Cold welding cast iron has emerged as a groundbreaking solution for industries looking to repair metal without traditional thermal welding methods. Its significance lies not only in its ability to repair but also in offering a more environmentally friendly alternative to conventional practices. This method stands at the confluence of advanced material science and practical engineering, offering an efficient and sustainable solution for numerous applications.
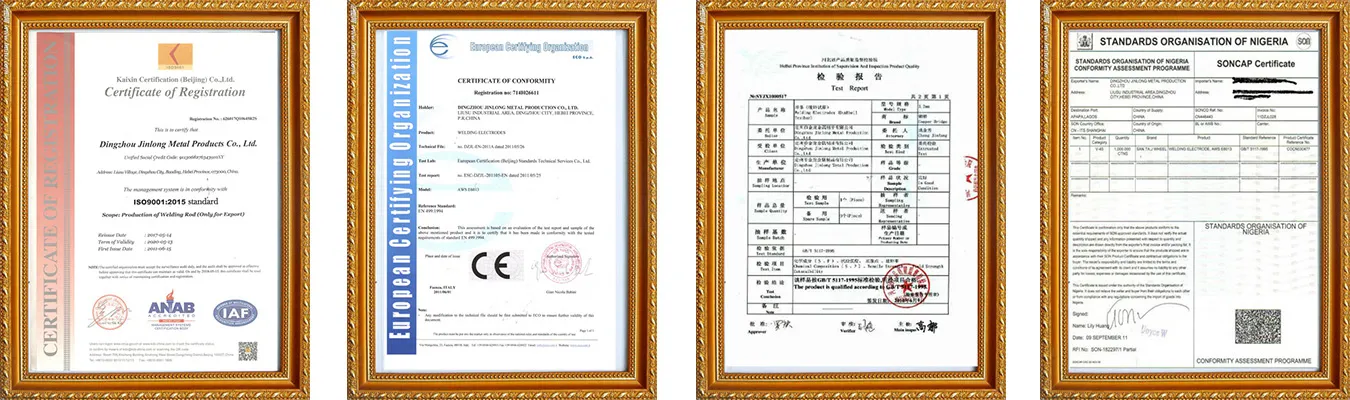
Cold welding, as the term implies, occurs at ambient or near-ambient temperatures, negating the need for heating the metals to be joined. This method uses pressure instead of heat, making it an ideal solution for cast iron—known for its brittleness and sensitivity to high temperatures. When applied correctly, cold welding ensures structural integrity without the downside of thermal distortion or introduction of additional stresses.
For those engaged in the industrial maintenance or repair sectors, understanding the nuances of cold welding can be a game-changer. By pressing the joint surfaces together under significant force, the atoms at the surface of the metals intermingle, forming a solid-state joint that is nearly as strong as the parent material. This seamless bond is devoid of the weaknesses typically seen in fusion-based methods like porosity or thermal cracking.
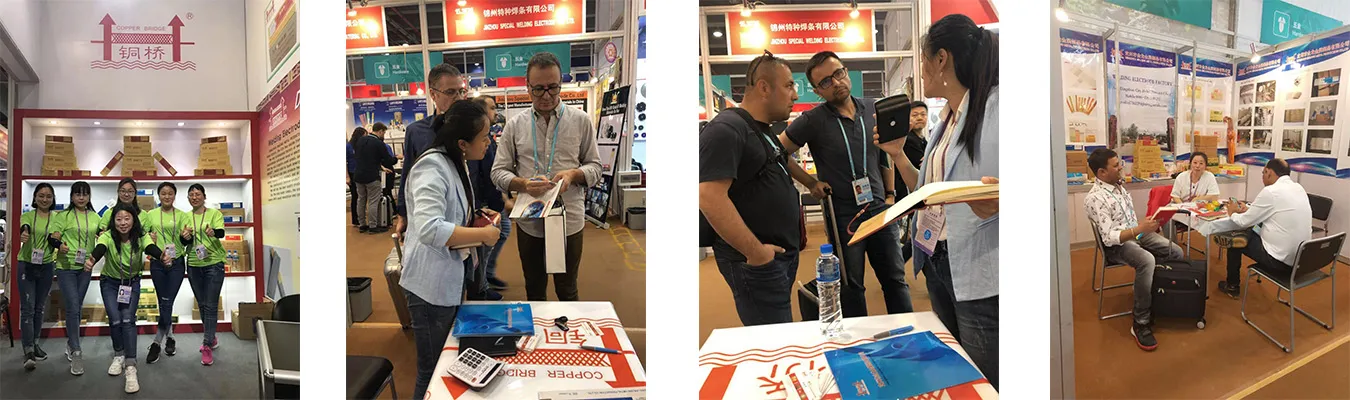
The advantages of cold welding cast iron extend beyond the absence of thermal influence. Firstly, it reduces the risk of introducing thermal stresses, which is a critical factor for a brittle material like cast iron, often leading to cracks upon heating. Secondly, the equipment involved in cold welding is less cumbersome and doesn't require the high-energy inputs associated with traditional welding systems, translating into cost efficiency.
When executing cold welding on cast iron, surface preparation is vital. The surfaces must be free from contaminants, including rust, oils, and grease. Achieving this clean surface typically involves rigorous cleaning processes such as wire brushing, sanding, or using chemical cleaners designed to strip off any potential barrier to the bonding process. The objective is to bring the surfaces into direct atomic contact, quintessential for a successful weld.
cold welding cast iron
Industries utilizing heavy machinery, automotive structures, and even artistic endeavors utilizing cast iron can significantly benefit from cold welding. It provides a method to repair and refurbish without altering the intrinsic qualities of the components involved. For instance, in the restoration of historical ironworks, where maintaining the original properties of the structure is essential, cold welding offers a nondestructive option that preserves both functionality and heritage.
Although advantageous, cold welding does require specialized knowledge to ensure effectiveness. Adequate pressure must be applied, and the technique’s suitability largely depends on the flatness and cleanliness of the surfaces combined with the precise alignment of the pieces. Furthermore, understanding which cast iron alloys respond best to cold welding is critical. Grey cast iron, for example, due to its graphite content, may present challenges, such as reduced weldability compared to ductile iron types.
Expertise in cold welding is growing, with educational resources and certification programs evolving to keep pace with industrial demand. Engaging with certified experts when employing cold welding for cast iron is recommended. These professionals bring a wealth of experience that not only simplifies the process but also enhances the reliability of the results.
Incorporating cold welding techniques represents a strategic move towards sustainability. The cold welding process omits harmful emissions typically associated with traditional welding, aligning with global trends prioritizing environmentally friendly manufacturing practices. As global environmental regulations tighten, the adoption of innovative methods like cold welding will likely increase.
As the world explores advanced manufacturing processes, cold welding of cast iron presents a pioneering solution that blends tradition with innovation. Its implementation across various industries underscores a commitment to improving operational efficiency, reducing costs, and embracing sustainable practices. Thus, it stands as a testament to the evolving nature of industrial repair methods, providing a robust alternative that reinforces, rather than compromises, the integrity of cast iron components.