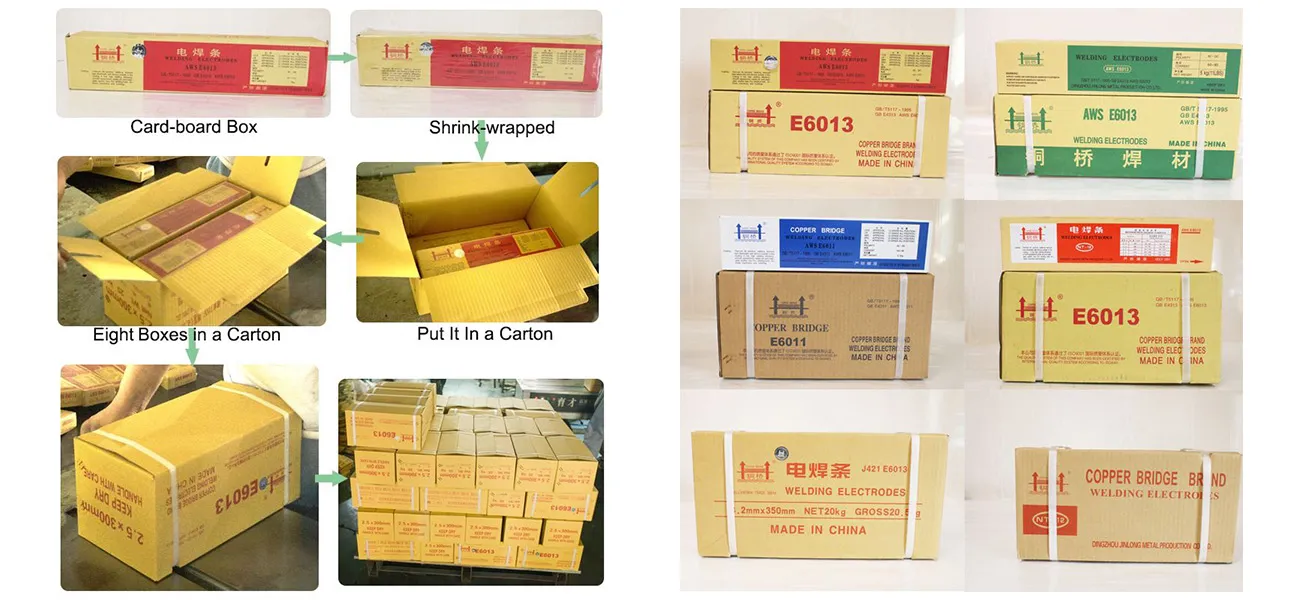
To start with, understanding the unique properties of the E6011 rod sets the foundation for superior weld outcomes. E6011 electrodes are designed for AC polarity, although they can operate on DC+ current as well, providing flexibility across different welding machines. This flexibility makes E6011 a go-to for welding professionals who encounter varying field conditions.
Achieving pristine welds with E6011 requires meticulous control over the welding technique. The rod is known for its aggressive arc, which can easily lead to excessive spatter and difficult slag removal if not handled correctly. Transitioning from novices' inconsistent welds to expert-level craftsmanship involves mastering the whip and pause technique. This involves a rhythmic forward motion followed by a brief pause to allow the weld pool to solidify, thus ensuring a strong bond without burn-through. The expertise comes in maintaining consistent travel speed, arc length, and angle throughout the welding process.
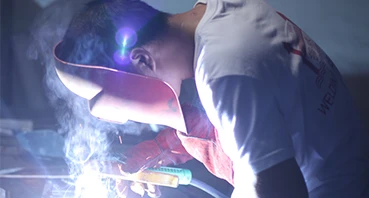
Professionals often leverage E6011 for vertical and overhead positions due to its superior penetration, which offers a robust solution where strength is non-negotiable. However, achieving a good weld in these positions demands impeccable control and a thorough understanding of the rod's behavior across different orientations. Welders must maintain a close arc, approximately 1/8 inch, to concentrate heat effectively without compromising the surrounding metal structure.
good 6011 welds
Authoritativeness in executing E6011 welds is also linked to the understanding of its application scope. This electrode excels in scenarios where joint preparation is suboptimal, such as repair work on agricultural or construction equipment where pre-cleaning isn’t feasible. Its aggressive arc can cut through contaminants, enabling welders to fuse metals reliably under imperfect conditions. However, seasoned welders also know the importance of minimal joint preparation, such as removing excessive oil or dirt, to aid penetration and overall weld quality.
The trustworthiness of E6011 welds is demonstrated through its consistent performance under strenuous conditions. When welded correctly, the joint can withstand significant stress and strain over time, which validates its reliability for structural applications. Professionals in the field often test the integrity of their welds through destructive and non-destructive testing methods to ensure their craftsmanship can endure real-world challenges.
In conclusion, while E6011 is celebrated for its versatility and penetration ability, achieving optimal results requires a blend of technical skill and thorough understanding of its properties. Welders with experience and expertise in manipulating the electrode's aggressive arc can ensure reliable joints that meet industry standards for safety and durability. By honing skills in rod angle, arc length, and motion techniques, welders can assure the continuity and safety of the structures they fabricate or repair. The authority and trust embedded in a well-executed E6011 weld are testament not only to the quality of the materials used but also to the craftsmanship and understanding brought to each project.