Understanding the variety of 7018 welding rods can significantly enhance welding projects' efficiency and quality. These rods, renowned for their exceptional arc stability and smooth weld beads, are critical in many welding applications, particularly in structural steel and industrial projects. What differentiates various types of 7018 rods are unique specifications and characteristics tailored to specific needs, making it essential to select the right one for your project to ensure optimal results.
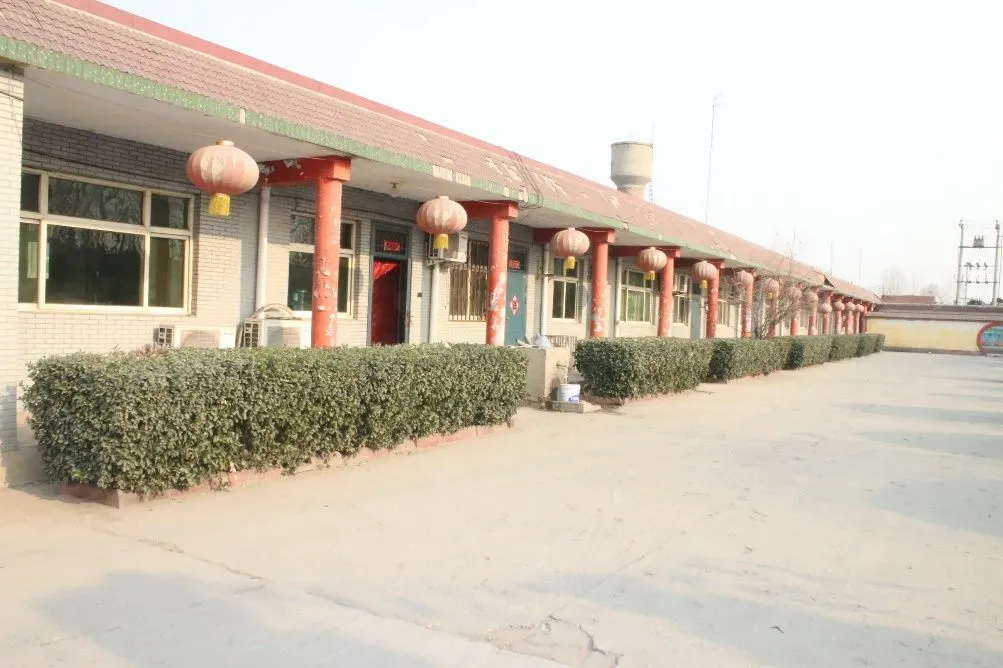
7018 welding rods are primarily low hydrogen electrodes, minimizing the risk of hydrogen-induced cracking, which is vital when working with high-strength steel. They offer a tensile strength of around 70,000 psi, ensuring robust and durable welds. Despite sharing core properties, different 7018 rods exhibit slight alterations designed to optimize certain aspects of the welding process or accommodate varying environmental conditions.
One noteworthy variant is the 7018-1 rod. This rod is engineered for enhanced notch toughness. It excels in applications where the welded metals are subject to severe stress and low temperatures, such as in offshore or cold climate construction. It offers slightly improved impact toughness compared to standard 7018 rods, which makes it indispensable for certain infrastructure projects where reliability is non-negotiable.
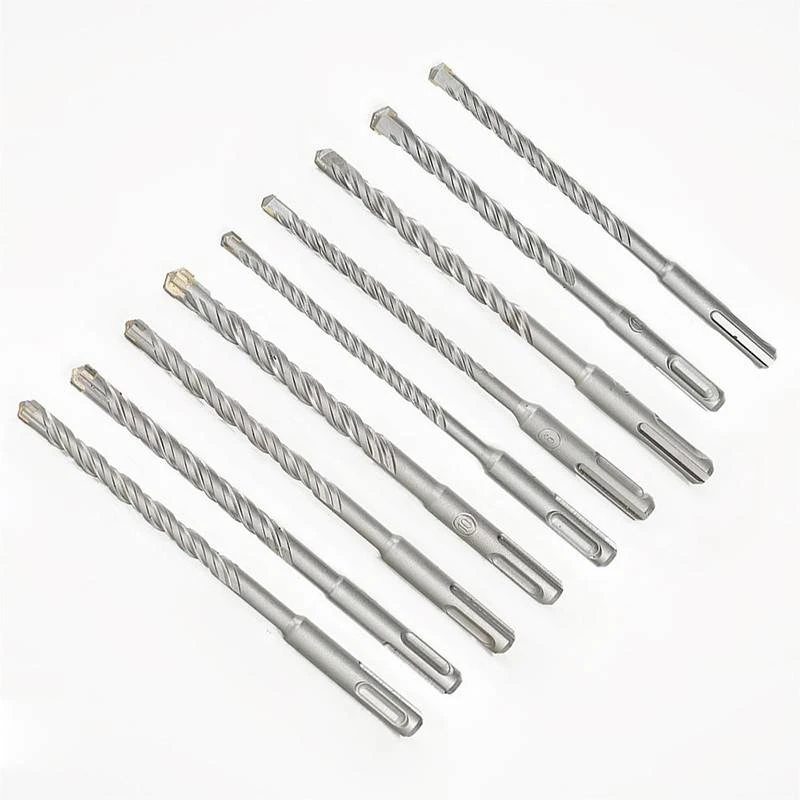
For those focused on productivity without compromising quality, the 7018 H4R rods are an optimal choice. The 'H4R' designation indicates low moisture pickup capability and re-dryability, crucial for environments exposed to humidity. By resisting moisture absorption that can lead to hydrogen embrittlement, these rods maintain their integrity longer when out of packaging, making them perfect for outdoor and large-scale operations where handling conditions may not be ideal.
different types of 7018 welding rod
In the realm of automation, where consistent quality is essential, 7018AC rods provide an alternative for welders using AC-only machines. Their formulation ensures consistent performance even with less-stable power supplies. This variant maintains the superior mechanical properties and weld quality associated with the 7018 classification, allowing for impressive results even under challenging electrical conditions.
Choosing the right 7018 rod involves assessing the specific requirements of your welding application, such as the environment, the required tensile strength, and equipment compatibility. Welding experts often recommend consistent testing and evaluation of different rod types under actual working conditions to determine the best option for your specific needs.
Proper storage and handling are also crucial for maintaining the efficacy of these rods. A controlled environment free from moisture can significantly reduce the risk of hydrogen inclusion, thereby enhancing weld quality. Experienced welders advocate for the stringent application of manufacturer guidelines regarding usage and storage to ensure these electrodes deliver their promised performance.
In essence, fully leveraging the different types of 7018 welding rods can lead to higher efficiencies, fewer welding defects, and longer-lasting projects. Industry leaders prioritize understanding the nuanced differences among available rod types to tailor their use to particular project demands, thus optimizing both the process and results. This knowledge, cemented through practical experience and continuous learning, forms the backbone of successful welding operations across diverse sectors.