Welding with ductile iron rods demands a precise blend of technical expertise and practical know-how, serving industries ranging from automotive to construction. This unique welding material offers a fascinating blend of properties that require seasoned insights to exploit its full potential.
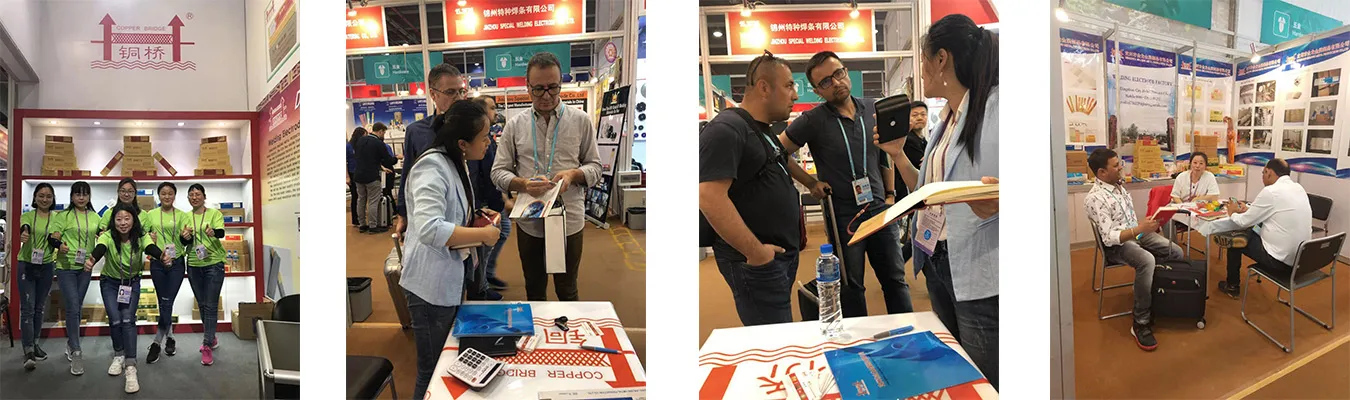
Ductile iron has gained prominence due to its excellent mechanical properties, particularly its remarkable tensile strength and elongation. These rods are commonly used to weld ductile iron pipes, designed to transport fluids under high pressure, and automotive components that require exceptional durability and shock resistance. Understanding the nature of ductile iron is crucial for successful welding, primarily due to its high carbon content and susceptibility to cracking if not handled correctly.
Preparation is the cornerstone of successful ductile iron welding. One of the most critical steps is controlling the preheat and interpass temperatures. Typically, the preheat temperature should be between 250°F to 500°F, depending on the material thickness and ambient conditions. Consistent temperature control helps reduce the thermal gradient, minimizing the risk of stress concentration and, subsequently, cracking. It is essential to note that rapid cooling post-welding can lead to brittle structures, so slow, controlled cooling is advised.
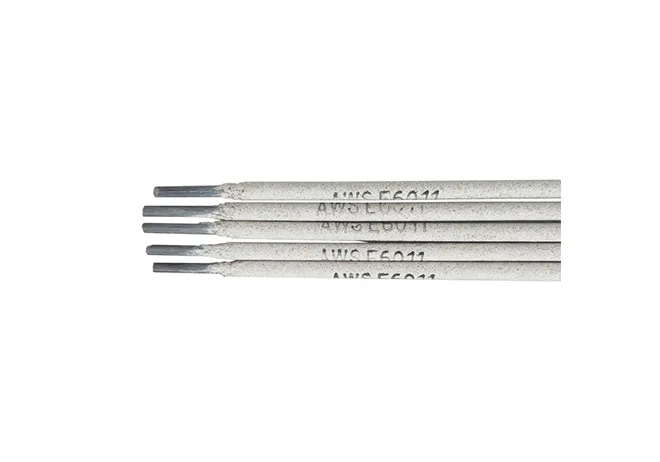
Choosing the right filler material is another pivotal aspect. Nickel-based electrodes are often the favored choice due to their ability to produce a softer weld, which is less prone to cracking. These electrodes accommodate the expansion and contraction that occurs as the weld area heats and cools. They also introduce less carbon to the weld pool, maintaining ductility. However, their higher cost and specific handling requirements must be weighed against the project's needs.
The welding technique also greatly influences the final product's integrity. For ductile iron, a short arc length is recommended to reduce the exposure of the molten metal to atmospheric elements, thereby minimizing contamination risks such as porosity and inclusions. The weaving technique should be avoided, as it increases the heat input and expands the heat-affected zone, leading to undesirable hardness.
Throughout the welding process, attention to detail in monitoring is paramount. Welders should employ dye penetrant testing regularly to identify any surface cracks before they propagate. This non-destructive testing method allows for immediate identification and rectification of faults, preserving the workpiece's integrity.
ductile iron welding rod
Post-weld heat treatment is frequently advised for ductile iron welds. This process relieves residual stresses and helps to soften the affected areas, restoring some of the ductility lost during welding. Typically, heating the weldment to approximately 1100°F and holding it at that temperature allows the carbon in the iron to be evenly distributed, thus preventing brittle welds.
In operational settings where ductile iron components are subjected to dynamic loads, it is crucial to prioritize the quality and methodology of the welding process over urgency. Ensuring each weld is executed with precision, adhering to specific temperature controls and technique, will enhance the longevity and performance of the weldment considerably.
Educating welding personnel on the nuances of ductile iron properties, and equipping them with the right tools and techniques, is an investment that yields significant returns in the form of reduced wastage, enhanced safety, and improved product performance. Proper documentation of welding procedures also fortifies the trust in welding operations, providing a benchmark for quality assurance and continuous improvement.
Finally, ongoing research and innovation in welding technology have introduced new consumables and automated systems that promise greater efficiency and accuracy in ductile iron welding. Manufacturers and project managers must stay informed about these advancements to maintain a competitive edge in quality and operational excellence.
As the industrial landscape continues to evolve, the demand for robust and reliable ductile iron welds will persist. By integrating comprehensive expertise, precise methodology, and unwavering commitment to quality, the full potential of ductile iron as a premier manufacturing material can be realized, propelling industries to new levels of performance and durability.