Understanding the complexities involved in selecting the right electrode for welding is essential for any serious welder or manufacturer aiming to enhance precision, quality, and efficiency in their projects.
Different types of electrodes play crucial roles depending on the materials being welded, the welding conditions, and the desired outcomes. This knowledge not only reflects deep technical expertise but also establishes a trustworthy foundation for optimizing welding performances.
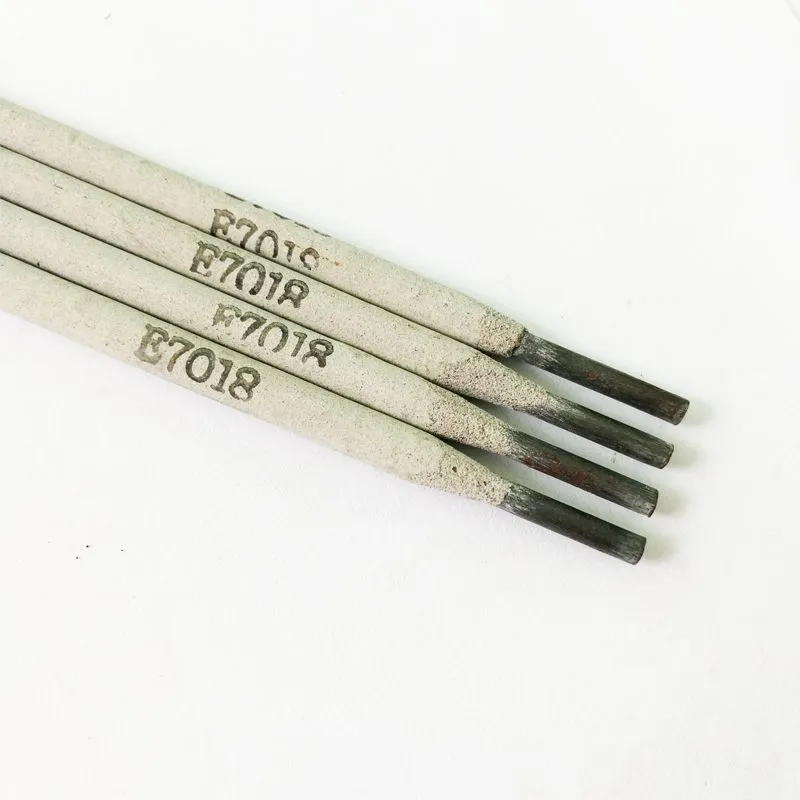
In the realm of welding, electrodes are classified into two primary categories consumable and non-consumable. The choice between these two types greatly influences both the ease of the welding process and the quality of the weld produced.
Consumable electrodes, as the name suggests, melt during the welding process to become part of the weld bead. These are extensively used in Metal Inert Gas (MIG) welding and shielded metal arc welding (SMAW). Within this category, you will find various types such as cellulose-coated electrodes, which are ideal for welding in positions that require deep penetration because of their fast burn-off rate. On the other hand, there are rutile electrodes that provide a smooth and visually appealing finish, making them suitable for welding thin sheets where appearance matters.
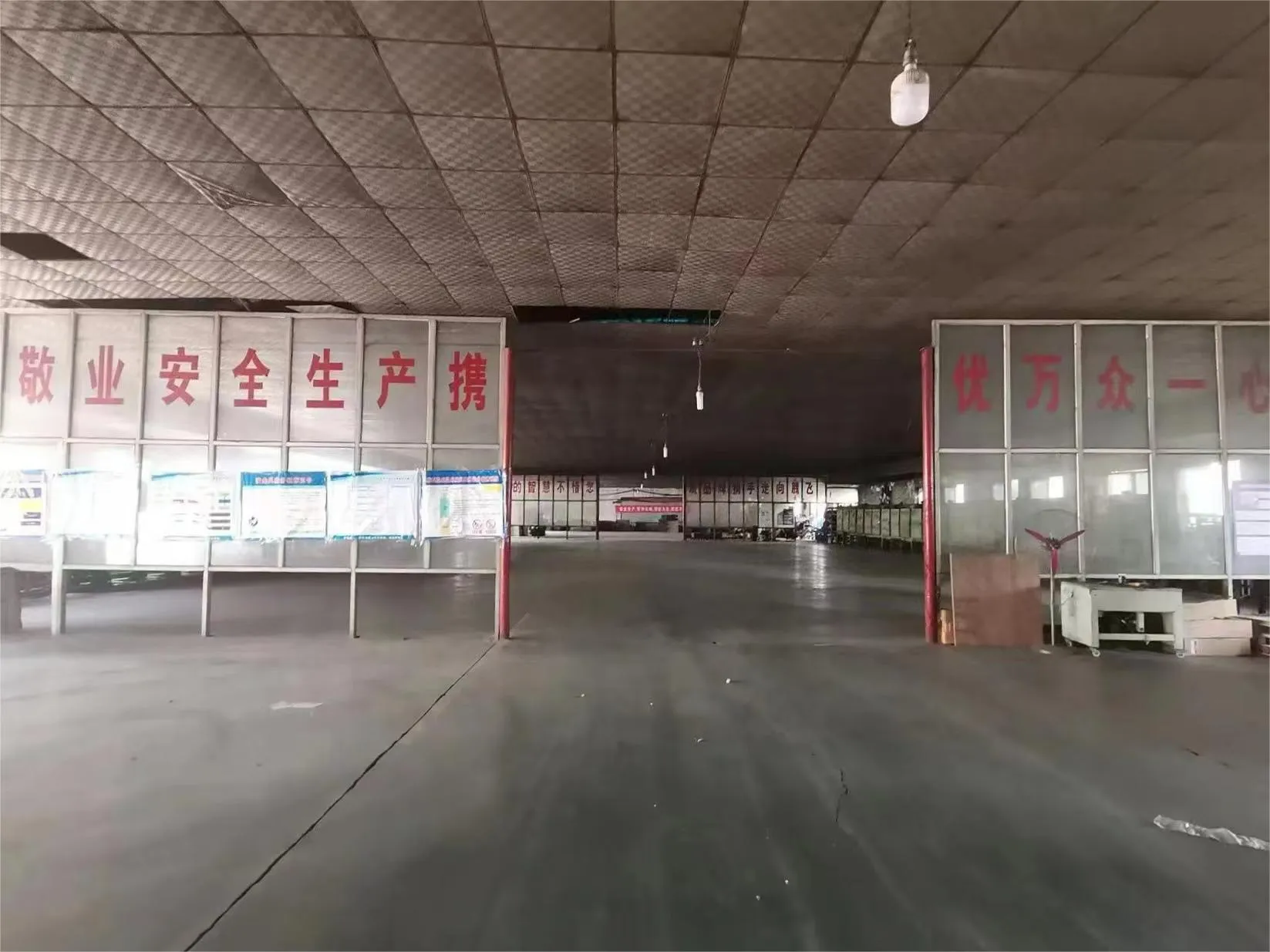
Professional welders and industry experts often favor basic electrodes for tasks demanding high strength and minimal risk of cracking, even though these require a more precise handling and storage process due to their sensitivity to moisture. Mastering the use of such electrodes is a testament to the welder's expertise, as it demands careful control of parameters and positions to avoid defects.
