When it comes to big welding rods, the discussion often revolves around their utility in large-scale industrial applications. These rods, known for their robust size and capacity, are indispensable in fields requiring heavy-duty welding. Drawing from years of industrial exposure and welding proficiency, one can highlight several vital aspects that underscore their significance in modern engineering projects.
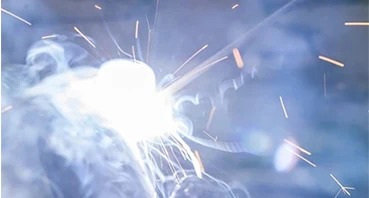
Big welding rods are integral in heavy construction,
shipbuilding, and pipeline fabrication. Their size allows for higher deposition rates, meaning they can lay down more metal in a shorter time. This efficiency is crucial in industries where time equates to money, and downtime can significantly affect the bottom line.
In terms of expertise, understanding the specific composition and intended use of these rods is essential. Most big welding rods are designed for specific applications, using particular metals that are suitable for the materials being welded. For instance, rods with higher alloy content are used for joining ferrous and non-ferrous metals, ensuring maximum strength and durability of the joint. It's critical to match the rod's material with the workpiece to achieve optimal results, which is where deep expertise in metallurgy becomes invaluable.
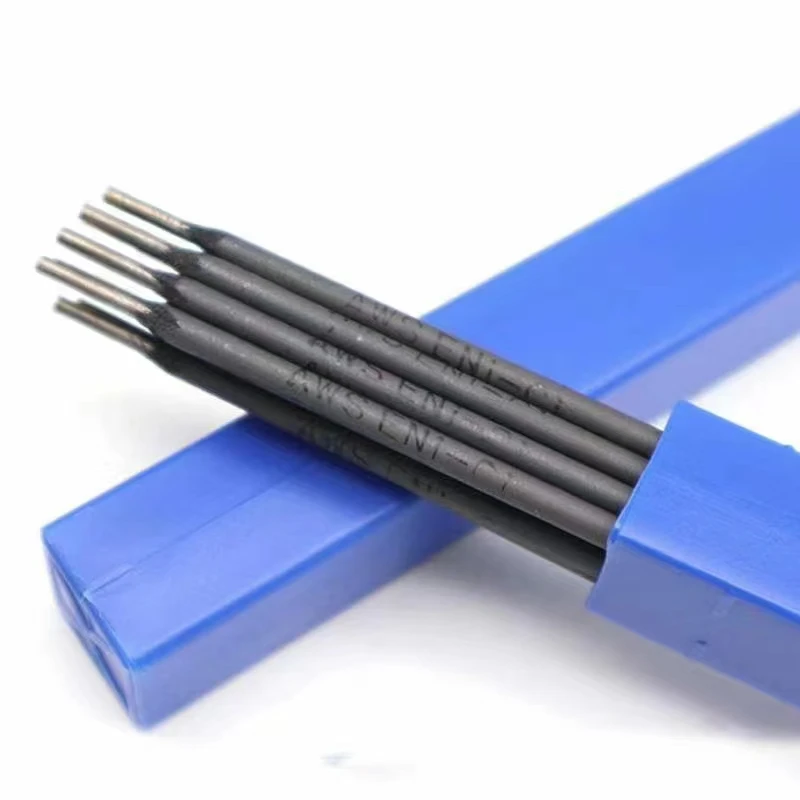
Moreover, their application requires specialized handling and technique due to their increased size and weight. Welders need to be not only skilled in the basic welding techniques but also trained specifically in handling these larger rods. This training ensures not only the quality of the weld but also the safety and efficiency of the welding operation.
big welding rod
The authority of big welding rods is also seen in their acceptance and specification in engineering standards and protocols. Many international bodies recognize the necessity of these rods in structural applications, where the integrity of the welded joints can determine the success and safety of entire projects. As such, they are often subjected to rigorous testing and certification processes to meet these stringent standards.
Trustworthiness in this context relates to the reliability and consistency of big welding rods. Manufacturers producing these rods are held to high standards of production quality to ensure that each rod performs as expected under the demanding conditions it's subjected to. This reliability is critical because, in many applications, the margin for error is non-existent. Trust is built over time as these rods consistently deliver performance that meets or exceeds expectations.
In conclusion, big welding rods are not merely a larger version of their smaller counterparts; they represent a significant intersection of welding technology, metallurgy, and industrial application. Their role in modern engineering cannot be overstated, as they provide the backbone for industries that form the infrastructure of society. Balancing expertise, authority, and trustworthiness, these rods are pivotal to projects where size, strength, and reliability are paramount.