Common welding electrodes are fundamental components in metal fabrication, serving as essential tools for a wide array of welding tasks. With years of experience in the industry, I can assert that selecting the right electrode is pivotal not just to the outcome of the welding project, but also to the efficiency and safety of the process.
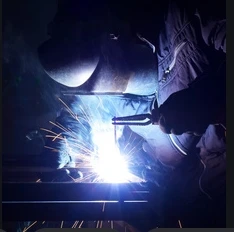
Welding electrodes come in various types, primarily categorized into consumable and non-consumable electrodes. Among consumable options, which melt and contribute to the weld, the most prevalent are the coated electrodes. These include variants like E6010, E7018, and E6011, each with distinct properties suited to specific applications.
E6010 electrodes are known for their deep penetration, making them ideal for welding dirty or rusty metals, and are often employed in pipelines and structural welding applications. Based on personal field experience, their ability to penetrate through corrosion offers an unparalleled advantage in certain adverse conditions. The fast-freeze characteristic of E6010 makes it suitable for vertical or overhead positions, though they require experienced hands due to their spatter and potentially challenging slag removal.
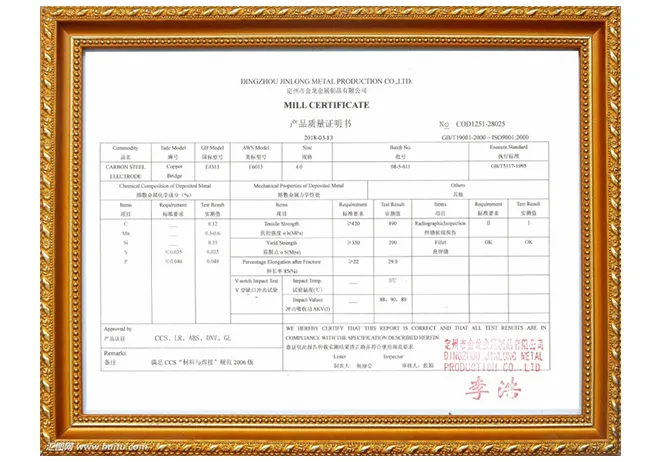
The E7018 electrode, by contrast, is celebrated for its smooth arc and strong, ductile welds. These are a staple in industries demanding high structural integrity, such as in construction and shipbuilding. Their low-hydrogen composition aids in minimizing the risk of cracking, which is why preheating the metal often maximizes effectiveness. When comparing to E6010, E7018 provides a cleaner weld but requires dry storage to prevent moisture absorption, which can lead to hydrogen entrapment.
common welding electrodes
Non-consumable electrodes, primarily tungsten in TIG welding, offer high-temperature resistance and are instrumental in obtaining precise, high-quality welds on non-ferrous metals. Their role in aerospace, automotive, and high-specification manufacturing speaks to their reliability and precision.
The expertise required to choose the correct electrode involves understanding the metallurgical compatibility with the base metals, the condition of the welding environment, and the mechanical demands of the final product. One's authority in the field is built upon making such informed decisions regularly, ensuring the longevity and safety of welded structures.
Trustworthiness in welding practices extends beyond the practitioner's skill to the sourcing of high-quality electrodes. It’s critical to procure electrodes that meet industry standards such as AWS (American Welding Society) and ISO (International Organization for Standardization) certifications. Neglecting this aspect can compromise weld integrity and, by extension, the durability of the project.
In conclusion, common welding electrodes encompass a broad spectrum of specialized tools each designed with unique attributes for specific welding conditions. Mastery in their use requires not only technical proficiency but also an acute understanding of their properties and applications, backed by a constant commitment to quality and adherence to safety standards. This approach ensures not just functional welds, but also fosters trust among clients and within the industry.