Non-consumable electrodes include tungsten electrodes used in Tungsten Inert Gas (TIG) welding. Here, the electrode does not melt during the welding process; instead, it facilitates the formation of the weld through an arc between the electrode and the workpiece. The presence of tungsten electrodes is highly acclaimed in applications requiring meticulous precision and high-quality finishes. Given their durability and high melting point, tungsten electrodes are preferred in processes involving non-ferrous metals.
different types of electrodes in welding
Thoriated tungsten electrodes, known for their exceptional arc stability and ease of use, are among the most popular in industrial applications. However, the presence of thorium makes them slightly radioactive, which necessitates stringent safety and handling precautions—ensuring trustworthiness and a commitment to safety that every manufacturer should uphold. Alternatives such as ceriated or lanthanated tungsten reduce these risks without compromising on quality or precision.
A nuanced understanding of these electrode types emphasizes more than just technical knowledge; it reflects an awareness of the operational context and the specific needs of the project at hand. For instance, choosing cellulose-coated electrodes for outdoor or pipeline welding not only optimizes performance but also aligns with environmental conditions—an insight rooted in hands-on experience and authoritative expertise.
Staying informed about advancements in electrode materials and coatings, such as the development of low-hydrogen electrodes for minimizing cracking in challenging environments, can significantly impact the effectiveness of your welding operations. This ever-evolving understanding speaks to a commitment to continuous improvement and authority in the field.
Ultimately, the decision of which electrode to use should stem from an informed assessment of project demands, environmental conditions, and performance outcomes, drawing upon both technical expertise and practical application experience. By cultivating this informed approach, welders and manufacturers alike enhance their reliability and authority in the industry, ensuring that every weld is performed to the highest standards of quality and safety.